Table of Contents
Chapter 1
Meeting and parting with Puncture preventative product.
1) First encounter with puncuture preventative in 1993:
I started my own business at the age of 30, and incorporated my company Nichiei Electronic
Industry Co.Ltd., at the age of 33 as a manufacturer of transceiver communications equipment.
However in 1971, the Nixon Shock caused the exchange rate to fluctuate greatly since then. Af-
ter World War II, the exchange rate was fixed at 360 yen to the dollar. Since then however, a
floating exchange rate system has been in place. In 1996, the exchange rate was 70 yen to the
dollar. The exchange rate increased more than fivefold in comparison with 360 yen. For compa-
nies manufacturing in Japan and selling abroad especially to the USA, it was very difficult for
them to survive. Exchange rates have risen sharply only between Japan and the US. The US
deliberately protects its domestic industry against exports from Japan, such as textiles and au-
tomobiles. This forced many Japanese companies to move their factories to China, where inci-
dent costs were cheaper. And this was because China was an economically weak state at the
time, and the exchange rate between China and the US was weak against the dollar. However
this was only possible for large companies that already had a solid economic foundation, not for
small and mediumsized enterprises. Therefore I stopped manufacturing in Japan and estab-
lished Alma Trading Inc. with the aim of trading overseas. In this situation, I once sold
some transceiver manufacturer's products to Europe, Sweden and Holland, through this connec-
tion, I came to know the company's president, Mr Kuroda.
It was the spring of 1993. Mr Kuroda asked me to help him sell a certain product. It was
unfamiliar in Japan and he wanted me to help him figure out how to market it. The prod-
uct was a puncture preventative. However it was also a product that I had never seen
before. The business was not started by Mr. Kuroda himself, but at the request of his sponsor.
Given the strong yen, he was not in a position to manufacture and sell products overseas, con-
sidering his position, I wanted to support him so that he could somehow succeed. To achieve
this, I diligently studied the products, thought about sales methods and conducted sales activi-
ties. As soon as I had a good prospect in Japanese market, I immediately started sales activi-
ties in the Asian region. This involved sales to China, Taiwan, the Philippines, Malaysia, etc.
However unexpected product complaints arose. An investigation into the cause revealed that
it was due to product separation. This issue has become very serious for us. Because we had
to stop operating completely. I had since been asked to visit the US manufacturers to talk with
them to negotiate a solution to the product separation problem, but I found that they did not
have the technology or the ability to do. They were Iraqis who had bought the manufacturing
technology to produce the product and had no knowledge or skills to develop it themselves.
While I was in the US, I looked for a manufacturer of puncture preventative products that would
not separate. However, no such information was available. I reported this to Mr. Kuroda. He was
then forced to give up his business activities. Thus my impression of a puncture preventative was
very sad, with only strong bitter memories.
2) Seeking Authenticity for the one that do not separate:
When I was doing my first market research in Japan on puncture preventative products, I re-
called information that there was a product called Perfect Seal, which is a non-separating
product for bicycles, not cars. Even if a product separates in puncture preventative vehicle
applications, it is not surprising that it doesn't separate in bicycle applications. This is because
bicycles and vehicles run at different speeds, therefore generate completely different centrifu-
gal forces on the tyres. However the product name perfect seal might have made me wonder
if the product would not separate? The idea crossed my mind that maybe they do not separate?
I was curious as to whether there really is a product that does not separate even cars. I was al-
so keen to find out if there really are products that do not separate, if so, for what reasons and
with what technology they are made possible. My curiosity drove me into action. I finally
tracked down its distributor in Tokyo. Then, as a favour to the president, he told me about the
company that manufactured the product. It is US Tire-tech Inc. I signed up for an appointment
and headed to Dallas Airport, Texas. It was May 1994.
They made me feel welcome. However I was not visiting as a tourist, but just to make a point:
Is there really a product for puncture preventative that does not separate? If this is true, I
would like them to explain to me with evidence, why and with what technology this is
possible. I told them that I visited your company just to find out. Gary L. Pledger, the presi-
dent of the company, asked me to attend a one-to-one training session with Sam, the
vice-president, from 9 am to 5 pm for three days, starting tomorrow. He seemed very
confident about his product, however, I was surprised that I was asked to attend a three-day
course. Because I had assumed that on the day of my visit, the briefing would be over. I was
surprised to find myself on a one-to-one course for three days, I gladly agreed to it. Though
I knew in advance, but in the morning, exactly around eight o'clock, I was violently sleepy.
It was jet lag. It was completely unexpected that this battle with sleepiness, was waiting for
me for three days. Somehow, apart from this unplanned battle, I managed to have a very
productive time. I thought I knew a bit about tyres because I drive a car, but when it comes
to work, the dimension of knowledge is completely different. In particular, it is about
truck tyres. I had seen them all my life, but I did not know about them. It was the first time
I had learned how hard truck tyres work in such harsh conditions through his lecture.
Of course, the corroboration of the product separation is also confirmed:
9 May 1990, as US tire-tech requirements; a Safety-Seal Tire was submitted to
the SOUTHWESTERN LABORATORIES. Conditioner, One gallon test request. The test period
was 21-25 May 1990. Among the various tests was a Product Separation section, which stat-
ed that at 5000 rpm for 15 minutes, there was no separation. It is stated that This, Gary
explained, is a centrifugal force large enough to separate blood into platelets, white blood
cells and red blood cells. Therefore, he explained, product separation does not occur, as
long as the vehicle is driven at legal speeds, even on motorways. For reference, the test
items requested included tyre puncture seals. There is also a report on corrosion testing of com-
mon wheel rim materials, including tests on aluminium and steel. Tests were also carried out as
Immersion Test of Inner Tyre Material and the test results for Rubber were also reported. I have
read the detailed test report from SOUTHWESTERN LABORATORIES and, in particular, heard Mr.
GARY's explanation of the product separation, and I consider that I can have confidence in the
product. Three dreamlike days passed in the blink of an eye. These three days of training,
have been so fulfilling that they have made my heart so happy that I have forgotten the
passage of time. I was able to learn about the workings of the new puncture preventative prod-
uct through this course. I was impressed by how well they work. Naturally, Mr Gary, the Manag-
ing Director, was informed by Mr Sam, the Vice Managing Director, about the content of the
three-day course and my product understanding and communication skills etc. On the morning
of the fourth day, I thanked Mr. Gary for the training, and also told him that all my doubts about
product separation problem had been cleared. With this, the purpose of my visit was achieved.
On top of that, I also learnt about the expertise of a new, non-separate product. I was sincerely
grateful.
3) An unexpected, a distributorship from US Tire-tech:
For some reason, Mr. Gary was very keen to persuade me to work as a Sole agent in the Pacific
Rim, including all Asia, which is certainly an attractive proposition in the trading business. I do
not know why, but he seemed very eager to sign up with me. Because he told me some confi-
dential information, which he had not disclosed to the outside world. He also told me that they
are currently in the middle of a five-year driving test to demonstrate 150% tyre life in coopera-
tion with Conoco fleets, a transport company. This is the fourth year and next year will be the
fifth year. He told me that the data from the last four years, all show figures of 150% tyre
life or better. And he strongly emphasised to me that puncture protection has moved
from being a product used to prevent punctures to a completely different product that sig-
nificantly increases tyre life. I couldn't help but be amazed at how he suddenly gave me
secret information about 150% tyre life when I turned up to find out if the non-separating
puncture preventative product was real. Why me? I couldn't understand why he was tell-
ing me such an important story to a peson he had never met before. Through Mr Kuroda,
became aware of puncture preventative products. However in my eyes, it is not something
I am interested in as a business. Because punctures themselves are becoming less and less
common. However when I learnt about the problem of product separation, I happened to
learn about a puncture preventative product for bicycles called Perfect Seal. And I thought
that somehow, because of the name Perfect, this product might not separate, so I looked into
it. The president of the importer assured me that this was indeed a non-separating product.
When I heard this, I decided that I would definitely like to meet the manufacturer of the prod-
uct and see it with my own eyes, in person. This is because I had previously visited the US
manufacturer of Mr. Kuroda's product for technical discussions on the issue of separa-
tion, and had also searched for manufacturers of non-separating products, but had been
unable to obtain such information. Therefore I couldn't believe it unless I met them in
person and confirmed it. The president of the import company, Mr Yokoyama, granted my
wishes. I was then able to visit US Tire-tech. But, I had never visited US Tire-tech before, and
Mr. Gary, the president of US Tire-tech, was very enthusiastic, told me that the puncture
preventive product would be a 150% tyre life product. A puncture preventative prod-
uct and a product that enables 150% tyre life are completely two different things in
my eyes. Even though they are the same product. I am not interested in puncture preventa-
tive products that prevent punctures, but I am interested in products with 150% tyre life.
For, I have a hunch that 150% tyre life is far more marketable. And this story has made
me positive about the Agent contract. The president, Mr Gary, was very pleased. We both
signed an agreement that Alma Trading Inc., would be the Sole Agent for the Pacific
Rim, including Asia.
4) Installation problem:
(1) The problem of the installation of puncture preventative inside the tyre.
(A) After the contract:
Through my sales activities, I ran into one problem. This was the installation of product into
the tyre. All puncture preventative manufacturers in the USA used a hand pump, similar to a
bicycle inflator, to install their product in the tyre. Apart from passenger car tyres, installation
in truck tyres is imposible by hand if you look at the installation time, it is absolutely impos-
sible to make it profitable. It is a mystery for me why this has not become an issue among
puncture preventive manufacturers. Assuming the use of truck tyres, there are three major
problems with the conventional method of installation with a hand pump.
(i) Accurate quantities can't be guaranteed. For the fibres can get caught in the pump valves.
(ii)The amount of product installed in the tyre is five times larger than a passenger car, making
it too time-consuming and unusable.
(iii)Even if the air pressure is set to zero, the physical strength required for pumping is so great
that it is also unusable in this respect.
Therefore, such installation methods do not work. If a person is employed, the business must
pay him or her a fee. But how much would it cost if it took a day to put the product into only
10 truck tyres? If it took a day, it would not be profitable. To my mind, it's not really a business.
(B) Developing an installation pump, Power Pump DC-10:
I set about developing an installation pump. The name of this pump is POWER PUMP"DC-10".
It is battery powered and can be fully charged in 40 seconds for an tyre 11R22.5(50 oz), and
can be used for 100 installations in a row. It is compact, portable and computer-controlled,
and can be filled automatically when the amount of installation is entered. Not only is it computer-
controlled, but we have also developed a Lock Valve Tool, that automatically grips the valve
head when removing the valve from the tyre and automatically releases it, when inserting
the valve. This was my eldest son Takanori, his first development work:
This power pump was very much appreciated by the agency people. It is a cool and smart
way for demonstration. But in my head I clearly see that this is not my ideal. It may be con-
venient for the person selling the product, but not for the user, I feel it is not ideal. This is be-
cause of the costs involved. The price of this pump is $5,000- per unit. For reference, the SELLA
Power Pump DC-10, the Lock Valve tools, and US patent application acceptance documents
are introduced here.
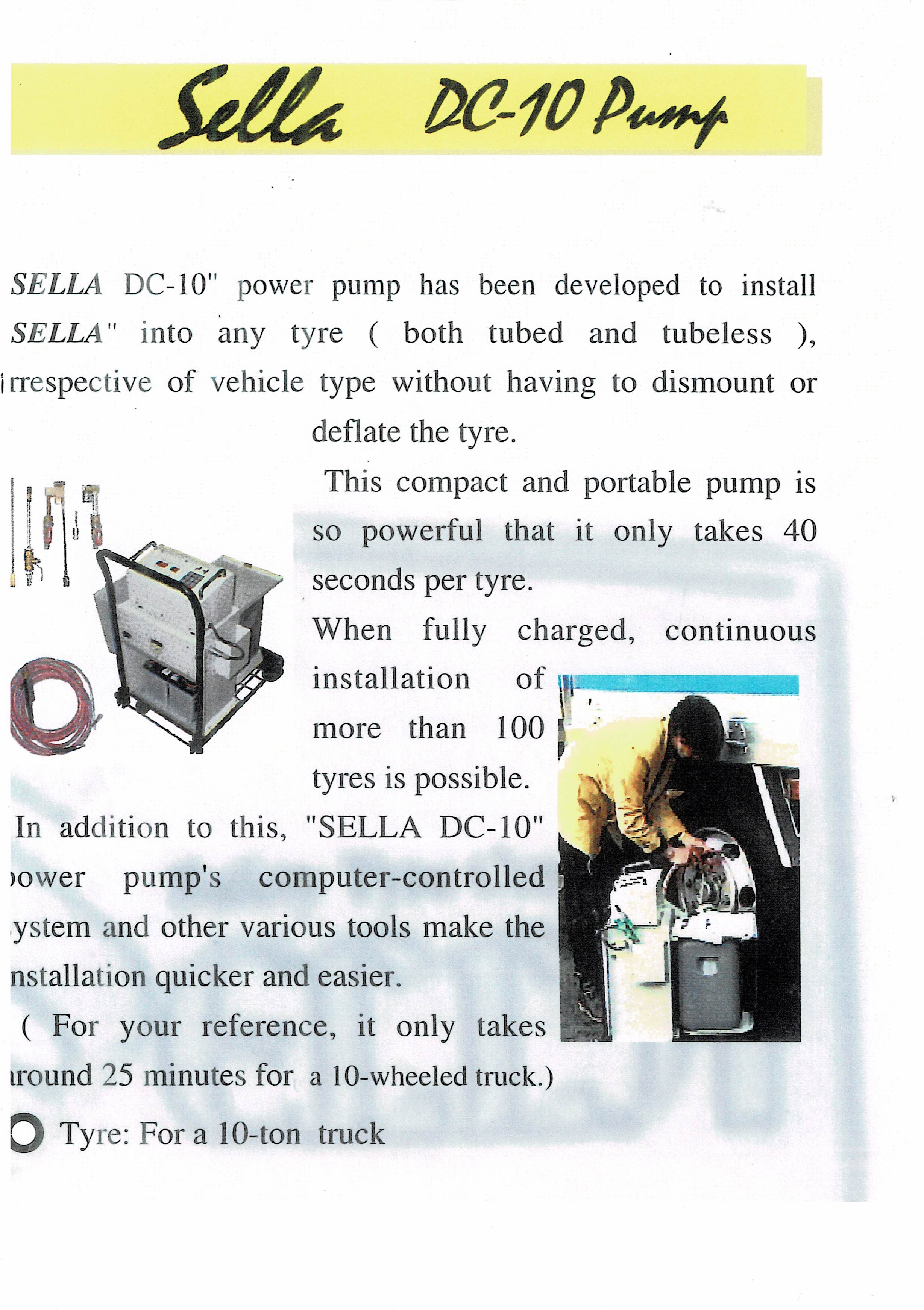
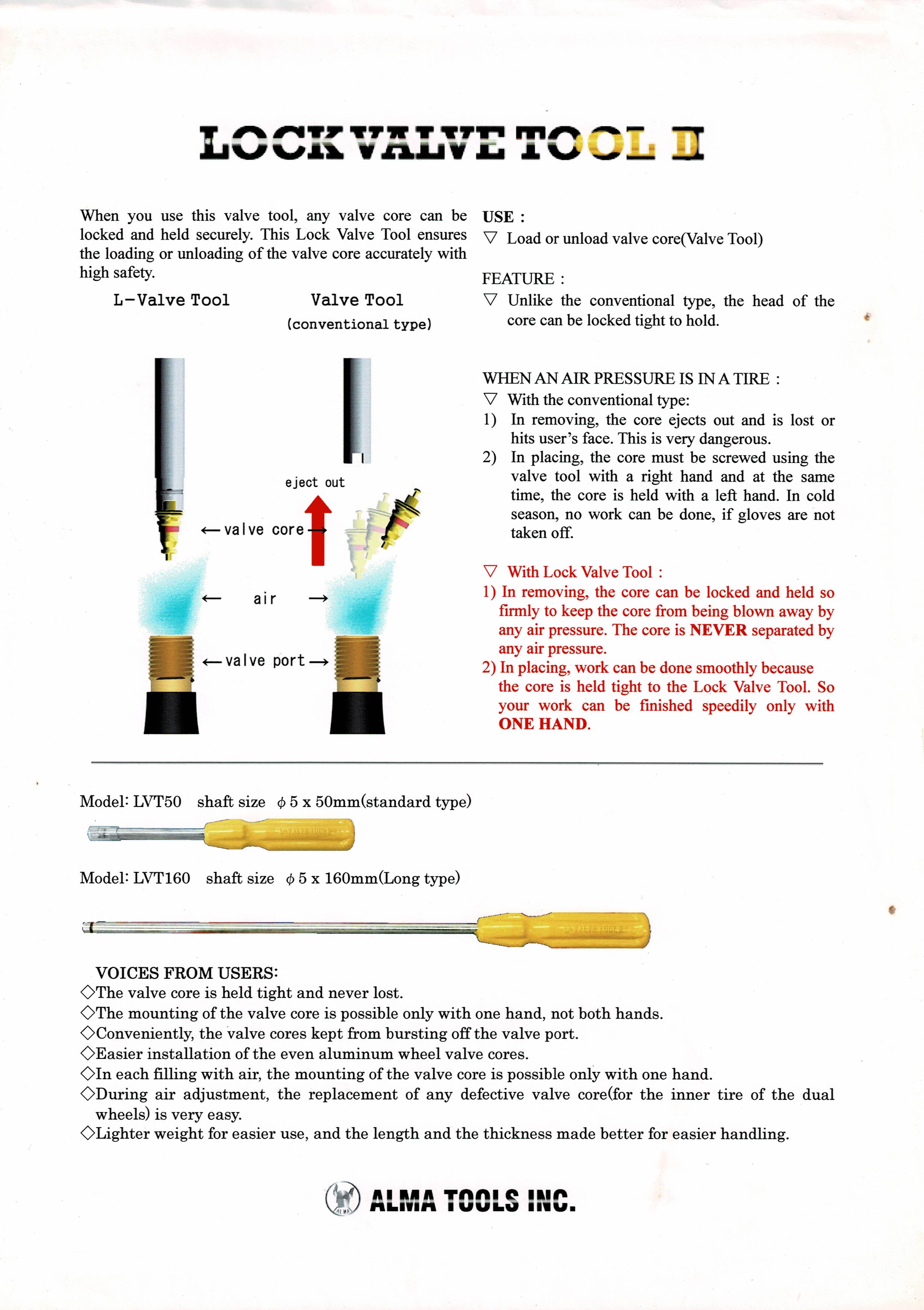
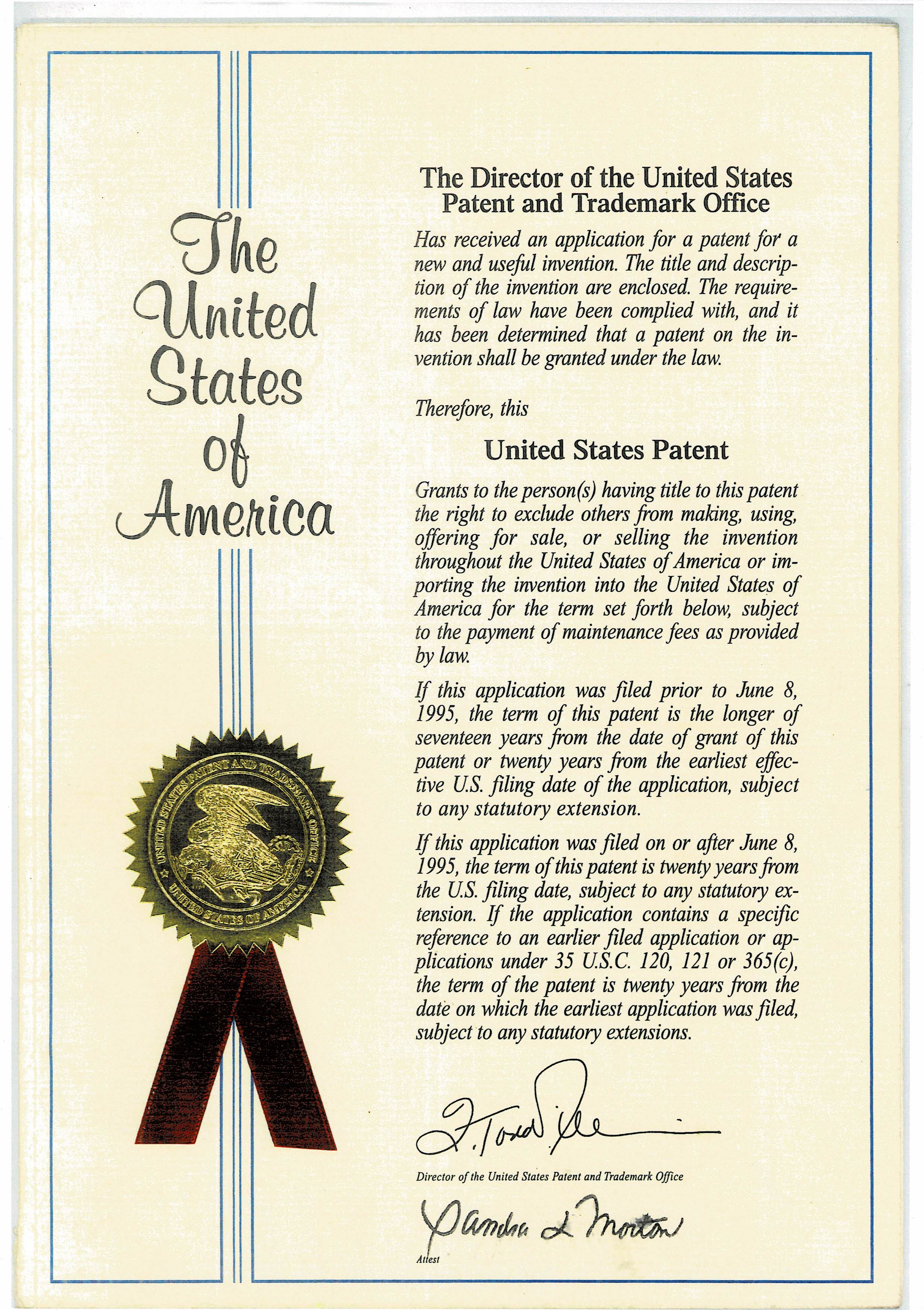
(C) Why a hand pump?
This is because it was necessary to install the product in the punctured tyre. However, times have
changed, and now that the product is no longer sold as a puncture preventative, but as a 150%
tyre life product. The purpose of use has completely changed. Therefore, the product's in-
stallation method must also change. From now on, instead of using a pump, be it a hand
pump or a power pump, there should be more suitable methods. My ideal installation for this
product, 150% tyre life, would be a zerocost, hassle-free installation. I will surely find a way
to do this.
5) Proven 150% tyre life based on data from five years of
road tests in 1995:
(a) Key witnesses to this momentous fact:
(1) US Tire-tech, manufacturer of this product.
(2) Dupont, the world's largest chemical company.
(3) Conoco Fleets, a transport company that co-operated with the driving data.
(4) Alma Trading, US Tire-tech's Sole Agent in Asia.
(b) Strange as it may seem; We have not contributed anything to 150% tyre life like some of
the other members. It was just a coincidence. It is therefore strange to be here as a witness
to 150% tyre life.
6) Dupont decided to sell the product on the world market:
With this proof of 150% tyre life, samples were sent to Europe.
7) Sample failures due to wheel rust:
Dupont's withdrawal and US Tire-tech's abandonment of production:
(1) A promising product is disappearing:
This incredible information filled my heart with sadness: as a 150% tyre life product, a promis-
ing product is disappearing. However, there were misgivings about this. For when I asked
for any scientific reason, how the no separation product could achieve a 150% tyre life.
there was no clear answer. The only explanation was that five years of driving data from
Conoco fleets had proven this. However their explanations did not answer any of my questions.
In fact, even raised doubts. It is too good to be true. How can a puncture preventive product be
into a 150% tyre life product? It's like magic. It is a mystery to anyone who thinks about it.
What on earth could be the reason for this? Their only answer is that five years of driving data
from Conoco fleets confirms it. There is no further explanation. Of course, I do not believe
that their data is false. However I can not honestly accept that puncture preventative products
are the only products that can make 150% tyre life. Because puncture preventative products
and tyre life 150% products are exactly the same product. What is the difference between
them? The only difference is whether the products separate or not. I can't help but wonder
why a difference of that magnitude would result in a product with a completely different intended
use. As a product, there is a difference between heaven and earth. The facts of the matter are
simple: the puncture preventative product is now separated by strong centrifugal forces in this
high speed era. This makes it unsaleable. US Tire-tech was the first company to successful-
ly manufacture a product that does not separate. And they discovered that their non-sep-
arating product increased tyre life by 150%. As this process shows, they didn't try to find
a reason, cause, or theory as to why no separation product could extend tyre life to 150%.
No, They did not at all, think about such things in the slightest. Therefore, this was an ac-
cident. Thus, they are unable to explain.
(2) In 1990 they should have tried to find out why:
It is unfortunate that the problem of rust on the wheels has arisen. However the problem al-
ways occurred regardless of Southwestern Laboratories' proof. Because their proof was incorrect.
However, I regret that in 1990 they should have tried to find out why 150% tyre life was
possible with their product, instead of asking Southwestern Laboratories to conduct product
separation tests and corrosion tests on the wheel materials, aluminium and steel. This is because
I believe that if the causes and reasons for 150% tyre life had been made clear by scientific
evidence, their business development would have been completely different. Because they
did not do so, they only accidentally became the discoverers of 150% tyre life. Because they
did not reveal the reason for it. If the explanation is backed up by an immutable principle, the
law of nature, i.e. the principle of science, no one can argue that it is a coincidence. Because
"To say that it is an immutable principle is to say that it is always happening". It does not
happen by chance. We must clearly understand the difference. Therefore, their explanation is
entirely speculative and unconvincing. Coincidence is only coincidence. It is neither a theory nor
an explanation according to scientific, i.e. eternal principles. Even if they prove 150% tyre life
with data over a long period of time, say five years, it is still just like a coincidence for many
people. For, people find it difficult to accept what they do not understand. Therefore, even if
only results are presented in the data, it is difficult to accept the results unless they know why
they are the way they are. Accordingly, coincidence cannot be replaced by an immutable
principle. The world's largest chemical company, Dupont could not do anything about it. No one
can place strong confidence in chance. As long as they manufacture and sell this product,
and 150% tyre life is a selling point for this product, I believe that scientific investigation of
the cause is an essential part of our sales activities. Therefore, I consider that they have gone
about this completely the wrong way.
Chapter 2:
Decision to take up the challenge of discovering the evidence for 150% tyre life
and establishing the scientific basis for 150 % tyre life:
1) My decision to 150% tyre life:
(A) Fateful meeting and choice with goods::
US Tire-tech Inc. and Dupont decided to get out of manufacturing and selling this product,
and among the four main 150% tyre life witnesses, the two biggest witnesses disappeared.
If I had not accidentally visited the manufacturer to verify the authenticity of the non-separable
product, this would have been the end of the story all over completely. Because, no one will
have attempted to solve this problem, except me. This is because only a very limited num-
ber of people know that puncture preventative products are 150% tyre life products.
Because the two main witnesses, (1)US tyre-tech, the manufacturer, (2)Dupont, the world's
largest chemical company, which decided to market the product on the world market, have left
the scene. The remaining witness is (3)Conoco fleets, a company that co-operated with US Tire-
tech for five years from 1990 to 1995 in 150% tyre life driving tests, and data collection.
(4)Alma Trading Inc. I have been the sales agent contractor for US Tire-tech for a short period
of time. Do we expect Conoco fleets, a transport company, to do research on the develop-
ment of wheel rust, a technology that does not exist world-wide? That is a complete impos-
sibility. So what do we do? No. How is this matter going to go? If things move, it is as a result
of someone acting with knowledge and wisdom to achieve a goal. Things do not change on
their own. Therefore, unless someone acts to solve this problem, no matter how much time pass-
es, the fact will not change. The 150% tyre life products will disappear with them. This is
the reality.
I reflect on all that has happened to me in the short period of time since I first became aware
of the puncture preventative products, I feel as if someone who knows the nature of my inner
spirit well is guiding me, here to this place. Because if I had not been given the opportunity to
be here for short period of time, I would never have known about this 150% tyre life product.
It is only by sheer coincidence that I am here. For I do not live in the United States. I am not
in the puncture preventative product business. It just happens that Mr Kuroda asked for my help.
My cooperation was shortlived because of the product separation issue. Moreover, I myself did not
consider the puncture preventative product to be an attractive business at all. I do not consider it
to be a profitable business in an era of low puncture rates. I would not choose a puncture preven-
tative product-related business, even in times of high puncture rates. Because it does not meet
my business requirements. I would choose a business that competes on the basis of valueadded,
cutting-edge technology and ideas. From my point of view, I don't see puncture preventative prod-
ucts as such a product. When I looked at the people at US Tire-tech, they never looked like people
who work for a development-oriented company. As an entrepreneur, I don't get involved in any-
thing that is not profitable. However, if it is a business that has potential, I am willing to take
some risks for it. Products with high added value that are difficult to manufacture and sell on the
world market in a situation of a strong yen, and which are also technically difficult to imitate. In
other words, Only one product in the world was my business policy. therefore, the fact that
I found out about US Tire-tech and signed a contract with them seems like a coincidence in
itself. And it was 150% tyre life that caused the coincidence. Without that story, I would have
left. Why did I decide that 150% tyre life was a aluable technology? I don't know. For I do
not have the specific information or knowledge to judge it. I just have a gut feeling as a
businessman.
There is no rust inhibitor technology in the world to solve wheel rust, and even Dupont, the
world's biggest chemical company, runs away from the problem, it is natural to wonder how a
small business owner with no chemical expertise and insufficient funds can do such a reck-
less thing. Therefore, I will be regarded as what a bold man I am, with no second thoughts.
But if there is great potential, even if there is no added value at the moment, if there is a possi-
bility that through our efforts, we can add value and make the product valuable, I am will-
ing to bet on that possibility. Why did I come up with this idea? It is something I realised
through bitter experience in my youth. It is that one should not look to others for the realiza-
tion of one's ideals. People have different thoughts and feelings, and each person lives his or her
daily life with his or her own thoughts and feelings. Therefore, I realised that wishing for the
realisation of my ideals will never be realised by others. if we want our ideals to be real-
ized, there is no other way than to strive for their realization by ourselves. Furthermore,
I know that heaven never gives us everything we want. It does so in order not to make us
lazy. So if there is great potential in it as a business - I will not run away from the problem
without trying, regardless of whether I succeed or not, even if there are great difficulties.
Be that as it may, so what can be done? Do I consider it inevitable that we will disappear
with them, or will I myself decide to keep this product and technology alive? I then decided
that I would first investigate the scientific basis and causes of what makes 150% tyre life
possible, and if I succeeded in finding that out, I would try to develop the remaining, non-
separating products and solve the rust problem on the wheels. Because I don't want to
make the same mistake as US Tire-tech and Dupont. I will try anything that is possible, but
I have no idea of trying anything that is not at all possible. Because I am a businessman.
2) Why does non-separating product allow 150% tyre life?
I set about research to scientifically clarify why. Before discussing this matter, I would like to
first clarify the meaning of the terms puncture preventive product and 150% tyre life, and then
summarise the problems faced by truck tyres today, before we start this paper.
(A)Words:The puncture preventative product we are about to describe is essentially the same
as the old puncture preventative product before. However, it needs to be adaed to today's speci-
fications. The reason for this:
@ to adapt to higher speeds and prevent product separation, and
A to adapt to tubeless tyres and prevent wheel rust. If these problems can not be solved,
it cannot be called puncture preventive today. And this allows a 150% tyre life to be achieved.
Why? Because today's truck tyres operate in harsher conditions than ever before. 150%
tyre life is compared to the normal tyres (including Retread tyres) you are currently using,
and we are not talking about absolute figures. This is because tyre life varies greatly depend-
ing on conditions. Naturally, as a professional driver and as a transport company, you are prob-
ably aware of this, but here is some data for your reference:
Information on tyre life:
a) Relation to the temperature:
Tyre life at 0℃: 100
Tyre life at 20℃: 70
In today's temperature environment, where global warming is a major concern,
the temperature of the roads on which we drive is also likely to have risen signif-
icantly, not just 20 ℃.
b) Relation to Braking:
a)Tyre life of 80km/h 100
Tyre life, 80km/h, but evry 7 km stop and start repetition 50
b)Tyre life, at 40 km/h, repetition of every 7 km stop & start 100
Tyre life, same speed, repetition of every 150m, stop & start 15
c) Relation to Road Surface:
Asphalt pavement 100
Concrete surface 87
Concrete rough surface 62
Gravel road 50
d) Relation to Curve:
No curve road, tyre life: 9,000km
many curve road: 1,600km
(Only 17.7%)
What do we learn from this information?
Tyre life becomes completely different by the conditions where, when and how driving a
vehicle:
When we say 150% tyre life, we mean that the tyre life will be extended more than 150%
compared to the conditions of the normal or retread tyre that you are currently operating.
The data will change as the driving location changes, as the driving time zone changes, even as
the driving season changes. Comparisons must be made under the same conditions.
(2) The two biggest enemies of tyre life:
(i) Incorrect inflation pressure: i.e. Under inflation, and Over inflation. This is because tyres
are designed so that at Proper inflation, the tread surface is in 100% contact with the road
surface. Hence, the tread wears least. Under inflation and Over inflation, the area contact is
partial, as shown in the diagram below, so that the entire weight of the vehicle is applied to
that small area, increasing wear in that area and reducing tread life. The life of the tyre is ulti-
mately the life of the tread.
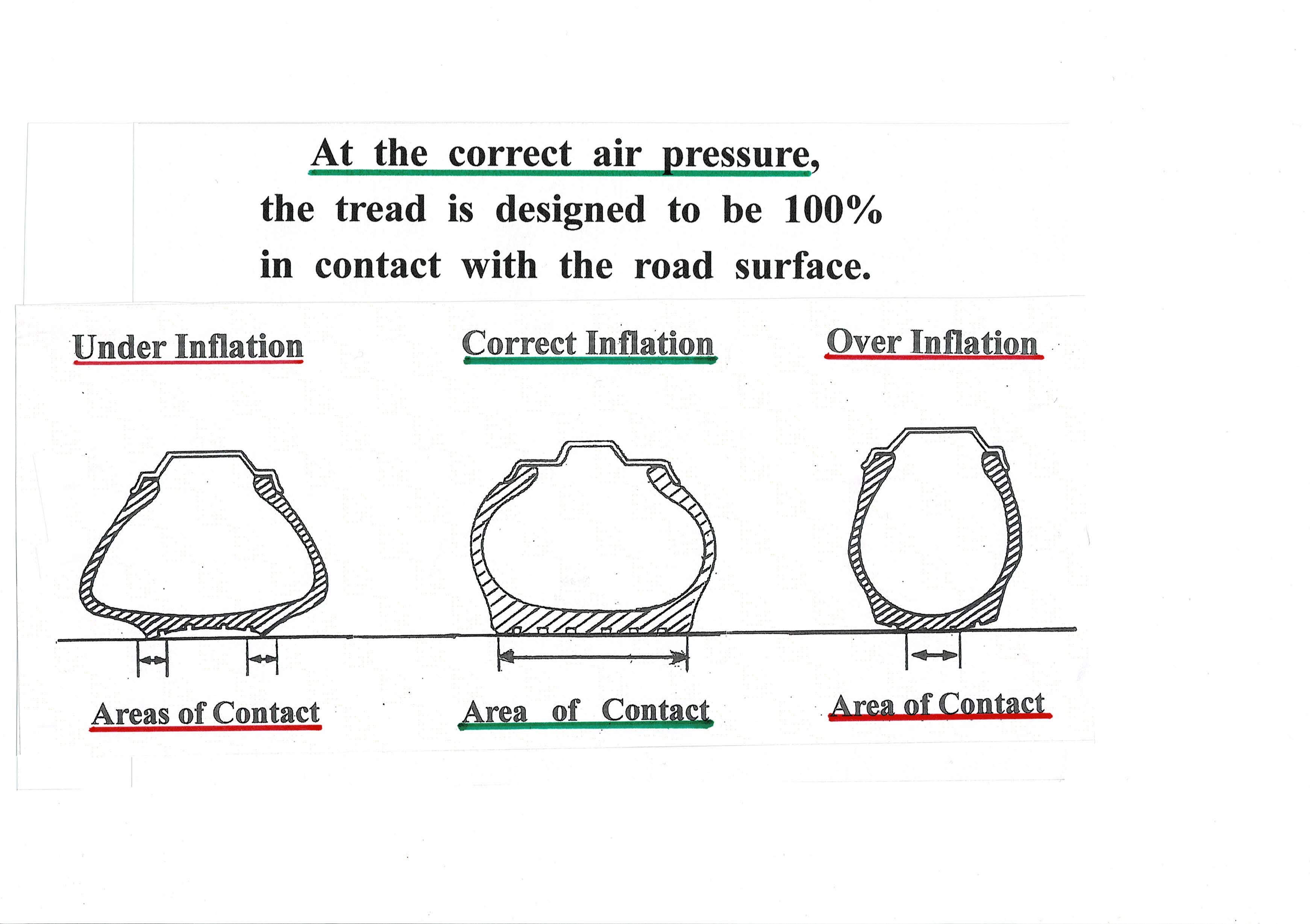
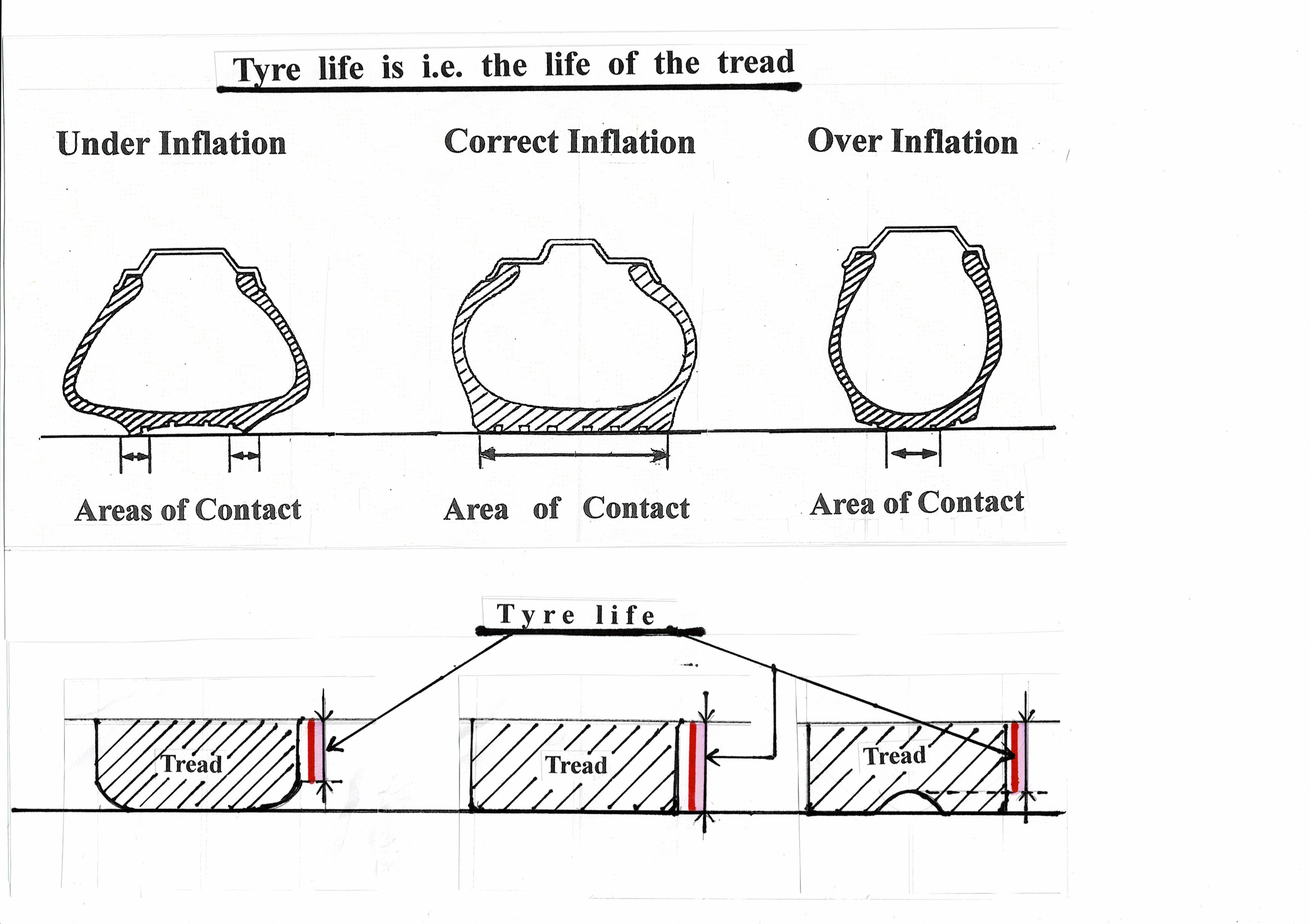
(ii) Heat kills tyres:
The second enemy is heat: rubber, which is a poor conductor of heat, can't transfer heat
smoothly. Therefore the heat constantly generated by the friction between the tyre and the road
surface can not be transferred and continues to accumulate in the tread area. Tyres are rub-
ber and rubber is heat sensitive. Excessive heat will cause the rubber to become soft, and
like a rubber eraser, the rubber will be scraped away. The life of the tyre will be accelerated.
Tyres wear out more in the hot summer months than in the cold winter months. This is not
the only way tyre heat can be bad, when tyre temperatures rise due to excessive tyre heat, the air
inside the tyre also expands due to the heat. The thermal expansion of the air causes the tyre
pressure to rise. And this results in over-inflation of the tyre. As already mentioned, this will
result in partial area contact of the tread with the road surface, leading to premature tread wear,
which will further shorten the tyre life. However this problem of excess heat in the tyre can
not be controlled by human will. This is the situation with truck tyres as it stands today.
In conclusion: Today's truck tyres operate in an environment where they have to run for
longer periods of time to carry heavier loads and deliver them further afield, at speeds so fast that
the puncture preventative products of old caused product separation. In other words, the higher
the speed, the heavier the load and the longer the running time, the more frictional heat is
generated in the tyre. Tyre temperatures are therefore much higher than before. Therefore
the problem caused by tyre heat seems to be becoming more serious.
3) The biggest problem that stands before us:
(1) Measuring the temperature of a specific place on a ro-
tating tyre:
If I say what a wonderful thing it would be, if we could measure the temperature of a specific part
of the tyre, everyone will look at me with a dubious eye. Because it would be so easy. So why is it
easy? Because we know that it is impossible to measure the temperature of a specific part of
the tyre once it has been driven. Therefore, the only way to measure the temperature of a spe-
cific part of the tyre is when the vehicle is stationary. What I want is for it to be in a running
state, not a stopped state. The reason for this is that if it were possible to measure the tempera-
ture of a particular part of the tyre while it is running, it would be easy to reveal a lot of things. For
example, the Dupont brochure describes it as; Allowing tyres to run cooler: Conducts heat
away from shoulder and tread area of tire and dissipates it through the sidewall and wheel:
and its authenticity can also be easily verified. But, their speculations have no scientific basis at
all. However there is no easy way to verify their truth. For it's impossible to measure the tempera-
ture of a specific part of the tyre while it is running. Therefore, people just assume that since
the world's largest chemical company says so, it must be so. The heart of this issue is that it
is impossible to measure the temperature of a fixed point on a running tyre. Therefore no one can
be sure how the heat generated in the tread is transferred. Therefore, solving this problem
is a top priority. If this problem is not solved, we will not be able to go any further. In any case, it
seems necessary, even tyre manufacturers to measure the temperature of the tyre as it ro-
tates, and when I met and spoke with Mr Shikada, a former engineer on the linear bullet train
for Bridgestone Tyres, two years ago, I asked him about this point and he replied that manufac-
turers are using temperature sensors embedded in the tyres and transmitting them via ra-
dio waves. Otherwise measurement would be impossible. However, like tyre manufacturers, I
do not have the luxury of being able to spend the necessary funds on research materials. There-
fore, I have to use my head instead.
(2) Great inspiration for the facts.
How to measure the temperature of a specific part of a rotating tyre? But, my mind could not
come up with a good idea. At first I was only concerned with measuring the temperature of the
tyres while they were running to investigate heat transfer, however gradually I started to see
things as they are. It was then realised by inspiration that the tyre, when running, is both a
heat-generating and a heat-dissipating body. Because, during driving, heat is generated due
to friction between the tread of the tyre and the road surface. And this happens continuously while
driving. Therefore, the tyres can be said to be heat-generating bodies, same time subject to
strong winds. And they are cooled by that wind. Tyres can therefore be called heat dissipat-
ing bodies. This means the fact that tyres are both heat-generating and heat-dissipating bodies at
the same time. Therefore, even if it were possible to measure the temperature of a specific part of
the tyre, it would be of no use to examine the temperature progress during this process.
I have noticed that the important thing is how much heat is left in the tyre as a result of si-
multaneous heat generation and heat dissipation, and the difference between the two.
I have come to the following conclusion:
If the amount of heat generated is the same, the tempera-
ture of a tyre that has stopped running, should differ due to
the cooling effect during that period.
Following this idea, I thought that by measuring the amount of heat by the stopped tyre, it
would be possible to determine the amount of heat remaining in the tyre as a whole.
According to this concept, it is possible to measure the amount of heat calories a tyre has, af-
ter driving for a certain period of time, the vehicle is stopped, and the temperature of the fixed
points of the tyre is immediately measured. In this way, the difference in cooling effectiveness
can be clearly demonstrated by the data.
If one wants to measure the remaining heat calories of a tyre strictly as scientific
data, it is best to prepare two identical water tanks in advance, remove the tyre as
soon as the vehicle stops, place the tyre in each tank and measure the change in
temperature of the water in the tanks.
However, it is not possible to do such a thing. Therefore we decided to do it in a similar, but practi-
cally feasible way. We have confirmed with experts that the comparative data will not differ sig-
nificantly as long as the measurements are made under the same conditions. We used a
high-performance thermometer to measure the temperature accurately in a short period of time,
with the aim of reflecting the facts as closely as possible in the data.
(3)Annotation:
At this point, our puncture preventive product, SELLA, is not a finished product. You might won-
der why it is being used in a driving test to take data. However, this test is on public roads, where
speeds are restricted to 60 km/h or less. It is not a product separation test at high speeds, nor
is it a wheel rust test. The puncture preventative product has a very simple specification. It con-
sists of fibres to seal the puncture, water and a dispersing agent to evenly distribute the fibres.
Antifreeze is added to the product to match the operating temperature. For example, the standard
product is set at -35℃ and the proportion of ethylene glycol used in the antifreeze is 50%. There-
fore, the specification for conventional puncture preventative products is a 50% aqueous solution
containing fibre. However, it's somewhat viscous and is not an aqueous solution, but rather, to put
it bluntly, a loose gellike state in which the fibres are uniformly dispersed. If this is difficult to imag-
ine in concrete terms, you can simply imagine a carpet. In other words, just imagine a uniformly
distributed layer with a fibre, a carpet. Imagine a carpet that conducts heat well, sticking to the in-
side of the tyre, on the tread and on the 3-40% part of the wheel width, but not up to the wheel.
Aside from wheel rust issues, how on earth did US Tire-tech succeed in producing a product
that does not separate at high speeds? The general idea is that if the specific gravity of the fi-
bres and the chemical solution are the same, or as close to the same as possible, they will not sep-
arate. Of course, if the specific gravity is the same, even if a centrifuge is used, it is true that dif-
ferent substances cannot be separated. However, the world is not that simple. Why did only US
Tire-tech succeed and no one else? When I first met Gary, the president of US Tiretech, I asked
him for clarification as to why your product does not separate, he gave me what I wanted, of
course, not manufacturing specification, but by Laboratories'report. Before he could do so, how-
ever, he asked me to sign a non-disclosure agreement. Also, when after I signed the Sole
Agent Agreement, he showed me around the company. However, when we came to the front
of the factory, he told me that he could not show me inside the factory. So, he was very careful
to ensure that this technology was not leaked to others. Thus, I am not even able to imagine
their specifications. It is therefore in a position where it has to go through a series of experi-
ments, starting with basic specifications. The puncture preventive product is essentially a sealer.
The first requirement of the product is that the fibres move quickly and pneumatically into the
puncture hole and seal the hole. If it loses this function, it is no longer a puncture preventive prod-
uct. Therefore, even if the product is non-separating or wheel rust-preventive, the specification
must never be such that it interferes with this function. Without such fluidity it would not work as
a puncture preventive product. The more chemicals are added to achieve the desired effect, the
more the fluidity is impaired. A simple specification is more difficult to achieve than a com-
plex one.
(4) Prepare to take data according to this method.
(a) Firstly, we asked "the Japan Automobile Federation for advice:
How long we should drive at full load, as a minimum, to get data on the amount of heat
generated by friction between the running tyre and the road surface, which accumulates
as excess heat in the tread of the tyre? Their answer was one hour running enough.
(b) To ensure objectivity in the data:
I decided not to take the data in Japan, but in South Korea in different country. At that time,
radiation thermometers were still rare, so I brought a high-performance radiation thermometers
from Japan to Korea. And I taught them how to use them. They prepared a Volvo 20-tonne
dump truck, fully loaded, at my request. In advance, the road to be travelled was studied and
an hour after our departure, our final destination was the large parking lot of a large restaurant
at the top of the pass. We made our pre-departure preparations. We installed 50 oz of SELLA in
one of the front wheels of the dump truck. Tyre pressures were also checked and we were ready
to start. 1996, 27 August, weather cloudy, outside temperature 27℃. Started at 9 am from
the starting point in Busan, the second largest city in South Korea, for data collection. We
followed the truck in a separate car, together with people from the company who had helped us to
collect the data. As planned, an hour later, the truck was parked in the large parking lot of a res-
taurant at the top of the pass. As soon as the vehicle stopped, I asked them to start measur-
ing the temperature of the tyre treads, sidewalls and wheels at the points I had marked for
30 minutes, according to the schedule.
4) This is the DATA that has been produced in this way.
This data was obtained under exactly the same conditions, i.e. same ambient air tempera-
ture, same road, same time, same vehicle, same driver, same driving speed and same road
operating conditions. Therefore, Thus, both Normal tyre and SELLA installed tyre data were
taken under exactly the same conditions.
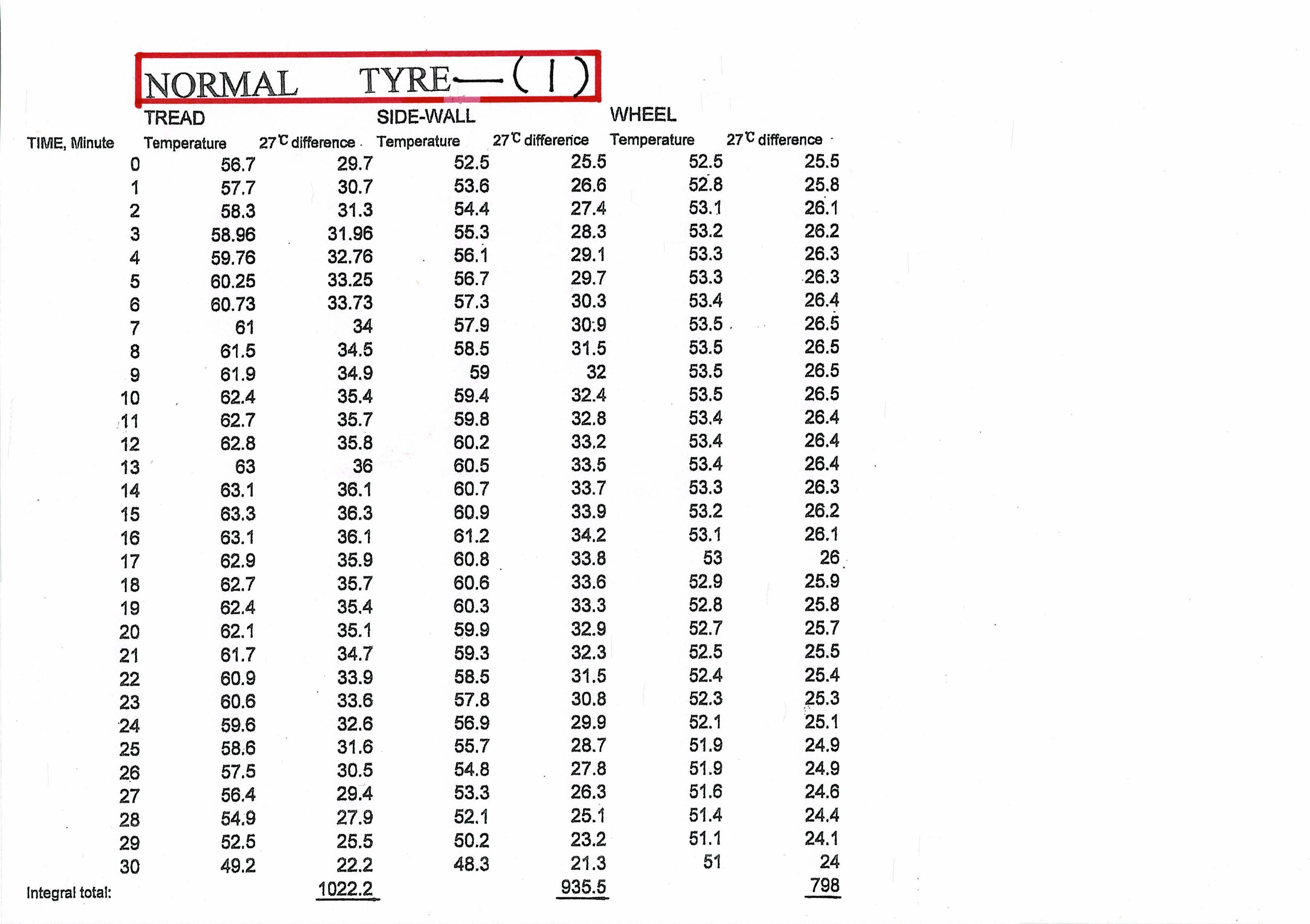
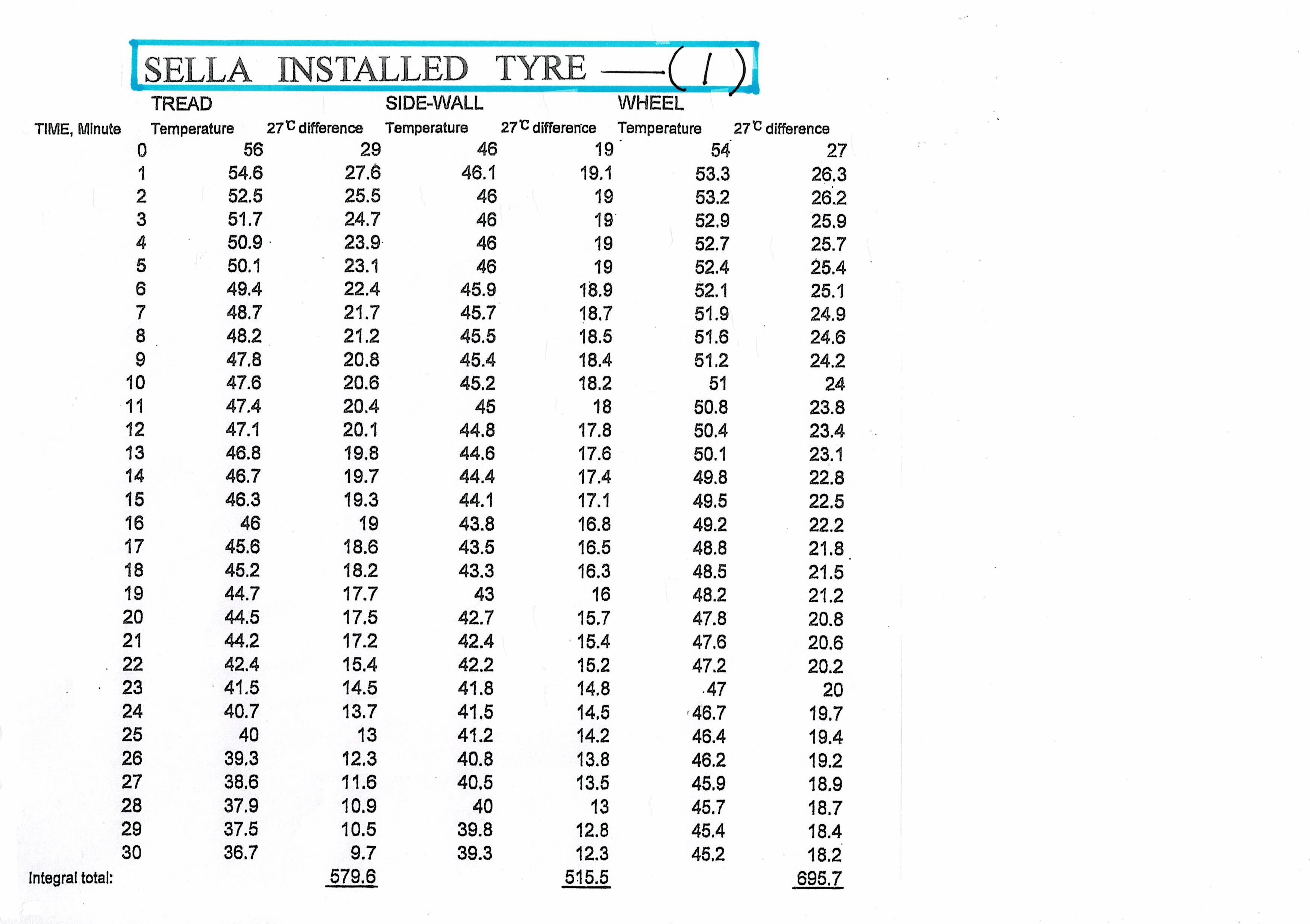
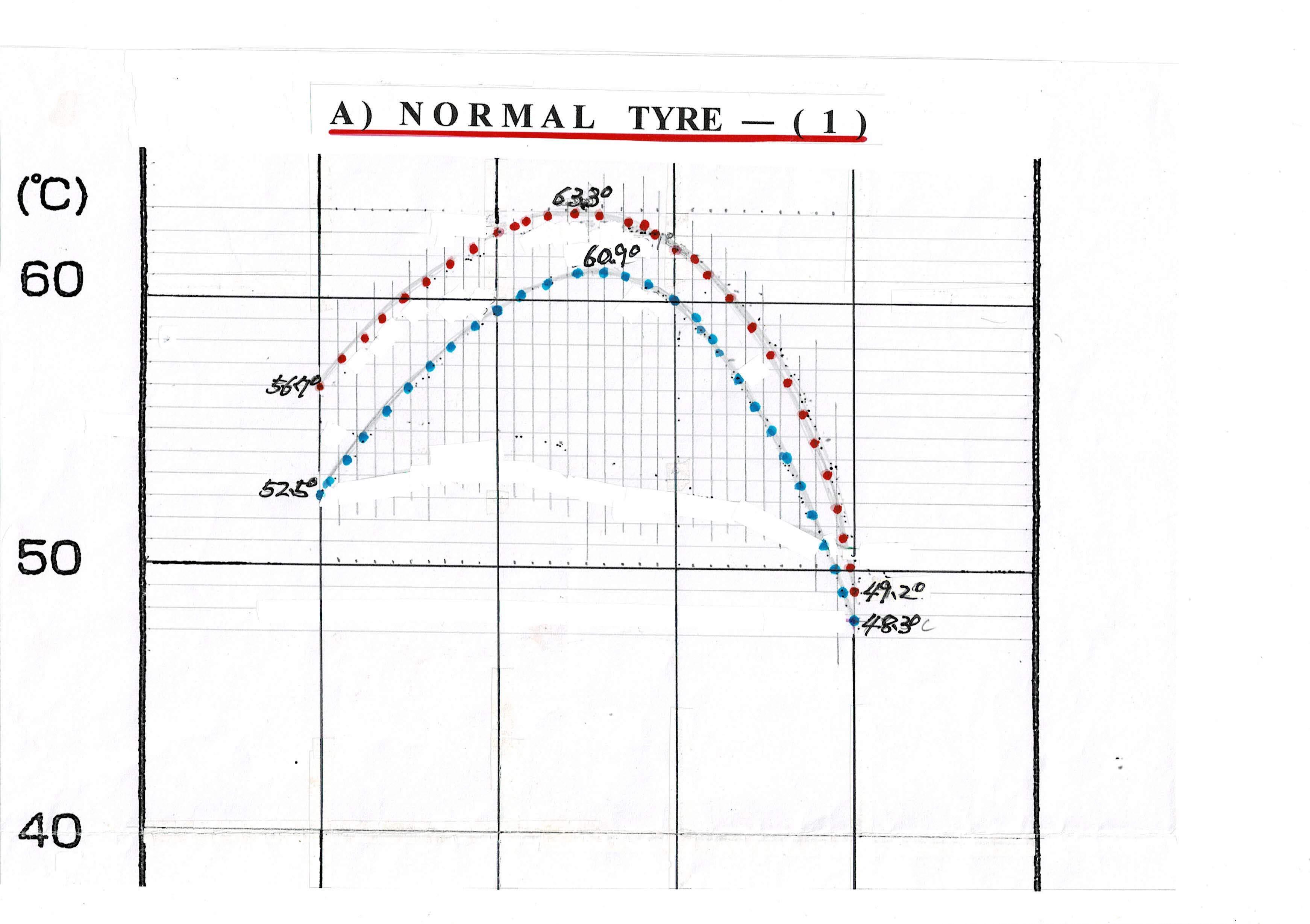
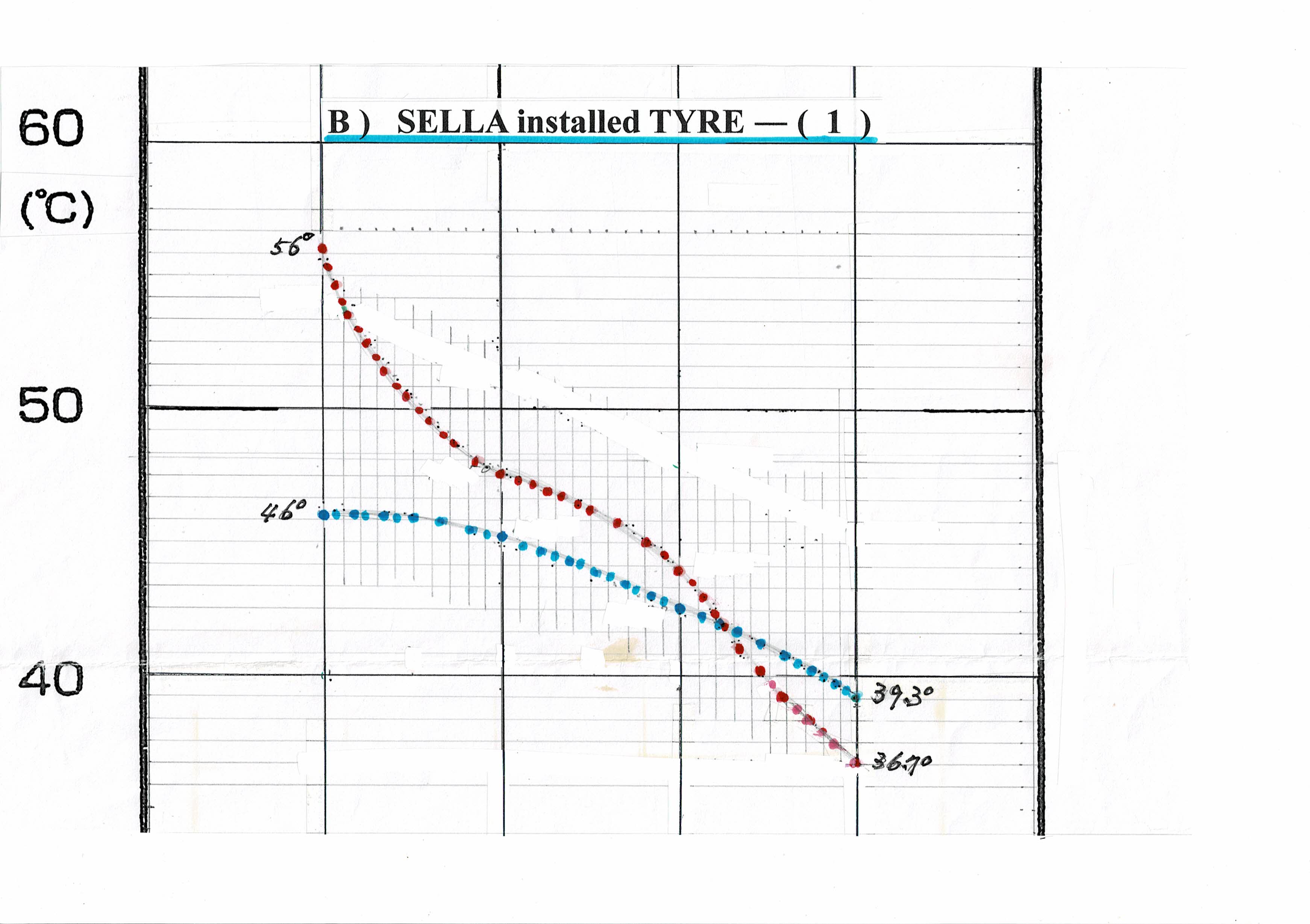
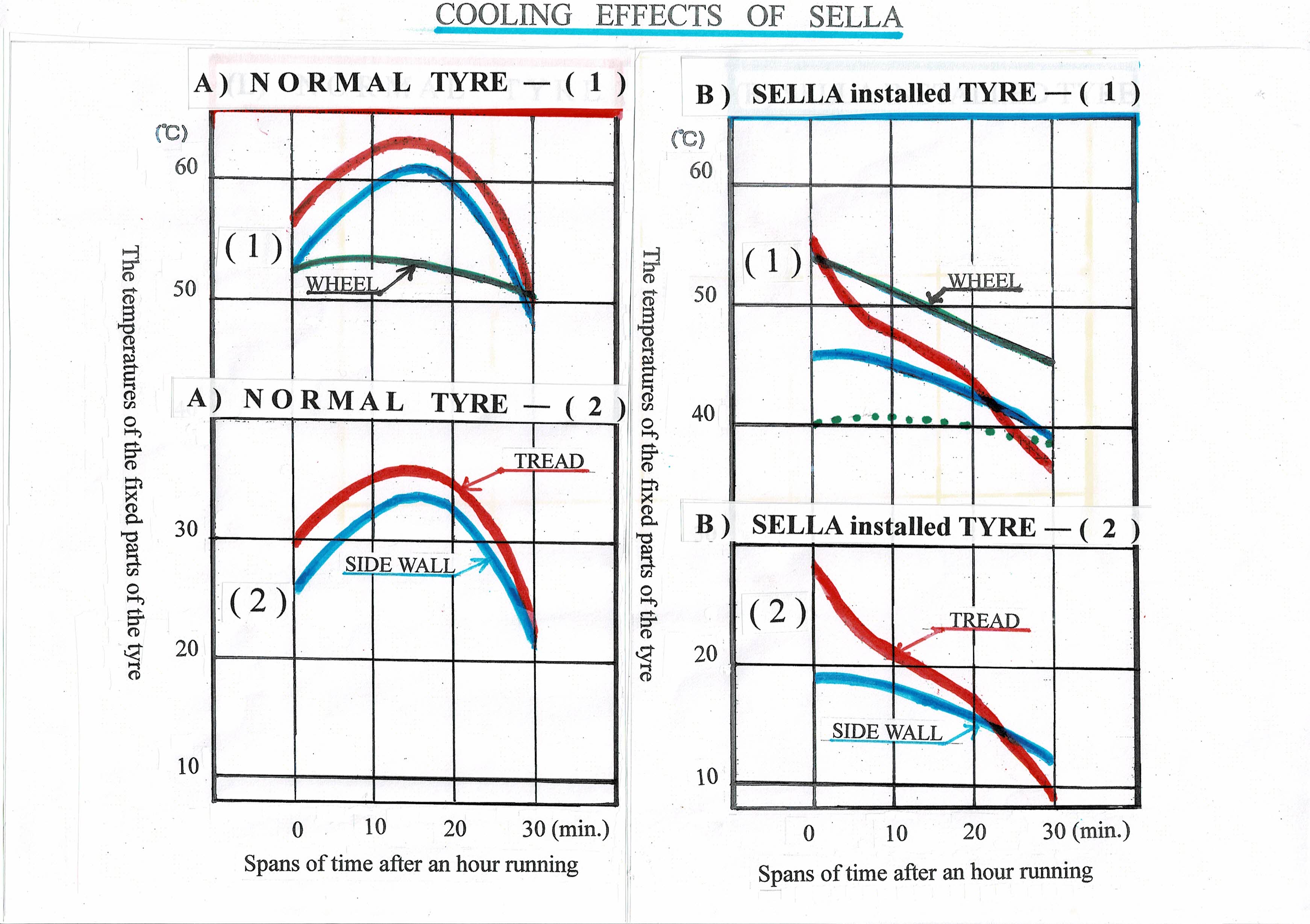
5) Find the AMOUNT OF HEAT stored in the tyre:
(1) Tyre temperature data is not the heat value itself.
To obtain the heat value, the ambient air temperature, 27℃ must be subtracted from the tyre
temperature. We have noted the temperature of the tyre over a 30-minute period and to the
right of that, minus 27℃, and the integral values are given below.
The total calories content of the tread section of the Normal tyre is[1022.2].
In contrast, the total calories content of the tread of the SELLA tyre is [579.6].
This means that SELLA tyre is 1022.2 - 579.6 = 442.6 ÷ 1022.2 = 0.432, indicating that
SELLA tyre is 43.2% more cooling effective than Normal tyre.
Isn't this a great cooling power? This is because when normal tyre is 100℃、
SELLA tyre is 100 x 0.567 = 56.7℃、and does not go up to even 60℃.
(2) Data comparison between Normal tyres and SELLA tyre:
Data on the amount of heat stored in the same marked areas of the tyre:
tread, sidewalls and wheels of the Normal tyre and the SELLA installed tyre are shown below:
Measured point: Normal tyre SELLA tyre
Tread:(calorie) 1022.2 579.6
Difference: 442.6 43.29% down
Sidewall:(calorie) 935.5 515.5
Difference: 420 44.89% down
Wheel:(calorie) 798 695.7
Difference: 102.3 12.8% down
This data is very groundbreaking! Because it is the first time in the world that
the cooling capacity of a Puncture preventative product has been specifically and
on a scientific basis clarified.
Of note is the cooling capacity of the tread section. Even if the temperature of the normal
tyre reaches 100 ℃, the SELLA tyre is at 56.7 ℃ and does not reach 60 ℃. When looking at
facts like this, it seems as if we have been able to glimpse the greatness of puncture preventa-
tive products. And the story of 150% tyre life does not seem to be a lie at all. I believe that
the data taken by US Tire-tech in cooperation with Conoco fleets for the five years 1990-
1995 should be something that you will find reliable.
As one of the approving parties, I cannot deny that fact. And I, as one of the approvers of
that fact, have been fighting to prove it until now. For, it cannot escape because it is the
truth.
(3) Why are the wheels cooled by only 12.8%?
I questioned the Dupont brochure's claim of a scientifically unsubstantiated theory: heat is
transferred from the tread to the sidewalls and dissipated through the sidewalls and wheels.
I then put the wheels into data capture to confirm this. And the data clearly showed that the
tread heat was not dissipating from the wheels as we had surmised. The main reason for
this is that SELLA, a puncture preventive product, does not reach the wheel. Therefore, It is
clear that wheel temperature is influenced by the temperature of the air inside the tyre
which is cooled by the SELLA. That is the meaning of the 12.8% Cool down compared with
Normal tyre. If the SELLA had reached the wheels,the cooling effect would be more than 30%
according to the data and not in the 12% range.
6) Testimony on data relating to SELLA installed tyre:
If under the same conditions, one of the two sets of data obtained is acceptable,
the other is likewise acceptable, even if it is beyond his knowledge.
This is the true scientist.
Technical Adviser Teijiro Wakatsuki
7) Technical Adviser, on Teijiro Wakatsuki:
He is a highly qualified engineer who graduated with honours from the University of Tokyo
Faculty of Engineering, one of Japan's top-ranked universities, and is indispensable to our
company which aims to develop products that are "Only one in the world". However, I only
told him that I would be assisting US tire-tech, the first company to successfully manufacture a
product with no product separation as their Sole agent for Asia. However, puncture preventative
product, is a simple product with fibres uniformly dispersed in a water-soluble liquid. And I was in-
terested in US tire-tech's product, the first to successfully manufacture a product with no separa-
tion, which enables 150% tyre life, and that I would be assisting them as their Sole agent for
the Asian region. However I did not ask him anything about my question of 150% tyre life. Be-
cause US tire-tech has no explanation as to why a non-separating puncture preventive prod-
uct can achieve a 150% tyre life, and their rationale is that five years of driving data from
Conoco fleets showed 100% and nothing more. With answers like these, I have no way of
consulting him. In other words, I can not consult him as a technical adviser, because I don't
have a clear idea of what the cause is. He is an excellent technician. I am well aware that, while
he can give clear answers to concrete matters, he can only give vague answers to vague and am-
biguous matters. The reason I had not consulted him before was that US Tire-tech's explanation of
150% tyre life had no scientific basis and I was too embarrassed to consult him. But, this time,
data was taken and, for better or worse, scientific evidence was obtained. Finally, I am at a
level where I can discuss the SELLA case with him.
I showed him the data. After examining the data, he told me, looking at this data, he finally
understood what SELLA was all about. And he said, this is a great product. And to my surprise
he saw through the nature of SELLA because it is water(water-soluble), which is the reason
why I could get such great data. He also said that there was no possibility of getting such
data with anything other than water. I had always assumed that chemicals were not his area of
expertise. However he has expert knowledge of the properties of materials, such as the ther-
mal conductivity of tyre rubber, water and other chemicals. He instantly understood that
because SELLA is water soluble, heat transfer takes place within the tyre, enhancing the
cooling effect. He was able to determine the nature of the SELLA effect just by looking at
the data I showed him. His explanation helped me to understand the cause of the high cooling
effect of the SELLA. This established the theory as to why puncture preventive products can
have a tyre life of 150%.
Our technical adviser, Mr.Teijiro Wakatsuki said "This data is everything.
This data shows what SELLA is all about. He then went on to say further,
"If it were not for this data, he would not believe me, no matter what I said.
This is a natural attitude for an engineer".
Chapter 3:
Battle for no separation product:
1) Working to secure development funding:
The world, of course, does not expect things to go according to our plan. The older we get,
the more experiences teach us about the realities of this world. But still, one must look for-
ward to the future and proceed according to the plan. For, if one does nothing for fear of
failure, one is considered lazy. And being lazy cannot be justified. But what happens if you
carry out your plans and fail? Of course, it is no one's fault but your own. But we must not
lament. This is the standard of value of the world we live in. The bursting of Japan's bubble e-
conomy in September 1985; Lehman shock in September 2008. The global financial crisis that
ensued; the new Corona in 2020. And the world economy came to a complete halt. No one
knows what will happen next. However this has been going on since the birth of humanity.
None of us can live in peace. Accordingly in such a major event, no one can avoid the crisis.
However even an election, or simply a change of government in the country, can have an impact
and set back plans. From big to small, the slightest change can have a huge impact on our plans.
In such a major event, Having succeeded in finding the scientific basis for 150% tyre life,
I can't help but wonder why I had to take so many detours to solve the rest of the prob-
lems. But this is the reality of the world. As it should be, the world is full of contradictions.
All my development funding arrangements have thus also failed. So I gave up on develop-
ment? No. No matter what happens, it is not my way of life, nor my principle to give up
halfway though once I have made up my mind. If I gave up, it would mean that I am dead.
As long as I am alive, I will continue to work towards achieving my goals. if I give up, the
150% tyre life product will never, ever appear again. It has been more than 25 years since
U.S.Tire-tech and Dupont pulled out due to wheel rust problems, and the proof is that no one
except me, has appeared. Whatever happens, I never give up. I feel obliged to completion. .
(A) Lock Valve Tool:
Lock Valve Tool is a valve tool that grips the valve core to prevent it from being blown away by
air. Because valve tool is very inconvenient under high pressure like a truck tyre. I checked if there
was a tool to hold the valve core, and found it in the catalogue of a company in the USA. Then I
flew to New York to buy it. Because it was cheaper to buy a tool that already existed as a product
than to develop one. As soon as I returned, immediately tried it out. However I was not satisfied as
far as its function was concerned: As soon as I saw it, the structural problems were obvious. Fur-
ther, the means of holding the valve core was by means of a V-shaped groove, the material was
brass and I could imagine that after a few uses it would cease to function as it began to wear away
. As I imagined, the V-section came to be worn and it could no longer pinch the valve core. What is
worse, there was no certainty in the action of gripping the valve core. It was surprising to me that
such a childish product was sold in the US market. Because it is unthinkable in Japan. Therefore, I
decided to develop a new tool, as the use of such an uncertain tool would damage the product of
Power Pump DC-10. I, therefore, ordered my eldest son, Takanori, to develop the tool. This is
the first job he alone is responsible for doing. I recognise his special talent as a developer.
He comes up with ideas one after another and has never had any trouble with ideas. Of course, he
needs the advice of our technical advisor, Mr.Wakatsuki, when it comes to material selection
and material strength calculations. However, when it comes to ideas for overall development,
our technical advisor cannot hide his surprise at his talent. Development requires imagination to
serve. In order to develop new products that do not exist in the world, we need technology
and ideas that have never existed before. And this ability to think outside the box is some-
thing you are born with, not something that comes from higher education. Our technical ad-
visor has the best education in engineering at the best universities in Japan. But when it comes to
imagination, he is not as good as Takanori. I was very much looking forward to seeing what tools
he would develop. It is an iron shaft with a diameter of 4.6 mm. It has a 2 mm diameter hole for
the valve core. The wall thickness is therefore only 1.8 mm. Under these conditions, how on earth
can the valve core be reliably grasped, extracted and securely mounted inside the valve core?When
I saw the finished prototype, I was amazed: when I tried it with the air valve, the grip was
fantastic, and even when I put the valve core back on, the feeling was the same as with the
valve tool. The difference between this prototype and the tool I bought from the USA was obvi-
ous. The US-made tool is made of brass and holds the valve core between two V-shaped cuts.
After several uses, the V-shaped groove is worn away, the width widens and the valve core can
no longer be held. In contrast, Takanori's method involves making a groove 0.8 mm deep and
0.8 mm wide around the periphery of a 4.6 mm diameter shaft. Holes of 1.2 mm diameter are
drilled from the top at both ends (on the 180°line) and the diameter of the bottom hole is 0.8 mm,
to prevent the ball from falling out. Insert a 1 mm steel ball into the hole and use a spring to hold
the ball from above. The ball at both ends clamps the head of the valve core from both sides
using spring force to hold the valve core firmly in place. The product is perfect. There is
nothing to complain about. The movement of the spring is slight, as it is the movement of two
balls. Because the spring will not weaken if the range of movement is within the set range. We
decided to use it for a while and see if any problems arise. If there were any, it would be due
to the spring itself and the 1 mm wall thickness of the shaft. It is a question of durability. We de-
cided to change the spring from the current C-spring to a wound spring and to consider a design to
increase the strength of the shaft. This is in order to sell it as a product. Because, when I saw
the prototype, I thought that this would surely sell. We named this tool“ Lock Valve Tool:”
After completing the patent application in Japan, I asked our patent attorney to apply for
patents in the USA and Europe.
At first we used it for our own Power Pump according to our policy. But people in tyre shops who
saw it asked us to sell it to them as it was very useful. Hence, planning was accelerated and
market research was initiated and found that it was well received, so we decided to manu-
facture and sell it as soon as possible. With regard to prices, worldwide, valve tool's retail
price almost $1.5~2.0/pc. However the Lock valve tool we have devised price $25/pc, more
than 10 times. Nevertheless, tyre shops all over Japan bought our Lock Valve Tool.
Please see to it: This is the first model. Exclusive contractors have the company's engraving on
the aluminium handle, as can be seen in the picture(Tip Top).
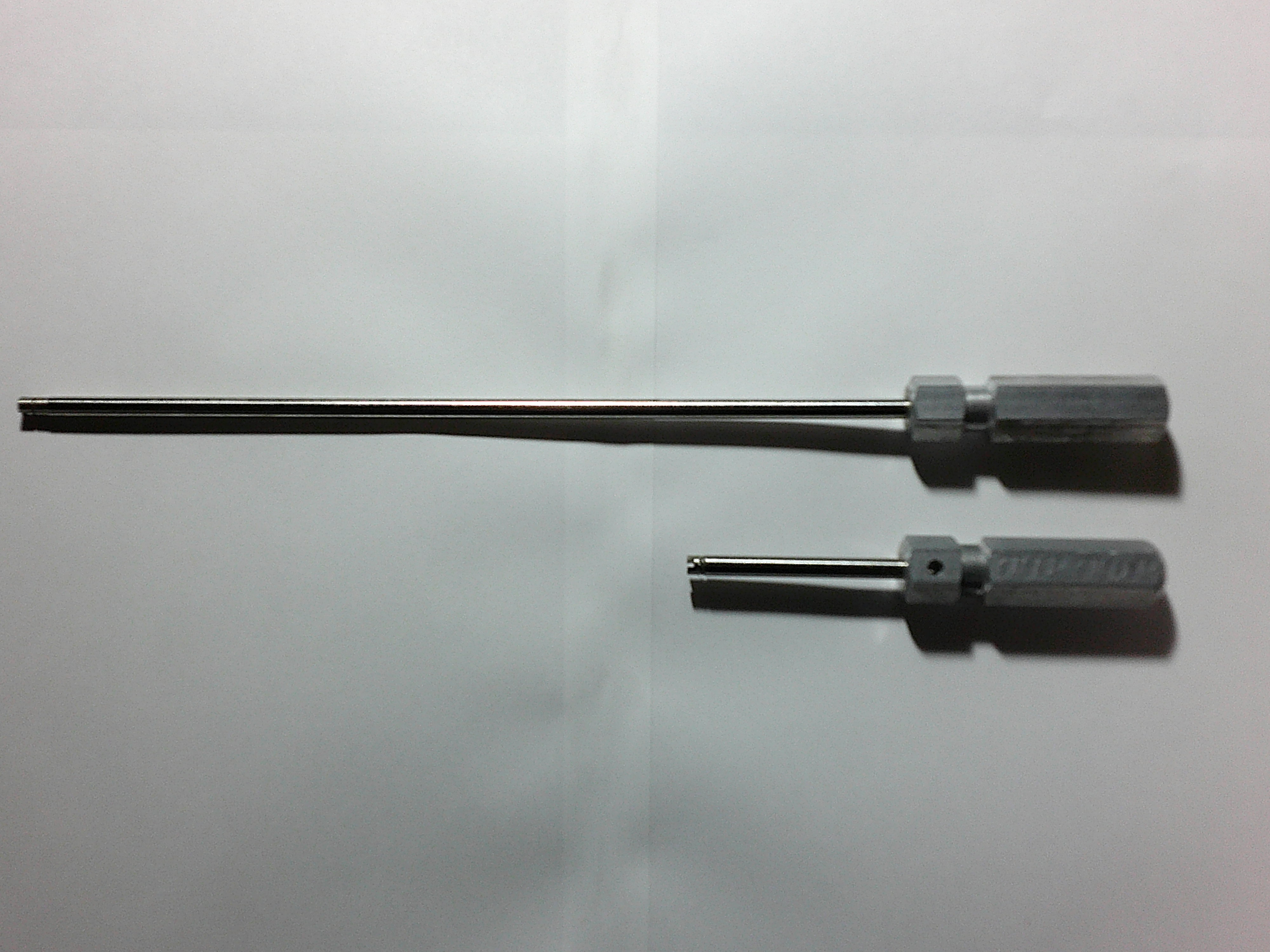
For reference: The lock valve tools are indispensable for the technical training courses for
tyre shops held by the Bridgestone Tyre at their training centre in Tokyo, and when our new
factory was destroyed by fire and we could no longer sell lock valve tools, people of Bridgestone
Tyre training centre came and bought all our stock.
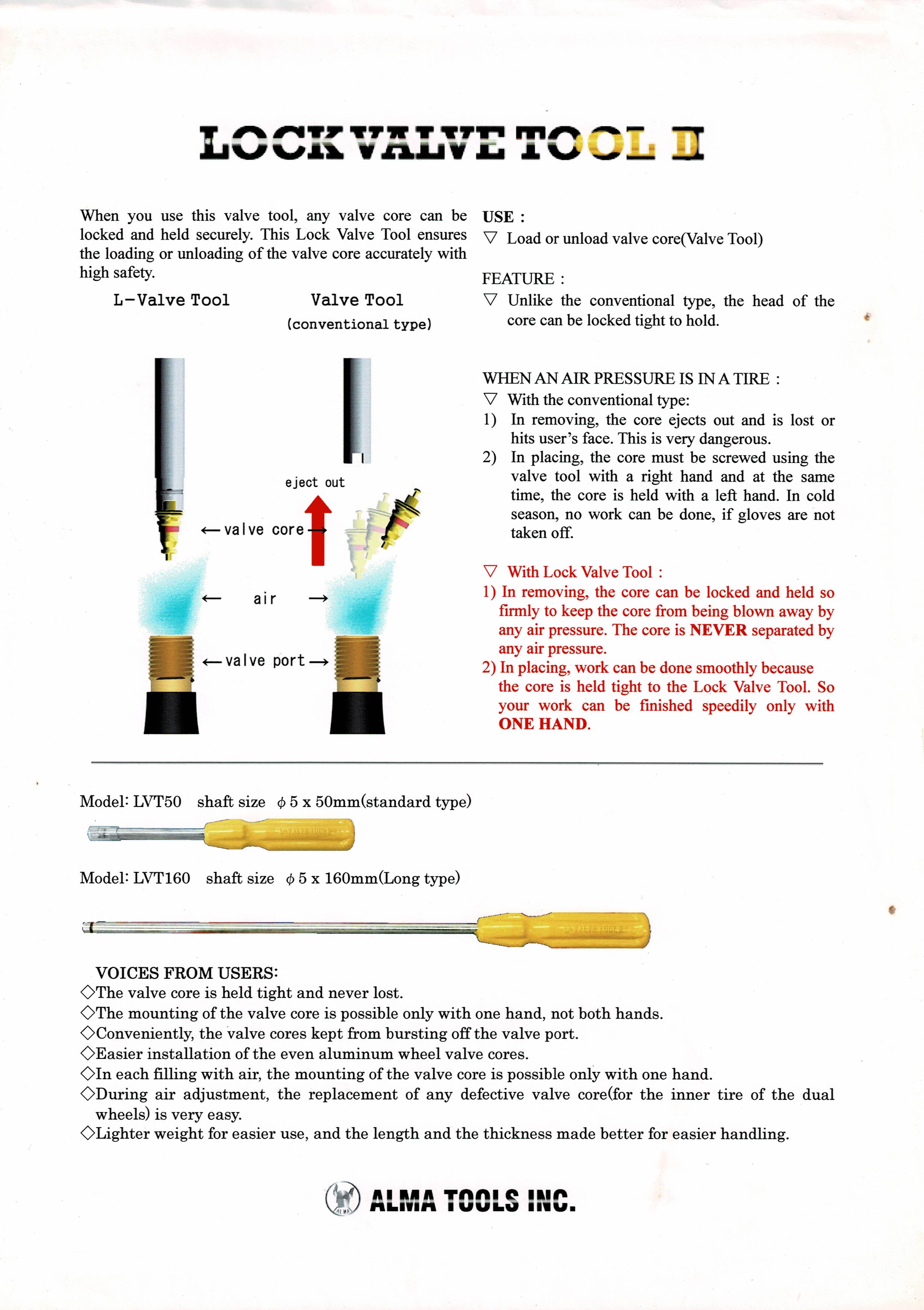
"Lock Valve Tool"
This small product took us and brought us the best profit in a short period of time. It
contributed to sales of more than 200 million yen in one year. (1) Japan market for
USD500,000-, (2) Tip Top for Europe market for USD1,500,000-, (3) Myers for USA,
only samples for USD100,000-. These are only the first orders. However, Myers has a
huge market, the US market. Despite this, I ended up ordering only samples. Sales
would have gone up steadily if there had been no fire at the factory. Considering these
matters, I feel sorry for my eldest son from the bottom of my heart, Takanori, who is a
developer of this wonderful tool.
(B) Development of tools for reinforced concrete housing
complexes, entrance door renewal:
low dust, low vibration and low noise, enabling door frame removal:
1) Takanori, showcasing his talents as chief engineer:
The problem beyond which I was asked by Y.K.K. to teach technology was not an easy one. It was
a technology that did not exist in the world. It concerned the development of a machine to
renew "the entrance doors of reinforced concrete houses". I sought information from the
President on the functional specifications, and size limitations of the tools required to renew the
entrance door, as well as information on the floor plan of the housing complex. This is because the
layout and shape of the leftmost and rightmost entrance doors may differ from the central floor
plan, and the machine must have specifications that allow it to be used in all locations. Without this
information, machines cannot be designed. Basically, it was also requested that the machine should
be heavy enough to be worked by one person. This is because it has a significant impact on con-
struction costs. Takanori, the company's chief engineer, used this information to start de-
signing the design. The thickness of the jaws was determined by calculating the strength of the
machine's jaws. Furthermore, the overall weight is determined. Furthermore, the force of the hy-
draulic pump was also calculated, and the weight of the cylinder was selected to be heavy enough
for one person to work with. It took more than a month, but he prepared several reference draw-
ings and computer graphics of the machine and attached a quotation. I visited the company a-
gain, accompanied by Takanori, with these documents. The reason for having the chief engi-
neer with me was to allow him to explain the technical questions from the designer's point of view.
The president did not make any complaints about our explanations or quotations. The quotations
include, of course, our development costs, which are separate from the product. He seemed con-
vinced about the documents. He then asked how much experience the chief engineer had in
architectural design work. When I replied that we had no experience in architectural mechan-
ical design, he was surprised and refused, saying that he could not offer us the job. I said, 'We
don't take on jobs we can't do. I told him that we had a good technical advisor and that the
chief engineer was designing the machine on his advice, but he still did not believe me. He
was elderly, a bit stubborn, and once he refused, his attitude was unlikely to change. Then I asked
him why he was so concerned about his architectural experience. He told me that the ma-
chine or tool he was asking us to develop was a difficult product that all construction compa-
nies in Japan, including the big ones, could not solve. But, we completed the design draw-
ings in just a month or so. He said he doubted we had completed the drawings with a real un-
derstanding of the work involved. I told him that the lack of experience in the construction in-
dustry does not hinder development in any way. If we add the conditions of use, the prob-
lem will be solved. That is science. The most important thing for development is whether an
idea can come up that achieves the purpose of use under the given conditions. If ideas do
not come up, nothing starts. Imagination is essential for development. Because science is es-
tablished within the scope of set conditions and nothing can be established unconditionally.
However he seems to have the idea that without experience in the construction industry, it is diffi-
cult to develop products that satisfy customers. Then he started talking about the actual use of the
product. When renewing the entrance doors of people living in reinforced concrete housing com-
plexes, the doorframes supporting the heavy entrance doors have to be removed and new door-
frames fitted. However this work is difficult. First, the concrete around the door frame has to be cut
with a cutter in order to avoid destroying the wall except for replacing the door frame. The dust
produced when cutting the concrete with the cutters is massive. Next, the mortar and concrete
holding the doorframe firmly in place must be broken and removed, but it is hard and cannot be
easily removed, and the only method is to use an air-powered slasher. However as we know,
these products are subject to vibration, noise and a lot of dust, so it is not possible to work on
them while people are living in the house, and they usually have to live elsewhere tempo-
rarily for the duration of the work. Therefore, he specifically asked us to develop a product
that would improve the worst of these working conditions and allow people to work in their
own homes. I told him that we had not seen the actual work site and that your description was
very informative. At the same time, I told him that we are sure that the product we are devel-
oping is exactly what you want. However he still did not seem to believe in the Chief Engineer's
design. I ended the discussion by saying that we should show him what our technology looks
like by making a prototype at our own expense. Of course, we do not normally overserve in
this way. We have lost all our money in a fire and have no money at all. But to help us in our
time of need, Mr Koyama went out of his way to ask his drinking buddy, the section chief of
Y.K.K. to give us a job. Therefore, we could not destroy his good name. The aim was also to
show them what kind of technology we have.
2) Successful tools development, then to presentation:
The work effectively began when I promised President Ito that the prototype would be devel-
oped at our expense and that we would use the prototype to make a presentation.
Did I have any concerns about Takanori, who has no experience in building-related develop-
ment at all, developing a prototype for a tool that no one else in the entire Japanese build-
ing industry has succeeded in developing? No, there was none at all. I had worked on con-
struction sites for about two years when I was younger as the voluntary work. I know how hard it
is. Nothing surprises me now. The first thing that has to be passed is the development costs.
It has to be raised quickly. With Heaven's help, we managed to raise funds for development. And
while the prototype was being built, I was struggling to find a reinforced concrete demolition
site. To complete the prototype, we had to repeat the tests until we succeeded. Buildings
are needed for this test. However the majority of buildings in Japan are wooden, and reinforced
concrete buildings were hard to find. We asked around not only in Shizuoka Prefecture, but also in
Tokyo and other neighbouring prefectures seeking information on demolition sites. Once the
prototype was completed, I took my two sons to the demolition site. In this situation, we
kept testing. Fortunately, we came across a demolished prefectural hospital in the adjoining
Yamanashi Prefecture. As a general hospital, it was a large building with many rooms and a
relatively long demolition period, which was very convenient for testing. Here, I mustn't for-
get another person who helped us with this development. It was the section manager of the hy-
draulic cylinder manufacturer Riken Kiki Co. His company is located in Tokyo, but he cooper-
ated with our development and rushed to all the demolition sites with hydraulic pumps. The
prototype is fitted with a hydraulic cylinder, but without the hydraulic pump, the cylinder would
not work. During the first, the prototype claws only slid and did not penetrate the hard con-
crete wall in the slightest. How many times had it been tested? When at last the claws caught
and pierced the concrete, everyone was filled with great joy. Of course, lunch was a cele-
bration and a feast was served. Until then, Takanori had had a hard time changing the shape of
the claw and making a series of design changes. But, the testing did not end there. We are just at
the starting line. The strong mortar and concrete that solidifies the door frames of all reinforced
concrete buildings must be destroyed without fail. And our efforts bore fruit: finally, the day
of the prototype demonstration arrived. I knew that President Ito was not very keen on our
development, as we had no experience in construction. So I had researched companies inter-
ested in developing this product. I found that Nohara Sangyo K.K. a mediumsized company
in Japan, was very interested.
3) Our technology is recognised:
We then invited Mr Nakamura, the section manager, to join us. He was very surprised when
he saw our prototype presentation. He had never seen such a tool before. The tool is free
from noise, vibration and dust, and can finish the job in a very short time. What professional
construction tool designers could not do, an engineer with no experience at all has developed. After
the presentation, when he asked me the name of this tool, I remembered the name of the mon-
strous man and said it was "Samson". Shortly afterwards, mail arrived from him. It looked like a
calendar, but when I unfolded it and looked at it, I was surprised. It was a large poster.
Below, see the photo of the presentation by SAMSON.
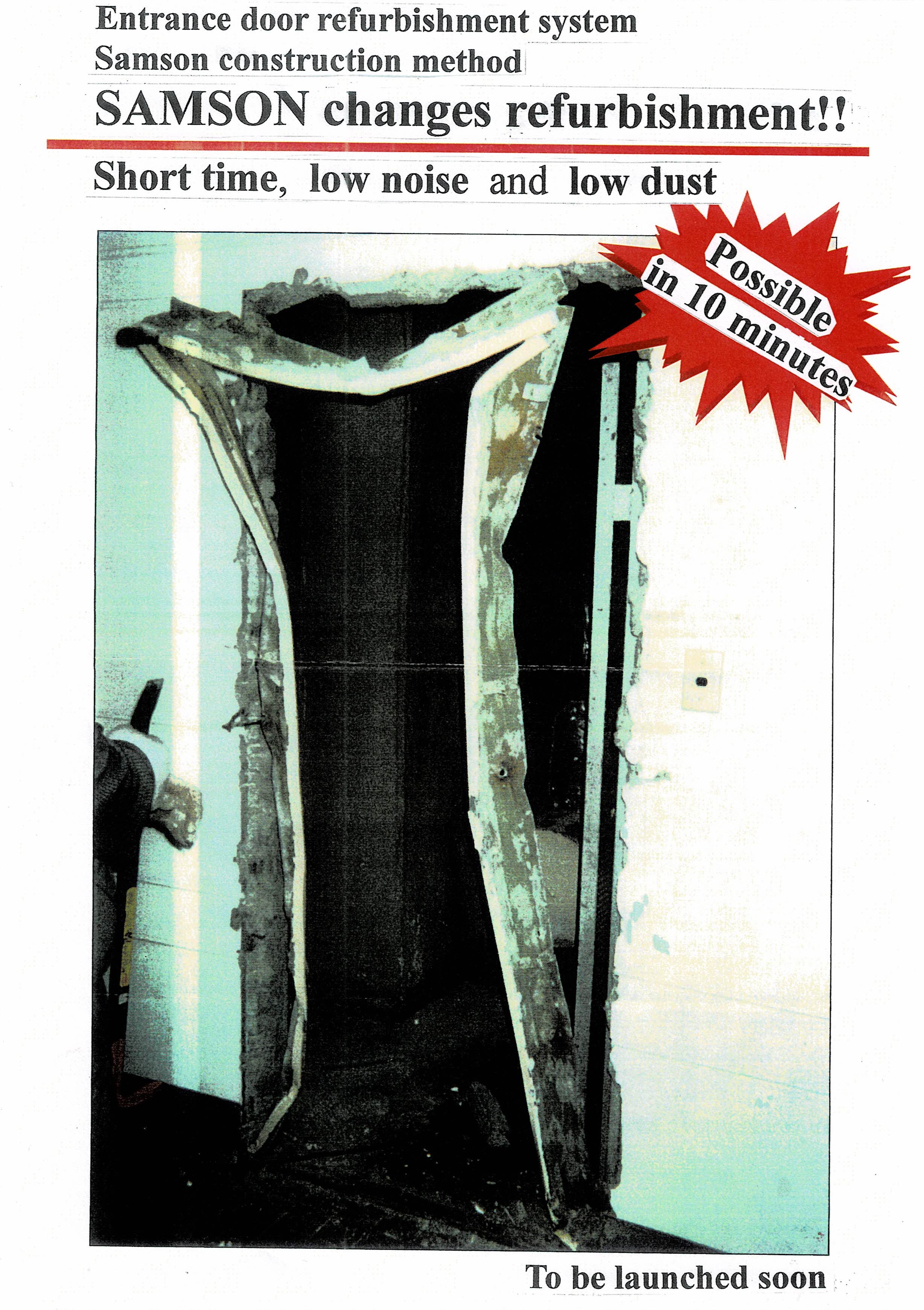
The Samson presentation completely captivated Nakamura, Manager of Nohara Sangyo. And he
was committed to the goal of Nohara Sangyo developing a new Samson construction method
for the renewal of reinforced concrete apartment blocks and entrance doors, using the
Samson tool. we had developed. He was busy working on a new business plan for the Samson
method, a new method of entrance door renewal for reinforced concrete apartment blocks using
our Samson tool. Much later, he came to tell me that the basic business plan had been ap-
proved, but that final approval would depend on a presentation early next January on the
actual removal of the door frames of a reinforced concrete apartment building in Tokyo and
how well that went. He said that many people from the company would come to see the work on
that day. We had to prepare two other tools as well as the Samson. This is because the pre-
sentation removes the doorframe in the same way as it actually does. Can the doorframes
really be removed with little dust and noise, and in a short time-just ten minutes? Almost
everyone could not believe it, it was like a dream, and until they saw it, they could not be-
lieve it. We parted with a promise that we would make sure that the presentation would be a suc-
cess.
4) A presentation of the company's fortunes:
And so, as the new year dawned, we went to the presentation fully prepared. It was a very cold
day. Many people had gathered at the site of the presentation before time to watch the
presentation. The large number of people gathered showed how much interest in this technology
was high. With a large crowd watching, the presentation began. And Takanori played a great role
brilliantly, and the presentation was a success. At a speed that was unthinkable by conventional
wisdom, but without noise or dust, they succeeded in destroying the solid concrete as set and re-
moving the door frame of the reinforced concrete condominium. The people watching the pre-
sentation couldn't help but be amazed. They witnessed a dream-like reality. But that's not
the end of the story. Now it was time for the real thing. As expected, it is a nationwide network
company. Nohara Sangyo is a company that mainly works for state-owned companies. If there is
any trouble, there will be a big problem with the credibility of the work, and the existence of the
company will be questioned. Therefore, in order to thoroughly confirm that our technology is really
problem-free, and to confirm that they are actually capable of carrying out the work according to
the tagline of One Day Finish construction. They secured a large five-story apartment building, and
in fact, they took data on the work time required to remove the entrances and frames of all the
rooms on each floor as designed, and to install new door frames. At first, things didn't go as ex-
pected, and it took a long time, but once we got used to it, everything went well as expected. The
three types of tools we developed also performed all the work without trouble, and their true value
was fully demonstrated. And with this, we have formally signed a contract with Nohara Indus-
try Lmtd. Nohara Sangyo established a new company for the purpose of this project and
promoted Mr. Nakamura, who had worked hard for this project, to its president. Not only
that, but in order to proceed with the project to confirm this decision, the manager of the
Tokyo Metropolitan Housing Authority was pulled out. In addition, we demonstrated using
our tools at the Tokyo Big site, the largest exhibition venue in Japan. My two sons actually
demonstrated there for a week. During this demonstration, many audience members called the
company to inquire about it, and Nohara Sangyo once again informed me that they were surprised
by the response to the tools we developed. Certainly, I don't think there is anyone who would
not be surprised to see a demonstration of cutting concrete pillars without emitting any
dust.
We will introduce the venue we demonstrated, the three types of tools we developed, and the ODF
method (One Day Finish), which uses these to complete a new entrance door in a day while resi-
dents are still staying. A large section of the renovation zone of the Japan Home Show at Tokyo
Big Sight, the largest international exhibition centre in Japan, was reserved for a demon-
stration of the Samson construction method for "Japan Home Show 2002”:
The diagram below shows the venue map.
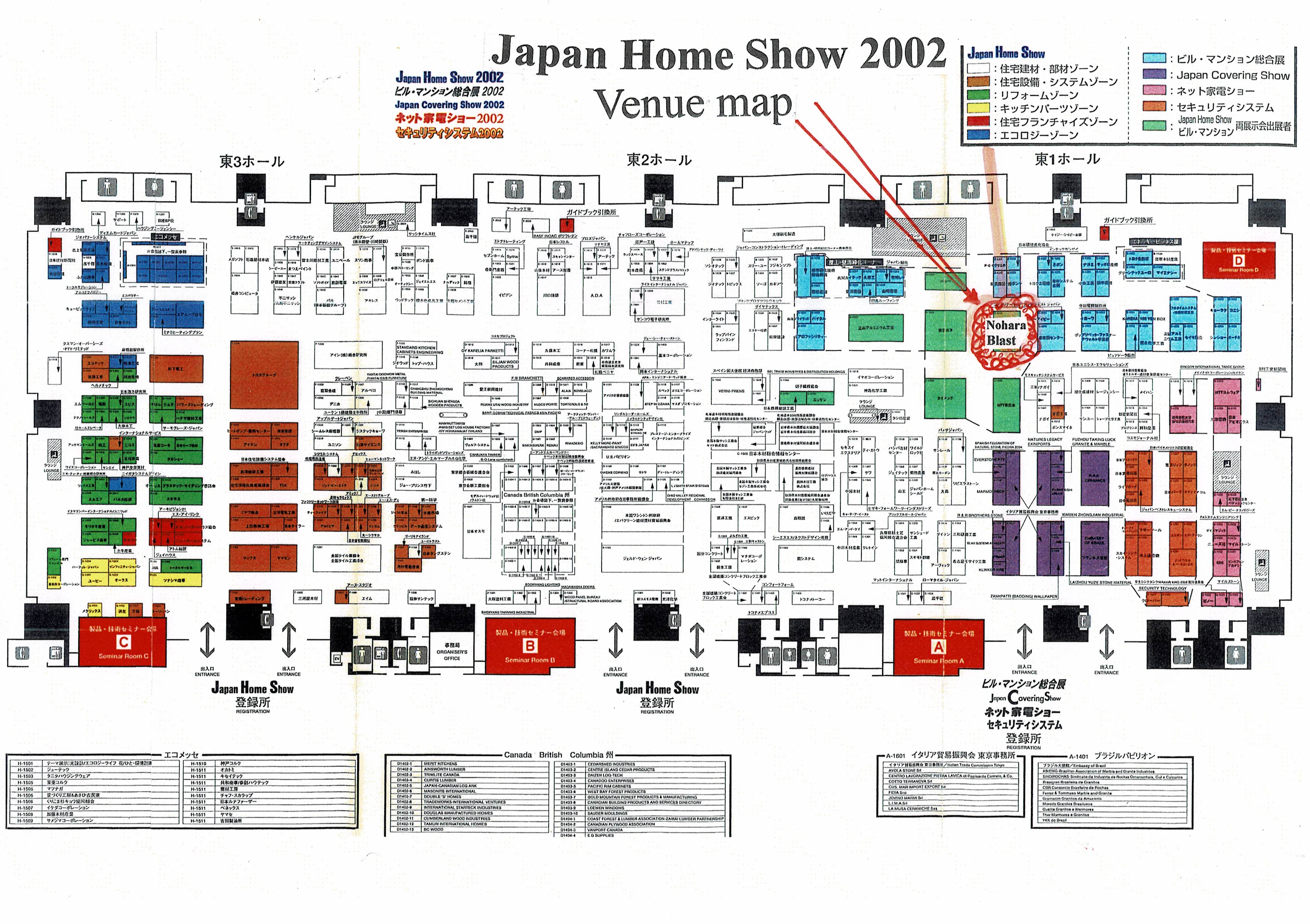
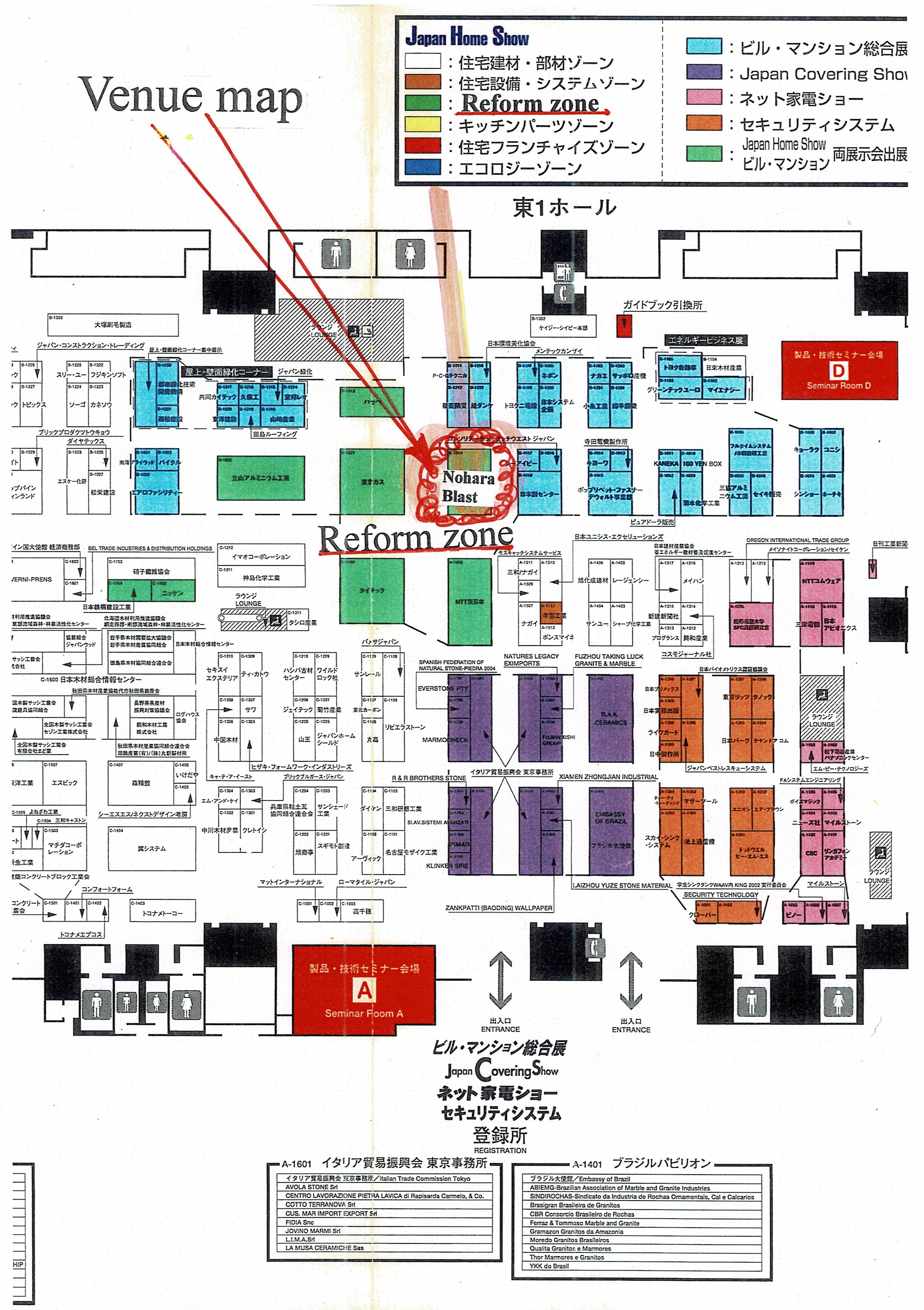
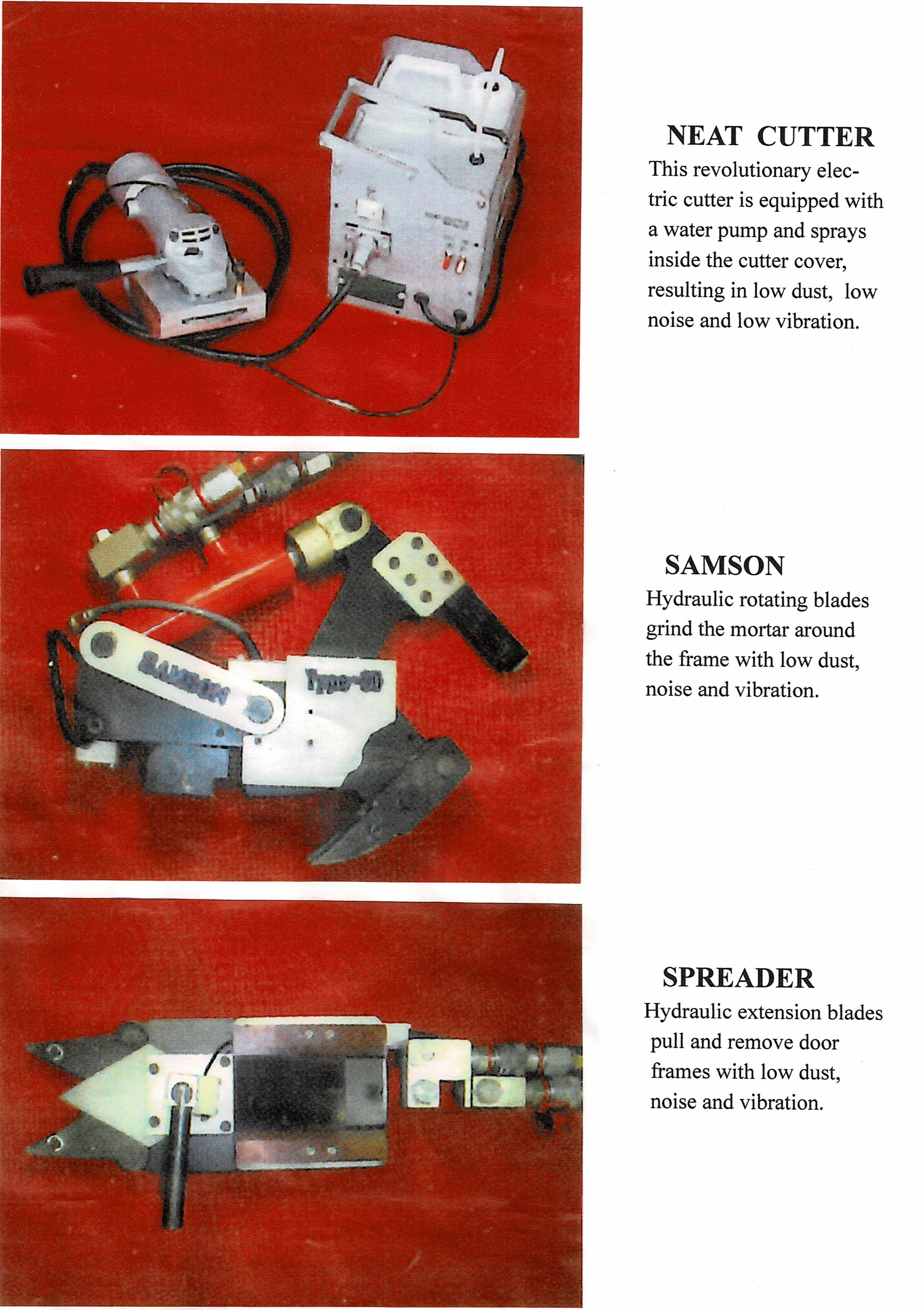
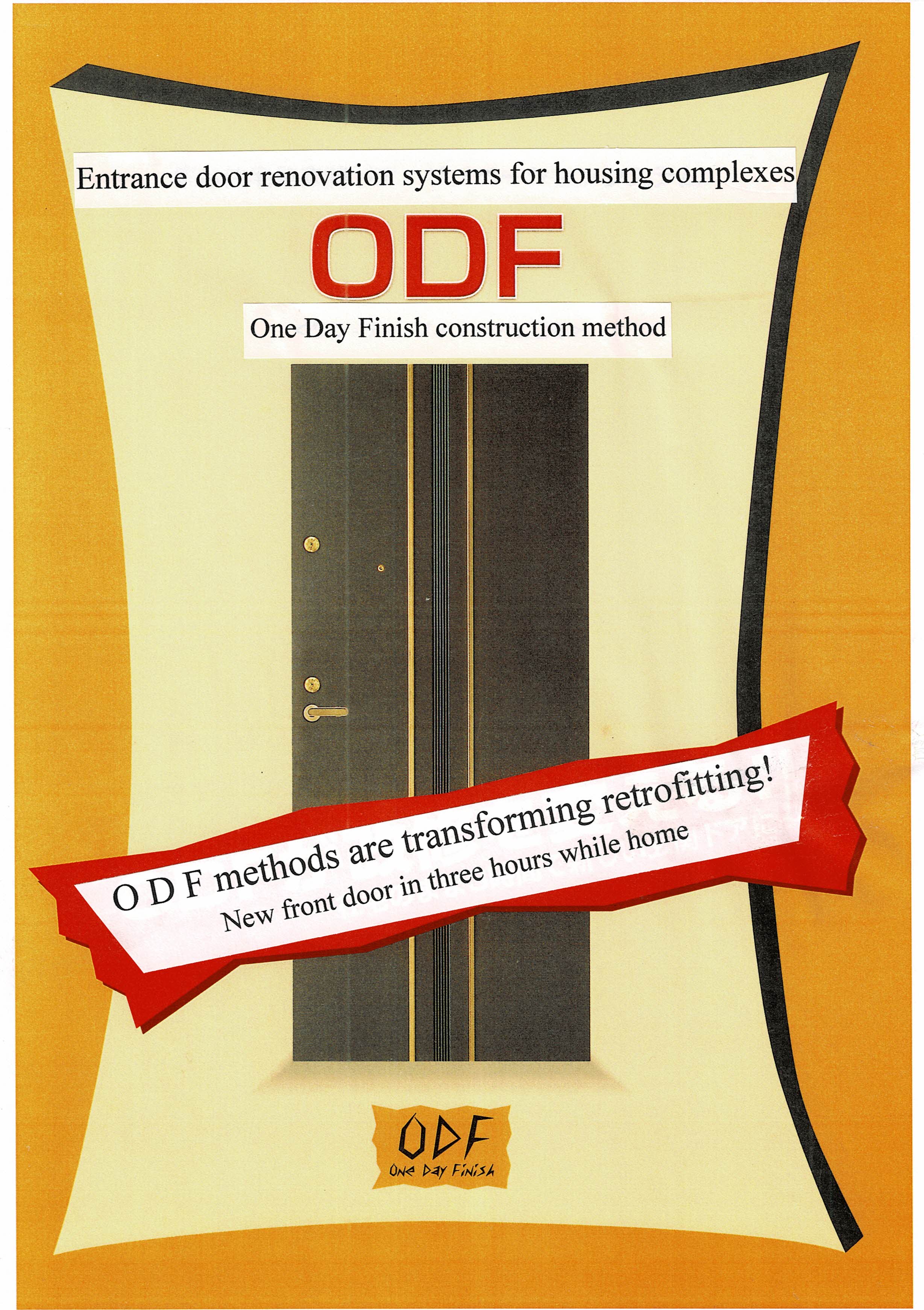
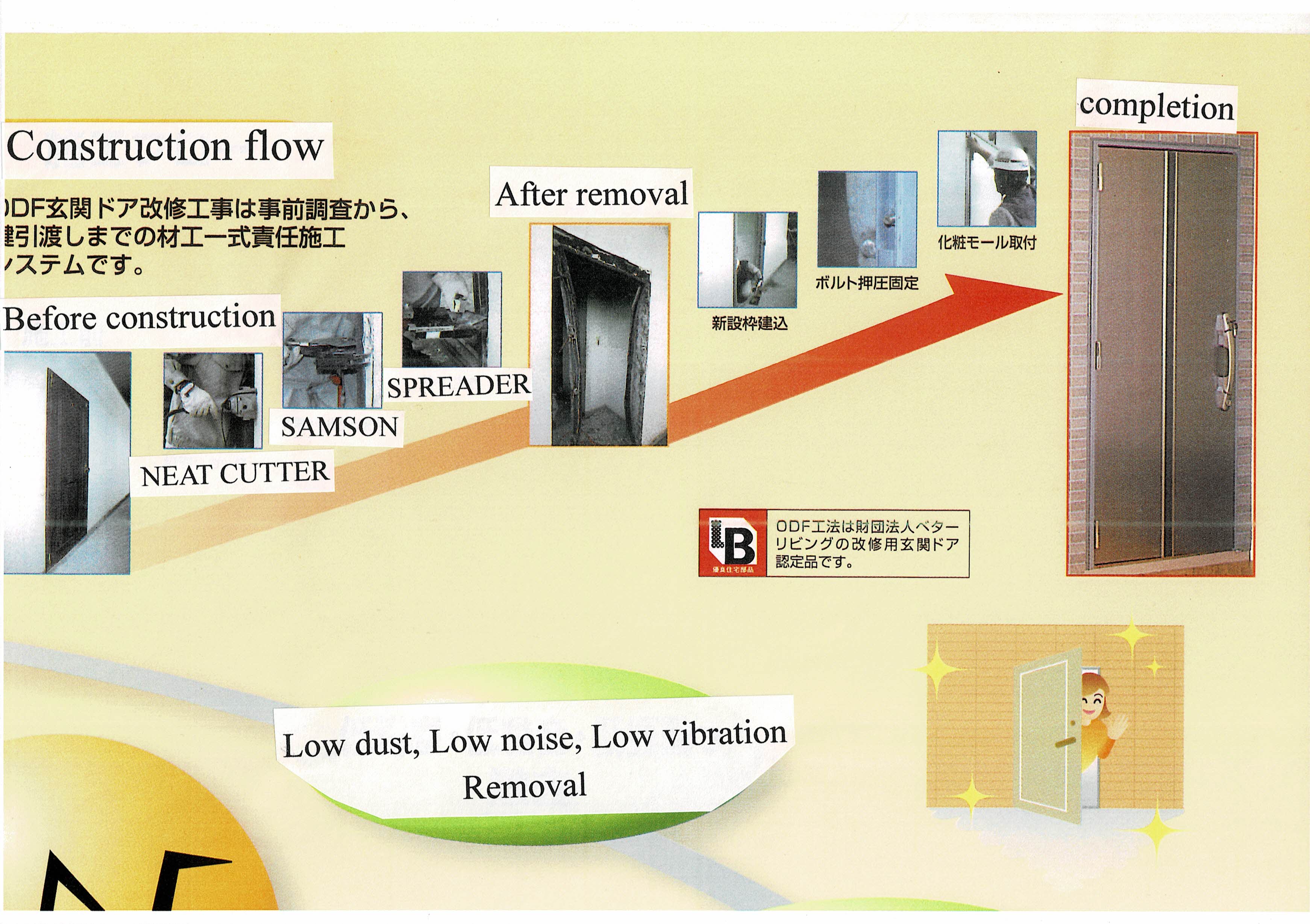
5) Abrupt ending:
In the presence of a large number of stakeholders, the actual work of removing the door
frame of a reinforced concrete condominium was presented in front of them in a short time,
without any noise, dust, or vibration. And the executives of Nohara Sangyo Lmt. invested a
lot of money and human resources to launch this new business. As for Nohara Industry Lmt.,
everything went according to plan, and they were fully prepared. And there was nothing to
worry about. However, the crucial order doesn't come from them. Without the tools we have
developed, they would not be able to do anything, so in order for this business to start, they have
to start by ordering tools from us. Despite this, I don't get any orders from them. Even
though I was optimistic, I was starting to feel a little anxious. Then, Mr. Nakamura contacted me
and reported that this project would be discontinued. He said he would tell me more about the
details later, and hung up. We have spent more than a year developing this tools, and we
spend a lot of money. However, for unknown reasons, this project that promised a future
was suddenly canceled. I tried to think about what I could think of if this business was going to
be ruined, but I had no idea. The market has not disappeared, nor has there been a problem
with the technology to meet the demands of the market. Unless there are problems with these
two points, it is unthinkable to cancel the project.
Eventually, the truth came out. One of the strengths of Nohara Industry Lmt., as a company is its
dealings with state-owned enterprises. Therefore, if our new business is attractive and Nohara In-
dustry Lmt., is able to sign a contract with a state-owned enterprise with which it has a business
partner, our business can be carried out as a state-owned enterprise, and if the budget of the Diet
is passed, the annual budget will be automatically secured. Large-scale reinforced concrete apart-
ments by state-owned enterprises are located all over the country, and their operation can proceed
without any trouble under the direction of the state-owned enterprises. Therefore, as long as
Nohara Industry Lmt., is able to contract with state-owned enterprises, they will apply for subcon-
tractors from all over the country to undertake this work. This is because we have the patents
for the tools that make this method possible. And Nohara Industry Lmt., has a patent for
the ODF method. The ODF method required for this work is instructed by Nohara Industry Lmt.,
to subcontractors, and the tools are purchased from us by Nohara Sangyo and sold to them. This
work is a state-owned enterprise, which has a large presence throughout the country. If
Nohara Industries teaches technology to subcontractors and sells tools to them, the work will move
forward. Nohara Industry Lmt., collects royalties for the ODF method from subcontractors.
It is agreed in a contract between Nohara Industry Lmt. and ALMA TOOLS INC. that it will
be distributed 50% and 50%. Therefore, in the third year, the commission fee that came into us
alone was planned to be more than USD1,000,000-. However, at that time, the privatization of the
Japan National Railways had become a political issue, and Junichiro Koizumi fought and won the
election by targeting it. I used to think that only railways should be privatized, but the new
Prime Minister Koizumi has forced the privatization of all state-owned enterprises. As a re-
sult, all state-owned enterprises, such as the Japan Housing Corporation were privatized.
Then the business plan that Nohara Industry Lmt., had in mind, was fundamentally re-
viewed. The new fiscal year of the Japan government is one year, from April to March of the fol-
lowing year. Due to these circumstances, Nohara Industry Lmt., had no choice but to cancel
this new business. Who is responsible for the cancellation of this project? Of course, Nohara In-
dustry Ltd., does not. We don't have it either. But this is the reality and the ending.
6) Developing a new business plan:
We had no time to be depressed about the sudden demise of a project, we had put everything we
had into the removal tools for the renewal of the entrance doors of a reinforced housing complex.
People are destined to have to earn, in order to live. Men are doomed to work until they die
with sweat on their faces. No matter how hard it is, a man must work for his family. As a fa-
ther, I have a responsibility to set an example to my sons. Talent or no talent, money or no money,
one must work hard to fulfil one's responsibilities. And the important thing is that, no matter what
the circumstances, we must live with dignity as human beings. One must not choose a way
of life that demeans one's character. Because, People reap what they sow. And he does not
reap what he does not sow. Therefore, if we act contrary to this, the consequences are obvious.
Therefore, we must not act on temporary feelings. You do not reap what you do not sow. There-
fore, one must always act according to the best knowledge one has. Indeed, no matter how
hard we work and how best we do our best work, there are times when it does not bear
fruits. No, it may be that such is often the case in this world. That is why we must always keep
sowing good seeds. For no one knows which seed he will reap. If we live contrary to our
best knowledge, we will surely regret. Therefore, after various failures, the destruction of prop-
erty by fire and even more debt, we put everything we had into this project, and despite every-
thing we did we succeeded, and as a result, it was ruined. Therefore, we are in an even worse
economic situation than before. Nevertheless, we must not lower our standards for our
work and for our way of life as a humanbeing. I believe that everything in this world is gov-
erned by eternal, unchanging principles and that everything is in motion. Therefore, as a
small and micro enterprise with no big business capital, why do I apply for patents and
constantly spend time and money on developing new products, like the same as a big com-
pany? Because I am convinced, as already mentioned, that economic matters are run by eco-
nomic laws. Therefore I believe that before the economic laws, there are no small or large
enterprises and everyone is equal. This time, it didn't go well, but why is it possible for
Nohara Industry Lmt., which has a high annual turnover of USD One hundred million- and
many employees, and only three small companies at present, me and my two sons, to distrib-
ute 50% : 50% of the patent fees using this ODF method? Normally, this would be unthinka-
ble. This is because this business would not be possible without our technology. Knowing
this, Nohara Industry has no choice but to accept my request. If one wants to make a profit,
the only way is to follow the economic principles. Therefore, even if I am in the worst financial
situation, there is only one thing to do: Follow the laws of the economy and make things
happen. This is my conviction and I will not live contrary to it. Despite all our efforts, in accord-
ance with economic principles, there was no result as we did this time, but I have no regrets
in my heart. For my mind knows that I have obeyed the law of the economy. What I fear
most is not obeying the laws. It is a complete failure and I will regret it forever. Because
I know that is the power of law. For it is an immutable and the most reliable eternal prin-
ciple.
(C) The next product is a tyre checker:
What will be the next product development? We have been involved with truck tyres through
puncture preventive product. We have found that maintaining the correct inflation is crucial
for tyre life. The development of products that make it possible to easily check the air pressure in
truck tyres was therefore taken up as a topic for discussion. After discussion, it was considered
marketable. We decided to conduct specific market research with the prototype once it had
been completed. From past experience, market research without samples is ineffective. Be-
cause people give specific answers to specific questions and can only give general answers to gen-
eral questions. Therefore if we want to obtain from them what we want, we need a certain
specific sample. In other words, unless we provide them with information to decide, they can not
comment on new products they haven't seen. It is quite natural. Then the first step was to in-
vestigate the actual situation with air pressure tyer checkers. We looked for samples of tyre
checkers, but only found products for passenger cars and none at all for trucks. And most
of the products on the market were made in Taiwan. The chief engineer, Takanori, immediately
recognised their product defects when he saw the samples. All passenger car products are of
the type where the valve core is removed and a checker is fitted in place of the valve cap. The air
pressure can be visually checked by the movement of a spring inside the tyre checker. Here, too,
he demonstrated his talent to the full.
(1) Tyer checker for trucks:
Chief engineer's proposals:
(i) Products for passenger cars are mounted on the air valve, so the product protrudes outside the
tyre, and if the product should come into contact with something, it will be damaged and air
will leak out, which is a safety issue. In the case of truck tyres, there is a risk of serious acci-
dents. This is a matter of Design issues.
(ii) Passenger cars have single tyres, whereas trucks have both single and double tyres and are
completely useless against double tyres. Therefore there is a need for products that can cope
with both single and double tyres. We have started work on the development of the basic key
components of a tyre checker for trucks according to the Chief engineer's development proposal.
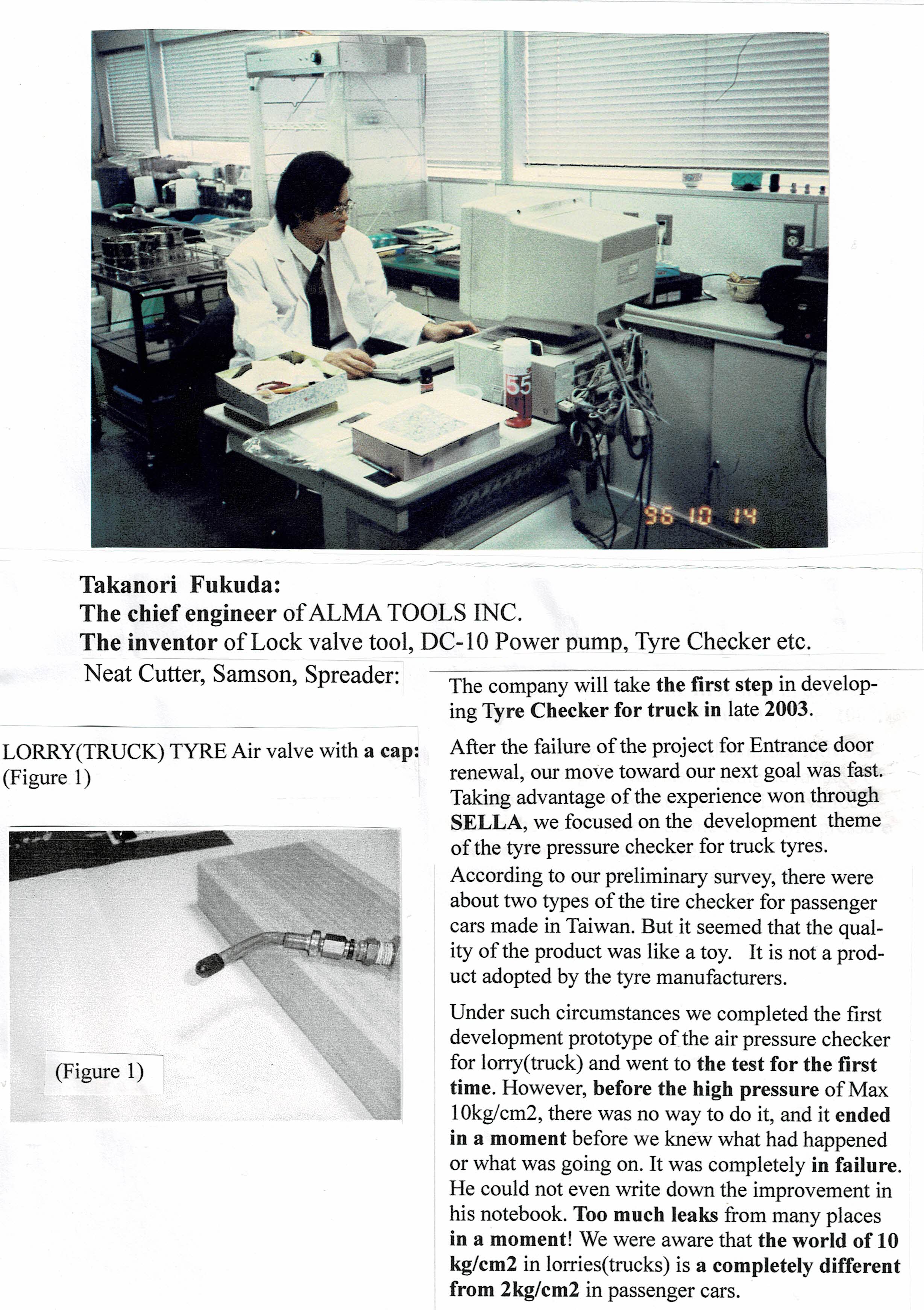

(2) Tyre Checker Model No.1:
We succeeded in developing the world's first Tyre Checker for trucks, but my judgment as a man-
ager was not good. Unlike passenger cars with a tyre pressure of 200 kPa range, trucks must
be made to withstand pressure at 1000 kPa to the maximum.How difficult it is, and how many
times more money is spent on development than a passenger car. Before this, We have spent
already two years and a lot of money on Tools for an apartment building, entrance door re-
newal project. Completely, we have far exceeded the limits of our borrowing amount. The biggest
reason is no sales activity. Of course, I am fully aware of that. On March 16, 2000, I lost all our
property in one day due to a fire in the new factory, and I have been living under economic
pressure. Fortunately, it has not affected the progress of development. And the project to renew
the front door, which I had been hoping for, suddenly disappeared due to the election. In the
midst of heavy debt, I must further confront the development of a new product called tyre check-
er. This product is a product using resin, and it costs tens of millions of yen for molds just for pro-
totyping. If we will succeed in one shot, no problem. but improvements are made, new molds must
be made. And even if the prototype is successful, a separate mold for mass production is required
at the time of mass production. In order to reduce the product cost it is necessary to take as many
molds as possible, and furthermore, the durability of the molds must be increased to maximize the
number of molded products. We will think about it after the development is successful and orders
arrive. Now we have to do our best to develop for commercialization. But how do I finance
it? With no collateral, we have completely exceeded the limits of credit borrowing, and I have en-
dured that pressure all our developments. Don't you have Mr. Suzuki? Yes, I know that he
has never refused when I asked for financial support. Therefore, he's the last person for me. So,
just because I'm in financial trouble, he's not the first person I ask. But this time, I was finally in
dire straits and asked Mr. Suzuki for support. He responded graciously as always. it is natural
to say to the extent that he is possible. His work doesn't always go well. But, how fortunate
I am to have someone close to me who knows me and understands me and helps me suc-
ceed in my work! I am truly grateful.
Our sales policy, as already mentioned, is to complete the prototype based on our best knowl-
edge now, and see the reaction of our future customers, tyre manufacturers. This is because
we are to sell our product through tyre manufacturers. However before going to tyre manu-
facturers' head offices, I decided to visit the distributors of each tyre manufacturer in Shizuo-
ka Prefecture. This is to fully prepare for visits to tyre manufacturers' head offices.
(3) Unexpected events:
I have always put first and foremost to act according to the best knowledge (eternal princi-
ple) in important matters. Because to act is to sow a seed, and one always reaps the seed
that one sows. In other words, we cannot escape this universal law that we must be held ac-
countable for the consequences of our actions. For the eternal principle is the truth, and
there is no further principle. And after obeying it faithfully, there is no choice but to accept
wholeheartedly, whatever the consequences it may be. For as long as I have acted according
to the highest knowledge(truth), there will be no further result. If there are no applicable
principles, I think I should act according to the best ideas I can think of. If there is any suffer-
ing or regret, it is because I have not followed the best knowledge or judgement I know. Therefore
in order to succeed in the business, we were going to make sufficient preparations in ac-
cordance with the future sales policy. When the first prototype was completed, before visit-
ing the headquarters of tyre manufacturers, according to our previous plan, I first visited each tyre
manufacturer's distributor in Shizuoka Prefecture to find out how they evaluated the new prod-
uct. The main purpose is to gather information to advance negotiations with tyre manufactur-
ers in an advantageous manner. Nothing else.
However, Something completely unexpected happened to me: It was a suggestion from the
head of the tyre accessories department of the first company I visited. It is an exclusive
contract offer that is Bridgestone Tire's distributor in Shizuoka Prefecture. He was eagerly try-
ing to persuade me that first of all, even if I go to the head office, there is no contract. Because
there is no track record of this product. And they have a close relationship with the distributor in
Aichi Prefecture, which has a strong influence nationwide on truck tyres. In cooperation with
Aichi's(Nagoya) distributors, he promised me that they will strongly promote the nation-
wide sales of this product. Then, after about a year of achievements, if I go to the head of-
fice, the contract will go smoothly. What perfect conditions! No more requirements! Why
did they make such an offer? Of course, Needless to say, they saw great potential in our tyre
checkers as a commercial product. But why couldn't I accept this offer? The only purpose
with them is their evaluation and comments on our specific world's first truck tyre checker.
We do not want anything more from them than that. A Bridgestone Tire distributor has asked us
for an exclusive sales agreement with Bridgestone Tire HQ. But you might question my atti-
tude as to why I didn't accept it. Because many companies may be honored and proud that
a small company like ours has an exclusive contract with the world's largest corporation, but
for me it is not so much to be overjoyed. Because, from the perspective of economic princi-
ples, if our products are strongly marketable, it is a matter of course, and that is what busi-
ness is all about. It is not the size of the company that matters, but the potential of the product
itself that matters. In other words, it is certain that a good product with marketability will
sell. And there is no doubt that the sales channel through which the product is introduced to
the market is also an important factor. And that's what happened when I started gathering in-
formation to make that decision. Therefore, I believe that there is no fault in acting in accord-
ance with the business policy. But looking back now, I can see that I made the right choice not to
accept his offer. Because his proposal seems to be procedural, and rather a proposal to help us get
a contract with the head office. His suggestion to us is quite timely. Why, then, did I reject it? Cer-
tainly, there seems to be no reason to refuse. If I had accepted their proposal, I think we would
have been too busy to visit Bridgestone/Firestone's headquarters in the United States. And
I would never have met Mr. Guy J. Walenga, nor would I have been taught how to inflate a
tyre directly by a tyre checker. The most important information for a truck tyre checker with
a large number of tyres is to put air into the tyre from the tyre checker without removing the
tyre checker. I learned from him not only the information, but also the specific methods of
doing it. It doesn't get any better than this.
However, in order to complete the tyre checker for trucks, there is one more thing that needs to
be done to solve the problem. It is a ±1% problem, the demand issued by Dunlop tyres, the
measurement accuracy. Certainly, it is a problem that we were not aware of. Of course, Dunlop
himself was unaware. They had accepted our specification of±2.5% product accuracy, but suddenly
at the ordering stage, they asked for ±1%. We solve their demands and problems so easily that
they seem to misunderstand the essence of things. if you buy a product with an accuracy of±1%,
they will understand the reality. It is completely different from the USD6.00/piece that we are
presenting to them. Maybe a few thousand dollars. It is a complete measuring instrument and re-
quires fine adjustments. Mass production is not possible. Dunlop tyre's requirements are out of the
ordinary, and their engineers have made it clear to us why. Even if the company demands an
accuracy of ±1%, there is no way to confirm it. In other words, it is not possible to confirm
it. That doesn't make for a contract. However, I subsequently developed a method for manufac-
turing tyre checkers with a product accuracy of ±1%. In order to achieve this, it is necessary to
have a technology that can measure the movement of a cylinder down to one thousandth of a
millimeter, and with the cooperation of ASAHI KASEI MICRODEVICES CORP., I have finally
developed a technology that makes it possible. The problem, however, is that there is no pros-
pect of a technology that retains the air in the cylinder during the measurement. There is a prob-
lem with the steel ball, and it has to be developed separately. Because when Takanori, the chief en-
gineer, explained to me about the specifications of the tyre checker, the only thing that bothered
me was how to stop the air in the very small cylinder. Keeping the air pressure in the cyli-
nder accurate while measuring. I cannot think of any other method other than using a steel ball
with a diameter of 1mm. But we are convinced that with time, we will find a way. Why do I
say that? The chief engineer of the development, Takanori once told me. The more he thinks,
the more ideas come to him. Therefore, as long as people do not give up thinking, they will
always find a way to solve the problem.
In reality, things that seemed impossible in this world are being solved one after another, new
products are emerging, and the world continues to evolve. Therefore as a developer, we do
not believe that this problem is unsolvable. But, of course, time is needed.
Apart from this incident, there was nothing that surprised me too much about market research in
Japan. In other words, there were no strong expectations or requests for the tyre checkered
truck version. However, I had the idea that truck tyre manufacturers should have a desire to pro-
vide convenience to their customers by eliminating their troubles and hassles as much as possible.
If they had such an idea, they should be able to demand a little more for our products. However,
with the exception of the prefectural agency, I did not have the opportunity to meet anyone with
such foresight. Therefore, I decided to visit a tyre manufacturer in the United States. And I
visited the main tyre manufacturers, and the last one, Bridgestone/Firestone Tire, LLC, had excel-
lent results, so I will only introduce them.
(5) Visit to the headquarters of Bridgestone/Firestone Tires,
USA:
My last visit US Tyre manufacturers was officially named Bridgestone/Firestone North Ameri-
can Tire, LLC. I asked for an appointment with Guy J. Walenga, Engineering Manager. How-
ever he was on a business trip, and it was difficult to get in touch with him through his secretary.
However by the time I left the Japan, I didn't go as far as confirming the appointment. I arrived
at Nashville Air port in Tennessee in the evening. From a pay phone at the airport, I immedi-
ately called Mr. Walenga. The time is 4 pm. Finally I was able to talk to him. But what he told me
was, "Have you seen the e-mail from me? I won't be able to see you on Monday to talk to
you. Because on Monday, we have an important meeting with the government from the
morning, and I can't have any time with you". I understood why he couldn't spend time with
me. But I couldn't say, yes, I understood. I have done everything for this purpose. It's not a-
bout enjoying airplane travel. Of course, he has no obligation to listen to me. Nor is it a matter
for him as a company to have to cancel an important meeting with the government and have
discussions with me. No one thinks there is possibility to talk to me. But still, I refused to admit
it. I came all the way Japan here to meet him. I couldn't accept it easily. But, if I can come up with
any good idea that can solve this problem, there is none. He asked, "Is there any other company
that you visit?" I replied that this was my last company and that I had nowhere else to visit. After
thinking for a while, he presented me with this suggestion. This was a wonderful proposal full of
his good intentions and taking into account my position. He said "The meeting with the govern-
ment starts at 9 a.m., so let's set aside an hour before that, so how about an hour between
8 and 9?" I sincerely appreciated this suggestion. But still, I did not agree with this proposal. And
this is how I replied." I sincerely appreciate your suggestion, but I still disagree with it. Be-
cause we need more than three hours. An hour is meaningless. I would like to ask for your
cooperation somehow" I had to ask him. I'm sure he was surprised to hear my reply. Given the
position he was in, he showed the utmost consideration for me that he could. What more are
you telling me to do? It is a natural emotion to want to say. It was the first time for me to ask
him to do something like this in such a situation, knowing his position, and though having applied
for an appointment but had not been able to reach a formal agreement. However, his position
turned out to be more difficult than I had imagined. He needs to prepare a lot of materials to
use in discussions with the government, but it is December, it is Christmas break, there is
no one to help with it, he has to do it all by himself, and he needs time to prepare. For him
he is in a situation that is not a case of being involved in other people's affairs. But knowing
the situation, I disagree with his proposal and make further demands. If I were in his position,
how would I be able to deal with this situation? But a miracle happened. He didn't reject my
request, but after thinking for a while, then he checked my Saturday and Sunday schedule. And I
told him that there was nothing. Then he said he would call me either on Saturday or Sunday
at noon. Finally, he promised to visit me in my hotel room. I thanked him from the bottom
of my heart. I was waiting for a call on Saturday, but it didn't come on Saturday. Then, at exactly
12 o'clock on Sunday, the phone in my room rang, and I got a call from him. He announced that
he would be visiting at 5 p.m. today. And he visited my room at 5 pm. I sincerely thanked
him for his cooperation. I immediately got into the talk of work. I want to end the meeting
for him as soon as possible. First, due to the Ford Motor Corp. burst accident that occurred
in 2000, US law required passenger cars produced in the United States to have a pneumatic
safety device, but the price is very expensive, but the performance is only a system that a-
lerts when the air pressure drops by 30%. This is because the product is regulated in such a
way that it must use electronic components. This is for the purpose of fostering the U.S. elec-
tronics industry. However we are focusing on truck tyres, not passenger car tyres. This is be-
cause the tyre pressure of passenger cars is 200 kPa range, while the air pressure of truck
tyres is required to be 1000 kPa to the max, which is far from the technology of eletronics.
And marketability is much higher for truck tyres than for passenger car tyres. That is why it is
necessary because the pressure management of truck tyres greatly affects tyre life. We be-
lieve that this will be a great force in truck tyre sales promotion, too. To my thoughts, Mr.
Walenga nodded. So I showed him a truck tyre checker that we had developed, only one in
the world. There is a tyre checker for passenger cars, but not for trucks. The biggest reason for
First problem: The air pressure must withstand up to 1000 kPa at the maximum. It has
five times higher pressure of a passenger car. Due to the strength of the material, its design is
difficult.
Second problem: For safety reasons. Looking at the tyre checker for passenger cars, in order
to see the tyre pressure, the valve core of the air valve is removed, the air of the tyre is directly
connected to the tyre checker and the spring inside the tyre checker is pressed to display the air
pressure. This poses a major safety risk. If a tyre checker coming out of the tyre comes into con-
tact with a road curb or something else, the tyre checker will surely be destroyed or damaged.
However due to the structural problem of the tyre checker, there is no valve core, so the high
pressure air of the tyre escapes instantly. The risk of leading to a major accident is unavoidable.
The third problem: Truck tyres have double wheels. In single tyres, the air pressure value can
be displayed on the side of the tyre checker attached to the air valve by expanding and contracting
the spring. However in the case of double wheels, the air pressure value must be displayed
from two directions, the side and the front. How can we solve these problems? It's not easy.
Furthermore, in the case of double wheels, the space between the tyres is narrow, and it can
not be installed unless the size of the tyre checker is compacted. It is extremely difficult to meet
these conditions. I showed him the actual product and pamphlet and explained how we
solved these problems and developed the product. The method of installing the tyre checker is
to remove the valve cap attached to the air valve and attach the tyre checker to the air valve in-
stead of the valve cap. This completes the task.
He understood my explanation. However based on what he saw of this sample, he comment-
ed that it would be difficult to sell it. For many truck drivers are elderly, and tyre checkers
get dirty with mud. Therefore, at this size, the display is difficult to see. He advised me that
it might be better to increase the size of the tyre checkers a little more. So I further asked
for his opinion on the marketability of this product in the United States. Then he asked me
"What happens if the tyre checker shows red?" I replied "Remove the tyre checker from the
air valve, inflate the tyres, attach the tyre checkers to the air valve again, and you're done"
And he declared,"That won't sell in the U.S.. Because trucks have a lot of tyres. Every time
the air is replenished, the tyre checker is removed from the air valve, and after the air is
replenished, it is too much work to attach the tyre checker to the air valve. If you want to
sell this product in the US market, you have to be able to inflate it through the tyre checker
without removing it" I felt like the scales had been removed from my eyes. We didn't notice
at all until he told us. But he's right. But my mind was full of problems, and I couldn't thank him
for his opinion. The problem is, he simply says that you can simply put air in from the tyre
checker without removing it from the air valve, but how can we put air directly from the
tyre checker? I have no idea how to do that. This is because the size of the Tyre checker was
designed in comma millimeters, and there was no space to let air into the tyre's air valve. But
he already understood my problem. And told me."You don't have to worry about how to get air
directly from the tyre checker into the air valve. But, you need a sample. If you give it to
your engineer, he will look at the sample and see how to design it to make it possible. I will
also teach you how to get that sample, so you don't have to worry about it. "I felt joy bubble up
from the bottom of my heart. Because the advice Mr. Walanga gave me on the US market is
the best specifications I know.
To be given the idea of being able to directly inflate the tyre air valve from the tyre checker
without having to remove the tyre checker one by one with a sample, shows how lucky I am.
I visited US tyre manufacturers and asked for the tyre checker rating, and in the end, I got
the best I could ask for. I am truly deeply grateful for this opportunity. Finally, Mr. Walenga
told me that when a prototype is complete, please send it to us at any time. Cooperate free
of charge, such as quality inspection. He said that they are always ready to cooperate
greatly with this product. Then he left the room. The clock read 20:30. The meeting lasted ex-
actly three and a half hours. Will I ever see someone like him again? With such a big job, he
never refused my appointment until the end, something that he would normally refuse outright,
to someone he met for the first time in a small company who didn't even know what I was here
for. He was a man of high calibre. Not only that, but he was also an excellent engineer.
Guy J. Walenga, I will never forget your name. I am now reminded to pursue the possibility of
tyre checkers that make use of your ideas.
(6)The first production model:
In a meeting with Mr. Walenga of Bridgestone/ Firestone Tires in the United States, the specifica-
tions of my final model were solidified. However it is not possible to immediately proceed with
the work towards it. It is understandable that it is an excellent technology, but basic experi-
ments are necessary to incorporate it into our tyre checkers. In addition, it is impossible to
judge at this point in time how much it is possible to achieve the smallest shape while maintaining
compressive strength, unless we actually make a prototype and test it. Naturally, we can't tell this
with a single test, and we cannot make a decision without several tests. And it takes time.
Therefore, the probability of meeting and discussing with Mr. Walenga is close to zero.
For this reason, we have to prepare a tyre checker for trucks with new specifications that take into
account the immediate situation. Therefore, I propose Japan tyre manufacturers to present a
model that was slightly larger than the current model, and made the display easier to see in-
cluding a request from the United States. However everyone was against my proposal. This is
because, in a small Japan of the country, three-quarters of the truck tyre market is occupied
by two-and four-ton truck tyres, and only a quarter of large tyres. The situation is completely
different from that of the United States, which is a large country. As we work as a business, we
have to make a profit. Otherwise, companies will go bankrupt. Compact products are produced in
small quantities for the Japan market. For the U.S. market, if we were to make a product with a
larger size, it would not be profitable just because of the mold costs. We have run into prob-
lems again. However it is here that the true nature of Takanori, the chief engineer, is also
demonstrated. The current model is compact and can be installed on both two- and four-ton
vehicles. However, since the product is compact, if the product is soiled with mud or the like,
the display becomes difficult to see. So he thought. Even if it is compact, how can we make
the display easier to see? This led to the development of the world's first product. It is the
use of high-intensity light-emitting diodes. At that time, it was not possible to produce blue
light-emitting diodes, but Japan finally succeeded ahead of the rest of the world. If we use
two colors, red and blue, the display will be clear. Takanori made a suggestion that no one
could think of. The manager of Toyo Tire particularly appreciated this proposal. "Tyre pres-
sure checks must be done before driving". The reason is that heat is generated after driving,
and accurate air pressure cannot be measured. Drivers leave early morning or at night. But he
says he has never seen a driver checking tyre pressure in the dark with a flashlight. There-
fore, it was evaluated that the display by high-brightness diode light emission can facilitate
air pressure check in the dark and greatly contributes to tyre sales promotion.
The chief engineer, Takanori, saved this crisis with an excellent idea. It is an idea to make the
size small and the display sharp. So how does he bring that idea to life? It was the use of
high-brightness diodes, which were not yet known to the world at that time. Domestic tyre
manufacturers were very pleased when they heard about it. This is because it can greatly
contribute to the promotion of truck tyres. Thus the specification of the production model be-
fore the final model was determined. Takanori put all his efforts into the development of this PRO-
TOTYPE.
(7) Tyre Checker launches sales activities for trucks:
As soon as the Ultra-High Brightness Diode Prototype was completed, we started sales activ-
ities. We listened to the tyre manufacturer's request in advance, and on top of that, the shape is
as compact as the first model, and it is a product that uses a high-brightness light-emitting
diode. Therefore, I had the idea of having all interested tyre manufacturers purchase it as a
promotional product for tyres. I had a preconceived notion that the companies we were selling
our products to were Tyre manufacturers, and that since they were respectable companies, they
were basically gentlemen and would approach our business in a fair manner. Therefore, it
cannot be denied that there was a problem with my attitude toward negotiations. I trusted
them too much. And it hurts. Due to the nature of the work, I thought that there would be no
exclusive sales this time, so I thought that I should visit all the manufacturers who were inter-
ested in our products. Therefore, I made an appointment and visited in the order of the course
I visited. And the first visit was Dunlop tires. Therefore, I should have gone to Toyo Tire first,
who evaluated our product. However, I ended up starting with Dunlop tyres as a routine of
visiting just the major tire manufacturers, which are convenient for transportation. Of course, it is
a product that is incomparably better than passenger cars, has high marketability, and we know
that it will sell. Therefore, there is no difficulty in making an appointment for a visit.
We gave a prototype demonstration to Dunlop Tire technicians. Mr. Masuda of Dunlop Tire's
Technical Service Department answered our questions in writing after our demonstration.
1) Evaluation of our product through demonstration:
We believe that it is a very good product as you said. In particular, the benefits to TB (trucks
and buses) users are great, and I felt that even for the tyre manufacturers, it could reduce dam-
age caused by low internal pressure driving if the customers could check it.
2) In particular, points that seem to be good:
1. The point that the air pressure can be checked even in the dark.
2. Even if the checker breaks down while it is installed, air leakage does not occur (consideration
for safety).
3. Miniaturization as much as possible.
3) Problems:
(i) Unidentified
(ii) Achieve the intended performance (maintaining the set value that switches between blue and
red) and durability.
→ We will confirm it in a future monitor.
Dunlop Tire Technical Service Department
Kengo Masuda
(8) Exclusive agreement with Dunlop Tire for 2 years only:
Many tyre manufacturers in Japan had high expectations for this model, we did not intend to make
an exclusive contract for Dunlop tire alone, but their enthusiasm led us to agree to a contract with
a limited contract of two years. Of course, in two years' time, we intend to supply this product to
all tyre manufacturers who wish to sell it. There are other important reasons why we signed an ex-
clusive contract with Dunlop Tire as a manufacturer of tyre checkers. That is, unless it is an ex-
clusive contract, the conditions of the minimum quantity cannot be presented. Once the
minimum quantity is determined, the budget for production capacity and production facilities can
be systematically determined and advanced. Otherwise planned production becomes difficult. First
of all, Dunlop's most important point in terms of quality is to make the product problem-
free. For this reason, they decided to install tyre checkers on all cars of sales offices nation-
wide from Hokkaido in the north of the Japan to Okinawa in the south, and have them re-
port problems, improvements, opinions, etc. to the head office every month and periodi-
cally for a year. We accepted their proposal. Then, we were prepared the samples for all cars of
Sales offices nationwide. Every month, we regularly visited Dunlop Tire's Tokyo headquarters
accompanied by Takanori, our chief engineer, to discuss the problems and improvements in
the reports that come up every month. And gradually the specifications of the tyre checker
were solidified. Dunlop tire required us the strict conditions for the sake of safety as a tyre manu-
facturer. Therefore, the technical manager in charge of us has demanded the same standards of
quality for our products as theirs. We, as a manufacturer of tyre checkers, have to respond to the
various problems and requests raised by all the sales offices, all to their satisfaction. In the
midst of all this, Dunlop Tire was surprised by our response. According to the technical manag-
er, they are tyre manufacturers and do business with about 120 companies, large and small.
If there is a problem, it will take about a month to receive a response from them, regard-
less of whether it is a large company or a small company. We have responded in 10 days
from one week. The speed of our response has surprised some within the Dunlop company.
This is all thanks to the outstanding talent of Takanori, our the chief engineer.
(9) The last big wall:
Due to the various problems raised and requested by each sales office, and due to the basic re-
quests of Dunlop tire manufacturers, the specifications of our products have changed signifi-
cantly. And with that new spec, we set to work on a tyre checker prototype for trucks.
However, after the prototype was completed, Dunlop Tire suddenly requested product accu-
racy. Their request was to increase the accuracy of the product from ±5% to ±2.5%.
Dunlop tires' requirements are that ±5% will be 10%, and 10% will be 100kpa for 1000kpa
pressure, which will be inaccurate and unreliable in the product. However, their opinions
differ from the facts. The air pressure of the tyre checker is only the -part, and the + part is
irrelevant. When adding air, the + part is required, but the tyre checker does not measure the
pressure of the + part. It is carried out in tyre shops and in the management of drivers. Tyre
checkers don't intervene there. Therefore, -5% of the accuracy of the tire checker is covered,
and +5% is not. We sorted out the various requirements for Dunlop tyres, asked for final
confirmation, and the two companies agreed on the final specifications. And based on that
agreement, we completed the prototype. After completion of the prototype, suddenly, the
question of product accuracy was raised. However, it was not a formal meeting, but an informal
one. I am the one who hates this kind of disorder the most. I was angry at this irresponsi-
ble and unordered approach of Dunlop Tire.. This is not what a gentleman does. I felt like I saw
Dunlop Tire, the essence of the company.
(10) Takanori his last job:
Apart from my anger at Dunlop, Takanori moved to resolve the issue peacefully. And Takanori, our
chief engineer, had already thought about how to solve this serious problem. Having talent
is another problem. His talent is at a level unthinkable for an ordinary person like me.
He devised a revolutionary method to improve product accuracy and keep costs down. The
equipment was designed so that it could be adjusted without taking much time for adjust-
ment, and the plastic parts could be welded at the same time. Using computers, he perfect-
ed complete programming. And There is another major reason why he developed such a large-
scale device. It is marriage. He has been helping me with my work since he was 24 years old.
But time flew by and he was 35 years old. However, since the new factory was destroyed by
fire, although we have spent many years devoting ourselves to the development of new products
and succeeding in their development. And he supported me with all his might. He has succeed-
ed in developing all the new products so far. However due to various circumstances the
business did not go well. We were not at fault. However, in the end, it did not go well. the
development costs spent on them will remain as debt. As a result, unpaid salaries to him were
accumulating. Apart from this circumstances, if you have talent like him, you can find a job in any
company. In particular, the talent for development has been proven. Anyone who shows what he
has developed so far will want his ability. This is because a company can only entrust development
with training and experience over many years after graduating from school. We are all products
for the first time in the world. All of them are patented products. Therefore, nothing prevents
him from getting a job. But, Takanori wants to succeed in this work for her waiting for him
for a long time. I made a promise to Takanori that I would not hold him back any longer. There-
fore, as soon as the machine was assembled, Takanori was allowed to go to her.
This is the Tyre checker Model-3: which will be the last chal-
lenge of the chief engineer, Takanori.
This is the adjustment part. FYI: this is what he bought all the parts
and assembled everything by himself. Even when money is scarce, he has always
used his wisdom to solve the problem in order to overcome it.
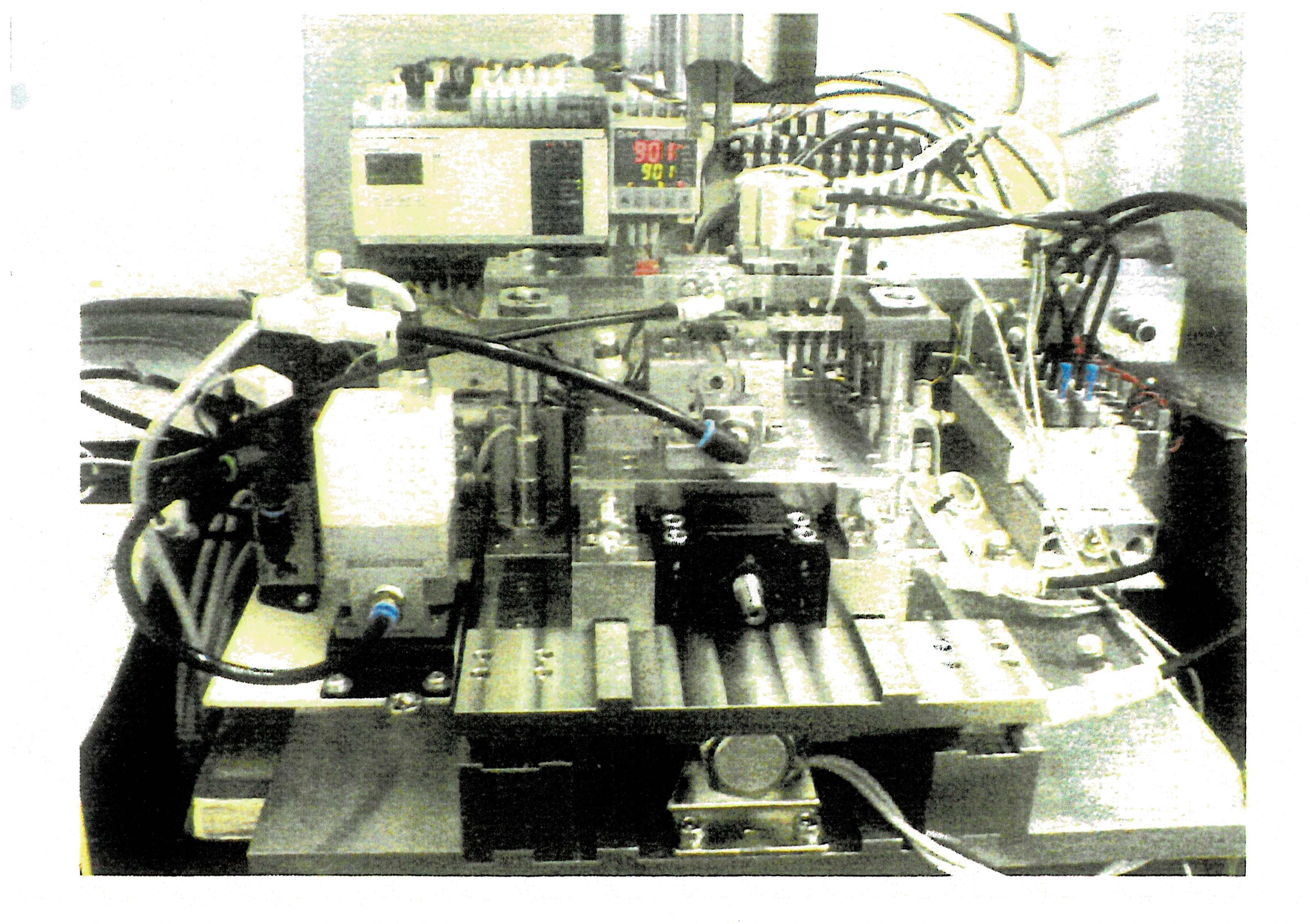
This is the automatic welding device part of plastic parts after the adjustment.

11) Aiming for The Ideal Truck Tyre Checker:
Once I had finished my work investigating the cause, I moved on to my next goal. But, as it turned
out, this was a matter that I could not do alone. The only person in the world who can help me this
is Takanori, my eldest son. By all means, what I have to ask him for is a drawing of the tyre check-
er body to be attached to the air valve. It's a drawing of a tyre checker for trucks that can di-
rectly inflate from the tyre checker into the tyre learned from Mr. Guy J. Walenga. I have
learned from my experience that in order to make the shape compact, it is necessary to separate
the cylinder part that attaches the main body to the air valve. and the device that can read the
position of the cylinder accurately in thousandths of a millimeter. Thereby the posibility of the
tyre checker measurement within ±1%. Leaving aside the accuracy, the biggest problem is how
to create the most compact model that can directly put air into the tyre from the checker
body with an inflator. In terms of specifications, I have explained to Takanori in as much detail as
possible the specifications of the main body of the tyre checker by the separation method. It's
easy to imagine he's struggling to meet the ultra-compact shape I'm looking for. And there is no
doubt that he worked very early to make it in time for the special day. For my mother was not feel-
ing well after the surgery. The information was passed on from my wife to our son Takanori. The
doctor told me to gather my family as soon as possible and I asked my wife to tell Takanori about it
in Kyoto. My mother especially loved my eldest son who was her first grandson. So the date of
completion of the drawings was to be a special day that I will never forget. And he finally finished
it and brought me the drawings. It is easy for me to imagine him on the bullet train from Kyoto
to Shizuoka, facing the drawings.
Before proceeding to the drawings, consider the usage environment of the prod-
uct required for development, and what kind of tyre checker must be made:
First, the specifications of the air valve of the wheel to which the tyre checker is
attached and the situation thereof will be described.
(A)There are two types of truck tyres:
single and double tyres:
Single tyres are mainly used for the front tyers. Double tyers are used for the rear tyers
that support heavy loads. Both single and double tyres are made by assembling a single
wheel.
Therefore, a tyre checker that meets the following three usage conditions is required:
(1) A tool with specifications that conform to the single tyre used for the front wheel.
(2) A tool with specifications that fit the tyre for the inside of the Double tyre.
(3) a tool with specifications that fit the tyre for the outside of the Double tyre.
These (1), (2), (3) specific wheel and air valve positions are photographed:
First show photo No. 1 about (1):
The shape of the single wheel used for the same tyre is the same. However, the shape seen
from the front side and the shape seen from the back side are different. What is required in
(1) is the shape seen from the front side of the wheel. The eight or ten small holes in the
center are holes that go into the bolts of the hub, which are clamped with nuts and the tyres
are fixed to the vehicle.
It is the orientation of the air valve, which is facing the front side.
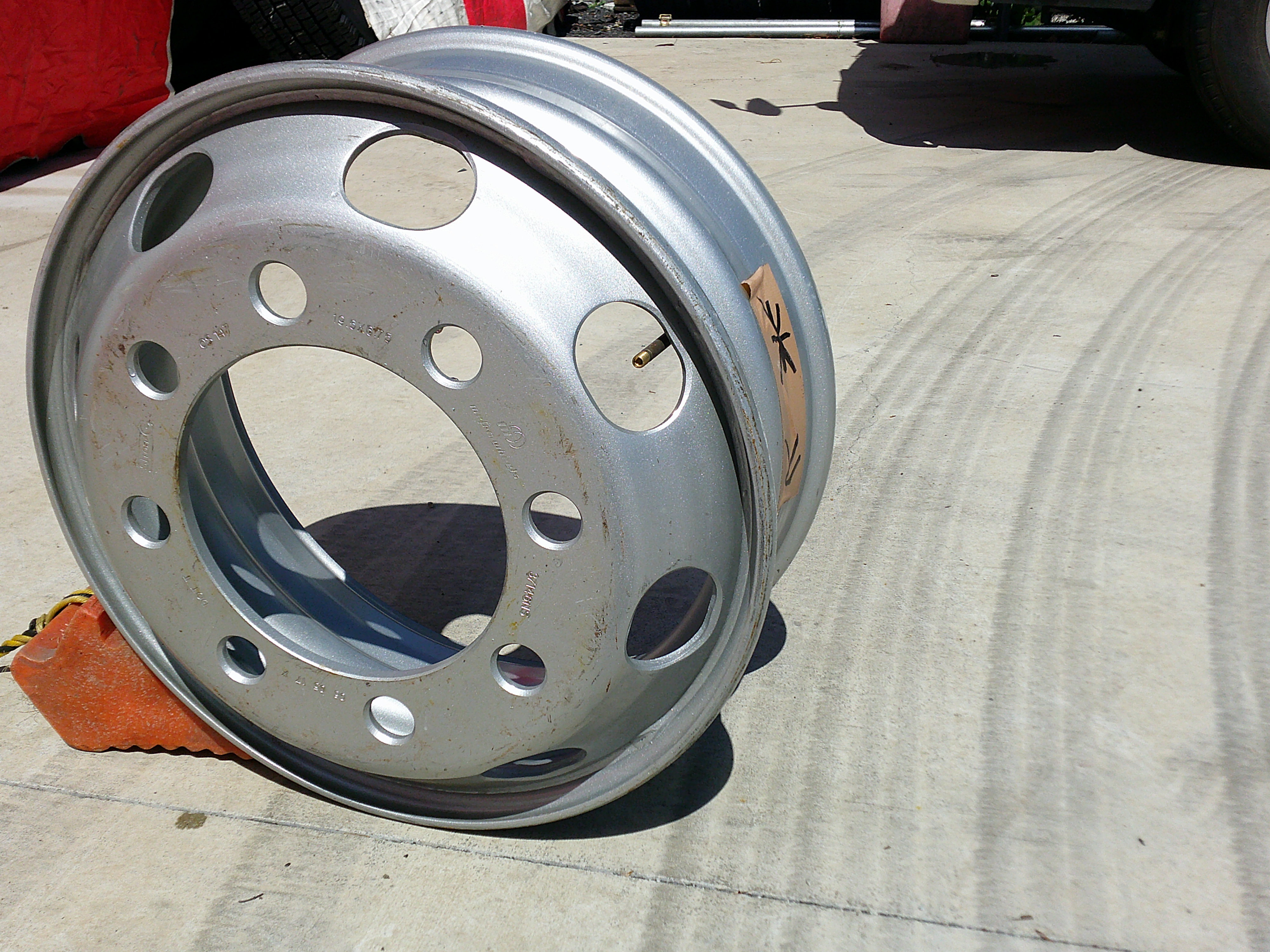
Second show photo No. 2 about (3):
a) This is a photo of the shape seen from the back of Photo No. 1. The same wheel of No.1.
b) The feature of Photo No. 2 is that the direction of the air valve is opposite to Photo No. 1.
Photo No. 1 and Photo No. 2 made it clear that the direction of the air valve is opposite on the
front and back sides of the wheel, even though they are exactly the same wheel.
c) (3) requires specifications that are the most difficult to respond to tyre checkers. The big-
gest reason is that, unlike (1) and (2), there is a limit to the distance between the tip of the air
valve and the wheel. The tyre checker must work within the size of the hole.
d) (3) is, of course, an explanation in Double tyres. However, since (3) is the wheel that becomes
the outside of the double wheels, it is the same as photo No.2, the surface from the back side
of the single wheel.
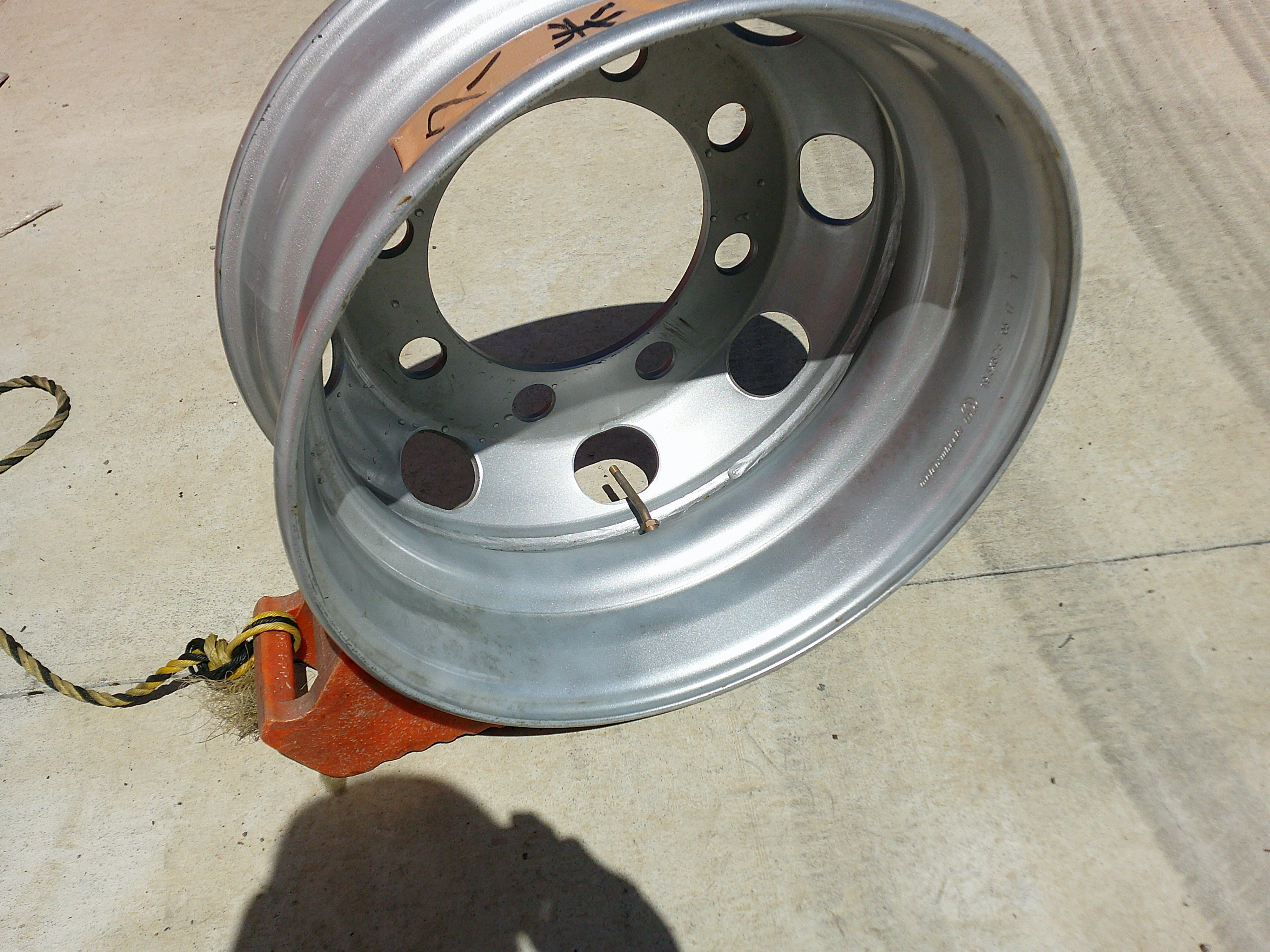
Third show photo No.3 about (2):
a) In the case of double tyres, the two wheels are connected so that the position of the air
valves facing each other is rotated 180 degrees, so that the holes with each air valves do not
block the path through which the inflator handle passes.
b) The double wheels assembled in this way do not cause any problems even if they are attached
to the vehicle on either side of the rear wheels. For example, in this state where two are lined up
when used as the left rear wheels: First, the wheel is assembled as a tyre, then a small (8-10)
holes of the right wheel are inserted into the hub bolts, and when it is completed, the same hub
bolts are passed through the holes of the left wheel in the same way. The two wheels are then
firmly fixed to the hub by nuts and attached to the vehicle. In case of the right rear wheels:
The hub bolts are inserted into the holes of the left wheel and finally the hub bolts are inserted
into the holes of the right wheel, the right wheel becomes the outside of double tyres.
c) If the front sides of the wheels are connected in a state facing each other, it shows that
the same can be handled regardless of whether it becomes the rear wheel on the left side or on
the right.
d)Both sides of the double wheel become all the outside of the wheels. Photo No.2. And the
photo of the air valve in the center of the double wheels will be No. 1 for both. However, unlike
the front wheel of a single wheel,it is a double wheel, so the inflating handle up to the air valve
needs to be longer for one single wheel.
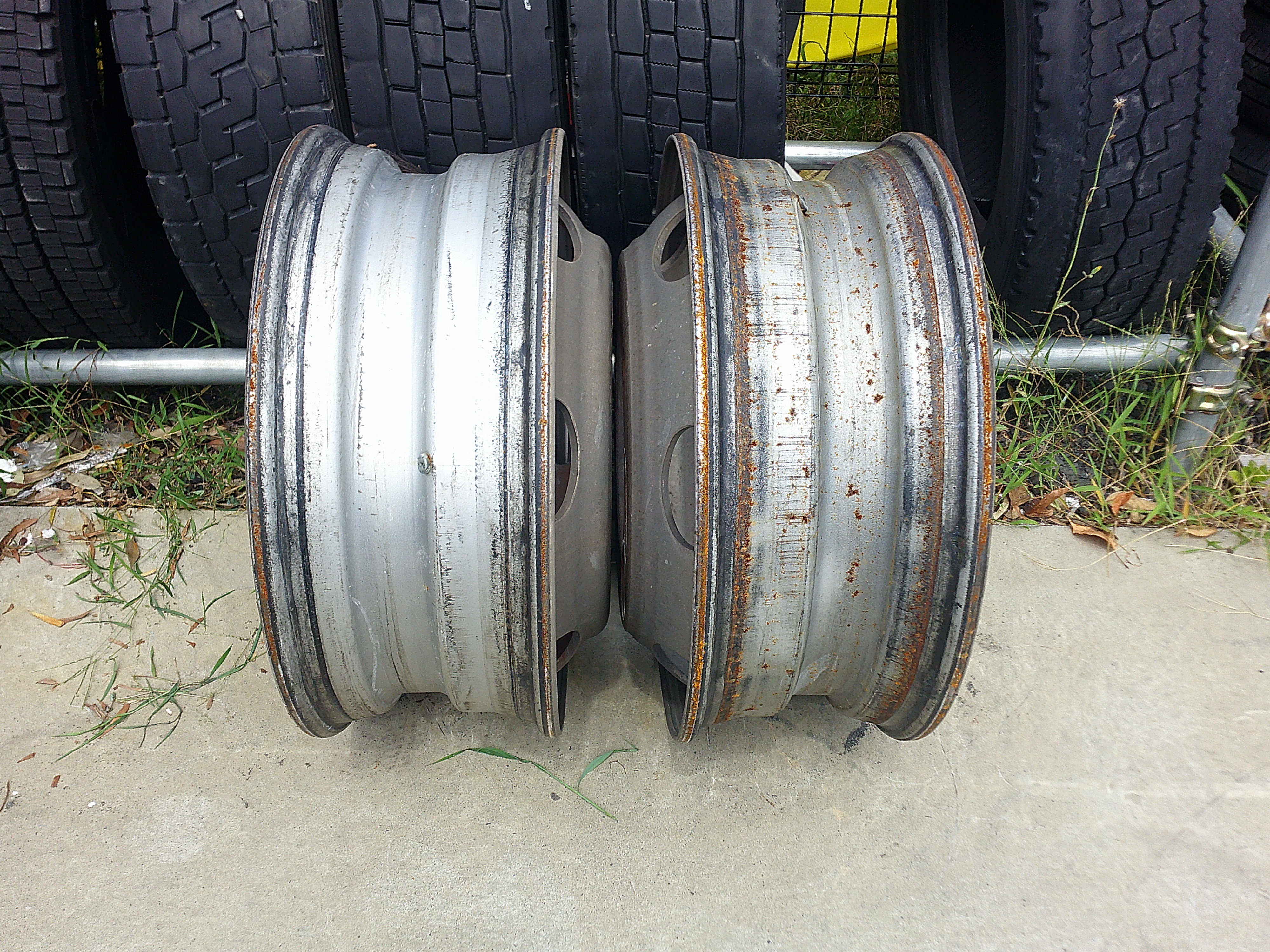
Fourth show photo No.4 about (1):
a) From Photo No. 4, the wheels are connected in two, but it is confirmed that the air valve faces
the front side as in Photo No. 1.
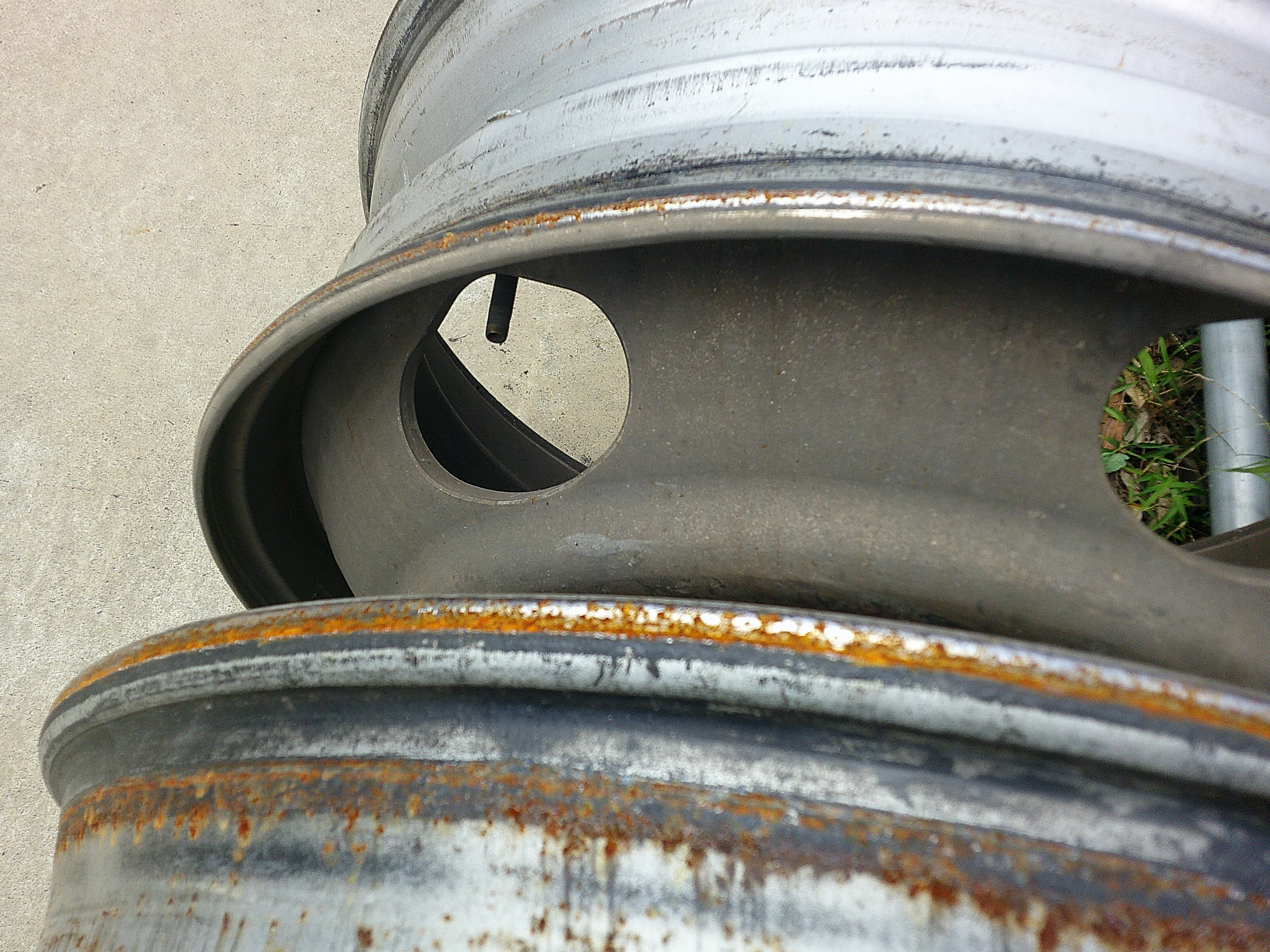
(B)Determining Tyre Checker Specifications:
The tyre checker we develop must be able to cope with the air valve of the following
three wheels.
1) To support the front wheel Single tyre's air valve, it should be compatible with
Photo No. 1.
2) As for the rear wheels, the inside tyre of the double wheels have the same ori-
entation as the AIR VALVE in Photo No. 1. However, since the air valve is one
wheel inside, the length of the handle needs to be increased accordingly.
3) In contrast to the rear tyre inside the rear wheel, the outside tyre should be com-
patible with Photo No. 2. And this is the most difficult job.
In order to meet these three conditions, the development of tyre checker was carried
out, and the time has come to give shape to them as products.
On the wording precautions:
(1) Frontside of the single wheel & inside of the double wheels or tyres: Photo No.1
(2) Backside of the single wheel & outside of the double wheel or tyres: Photo No.2
(C) This is the body drawing for truck:
This Resin design drawings shows the date November 10th, 2009. In fact, it was com-
pleted a year ago, and I have been spending about a year developing the measure-
ment section.
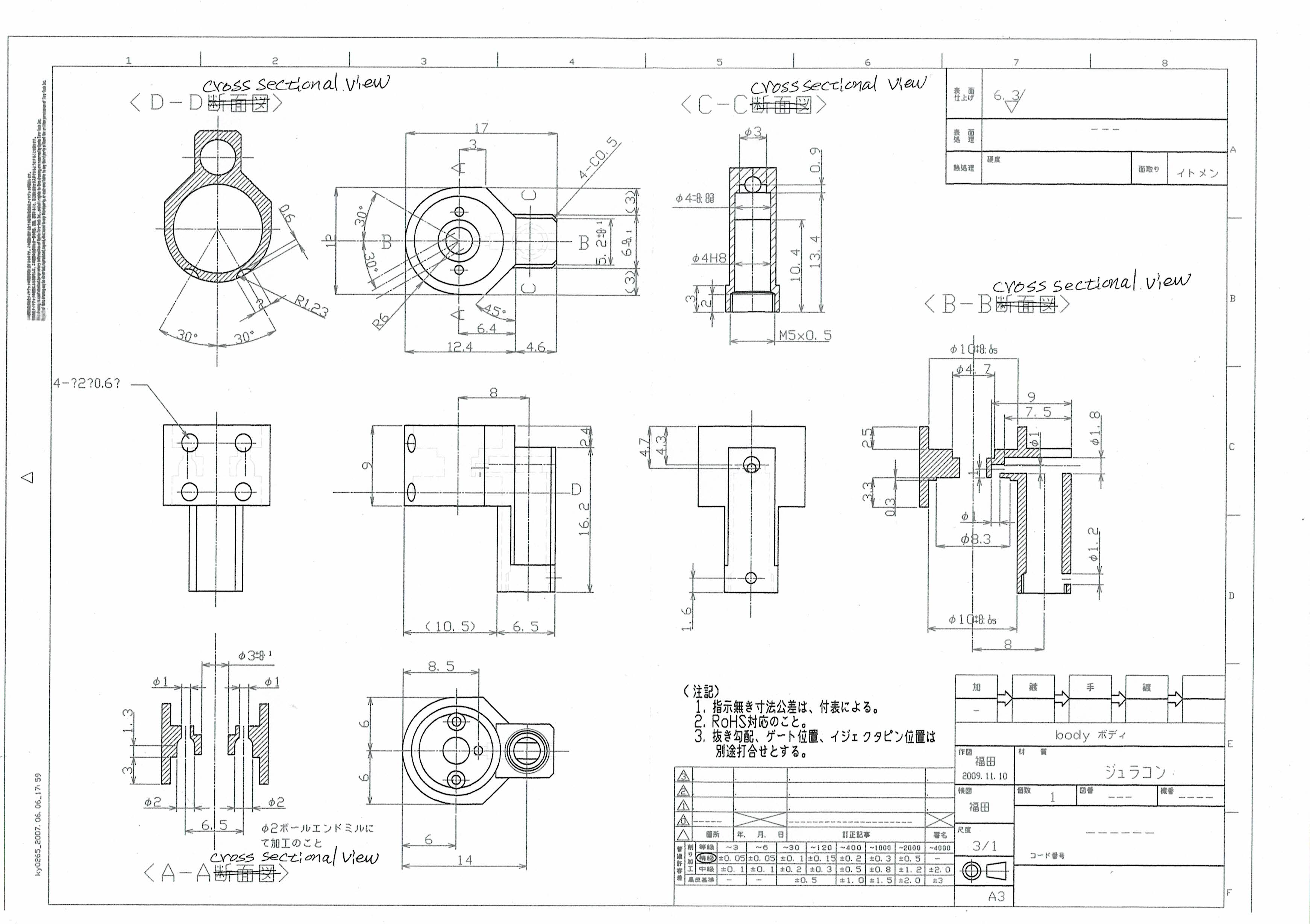
Photo of the finished product developed as a separation method:
(D)Main Body:
@ In the same way as an air valve, it allows air to be filled into the tyre from the
main body.
A A cylinder for measuring tyre pressure is provided, and the mechanism moves
according to the high and low air pressure within a predetermined range, and the
cylinder stops at a position, where the predetermined air pressure and the built-in
spring force are balanced.
BA special magnet is used so that the stop position can be accurately pin-pointed.
As a result, measurement in units of thousandths of a millimeter becomes possible.
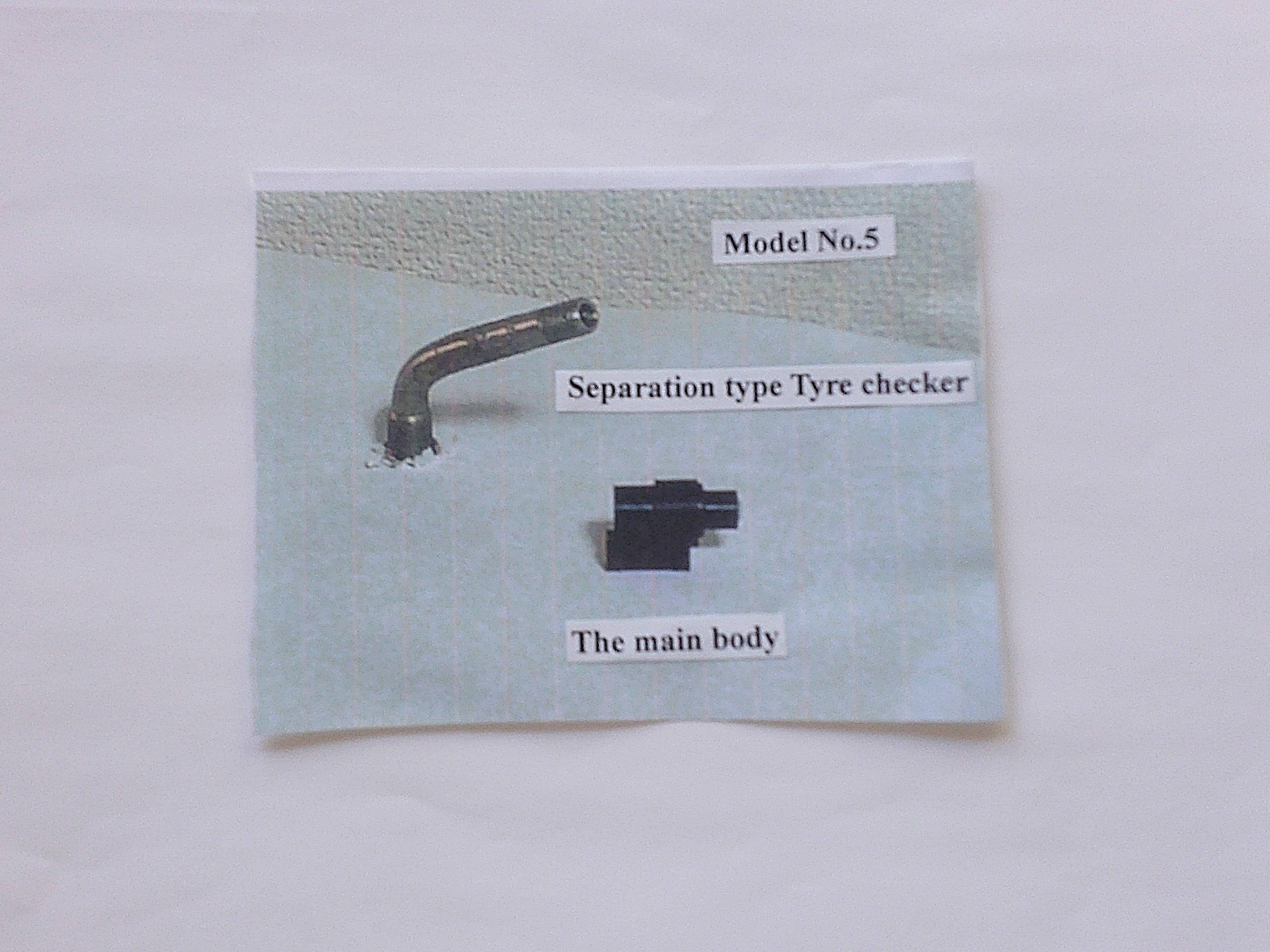
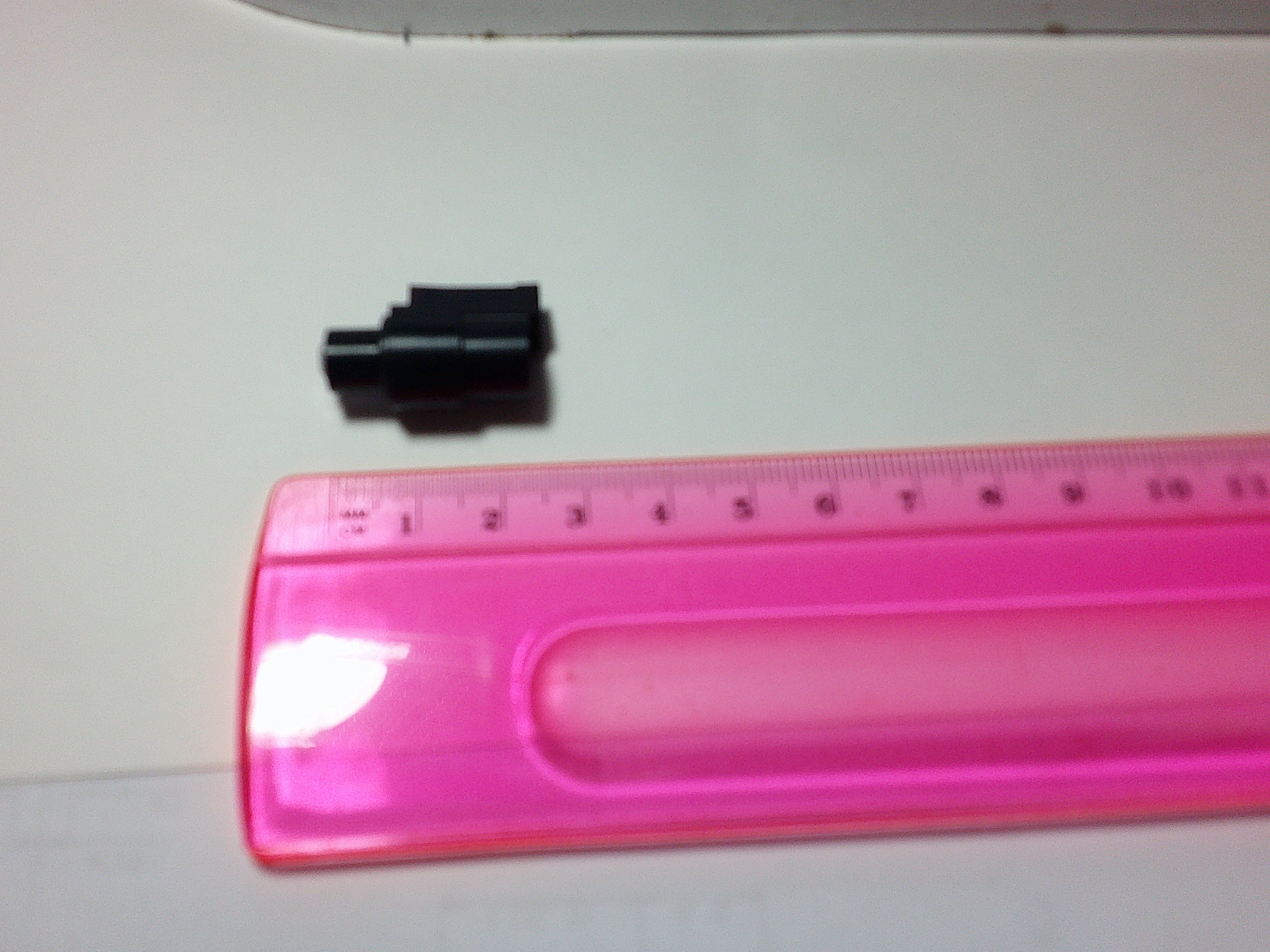
(E)Measurement section drawing:
I drew a drawing of the measurement part and asked Takanori to draw the drawing,
which is the next drawing. This is because, in order to make a prototype, I asked
Takanori for a drawing to be given to a resin mold manufacturer for an estimate.
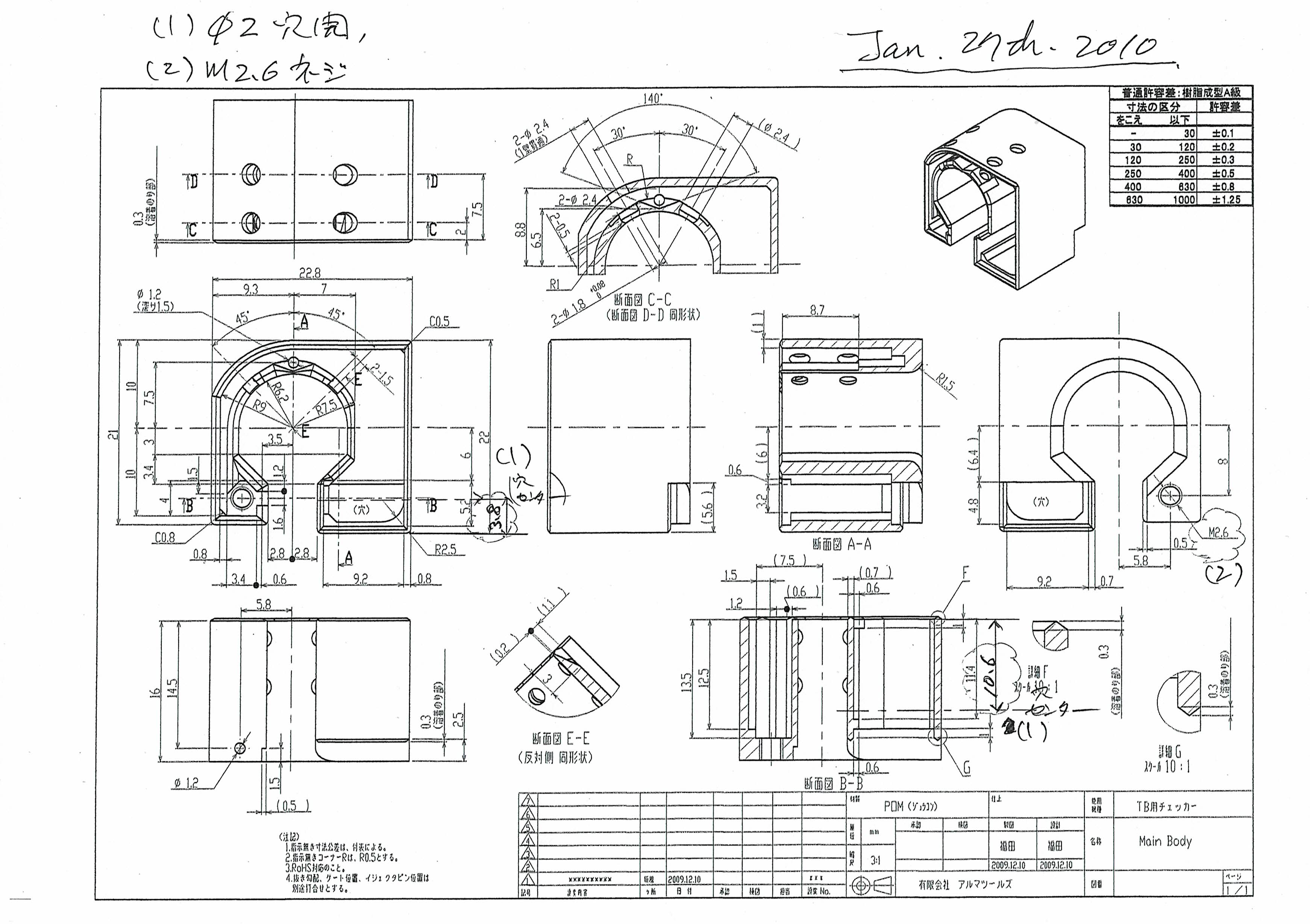
(F)The photos show the parts of the molded:
measurment section and the assembled ones.
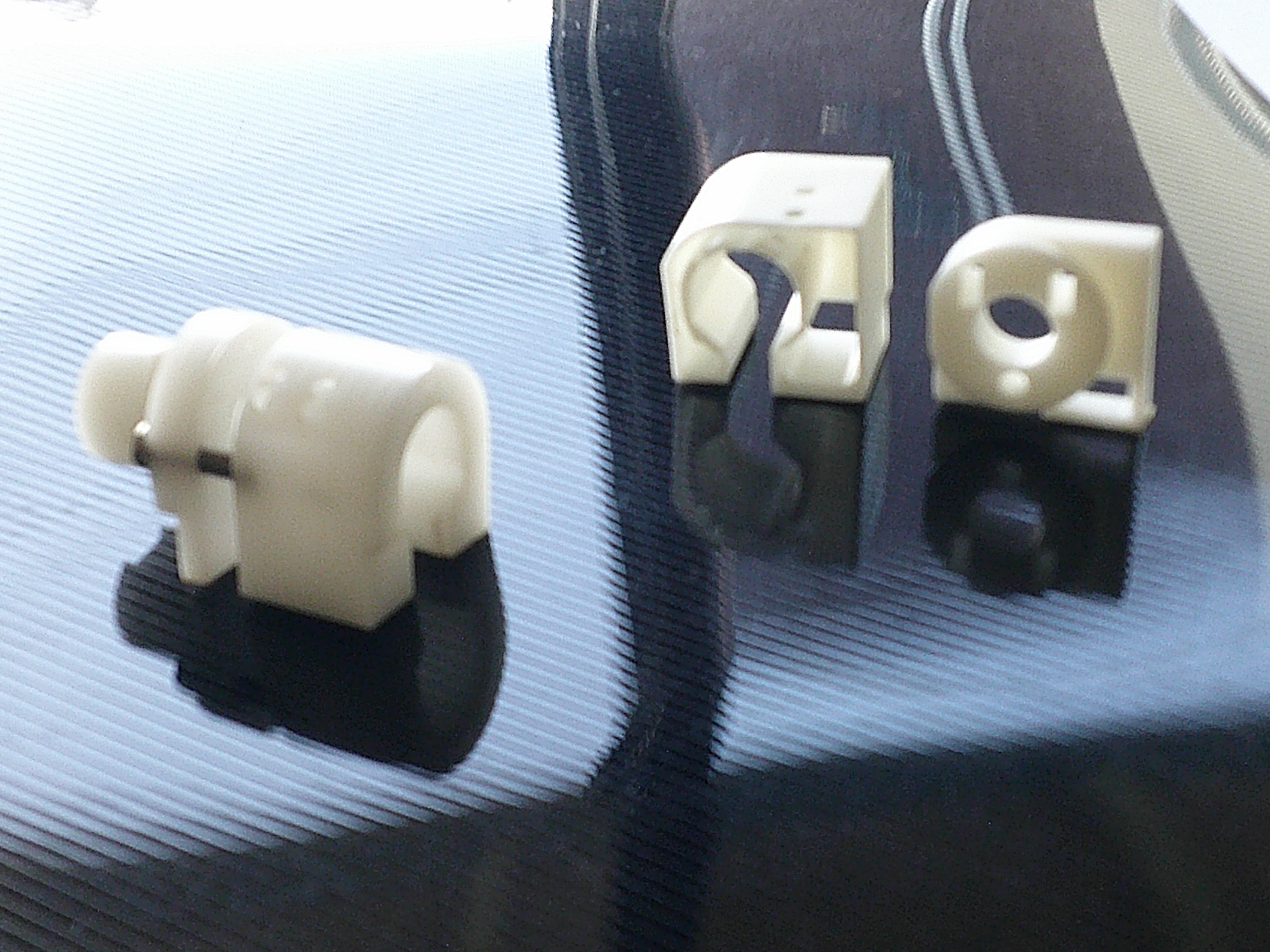
(1) Of course, I didn't jump to the mold drawings. As shown in the photo on the left,
I first make a mock-up, and then I check everything in advance to see if there are any
problems, and then proceed to the molding mold drawing.
The following parts become the next photo.
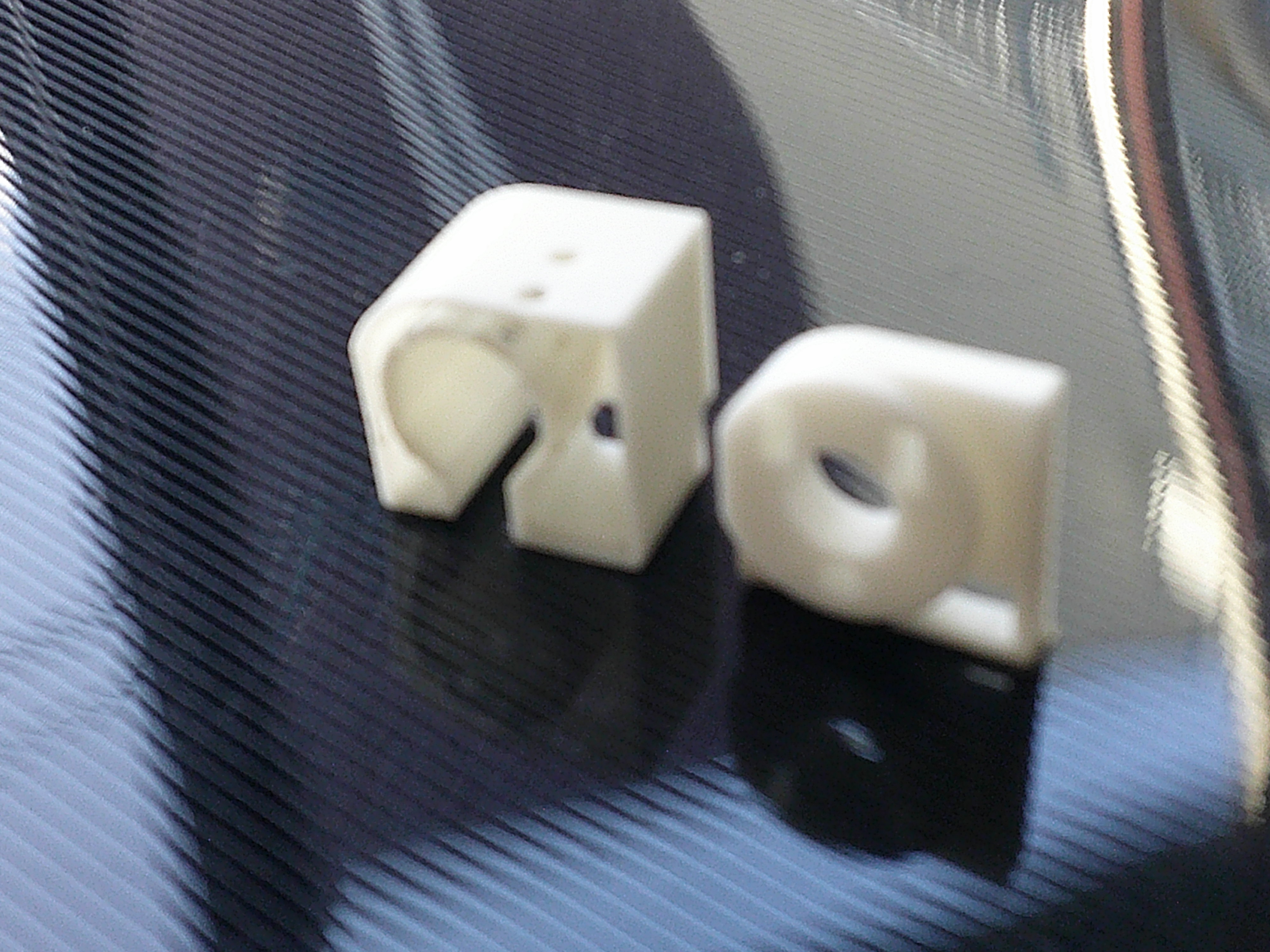
(2) On the left is a completed photograph of the measurment section. The Meas-
urement section is called the Tip unit, and is attached to the tip of the Handle unit
as a detachable part. This is because in order to respond to Outside tyre, No.2, it is
necessary to make it detachable.
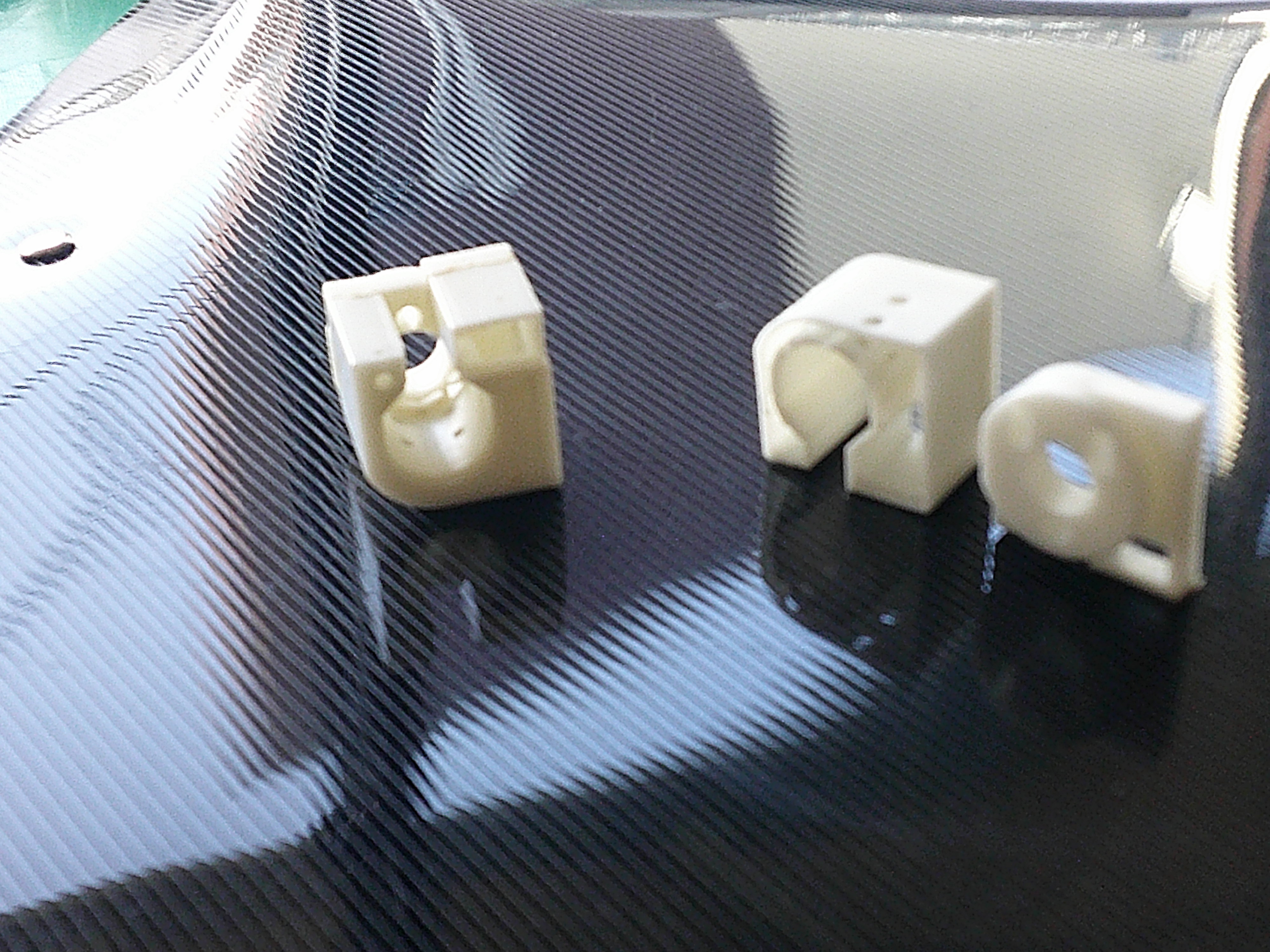
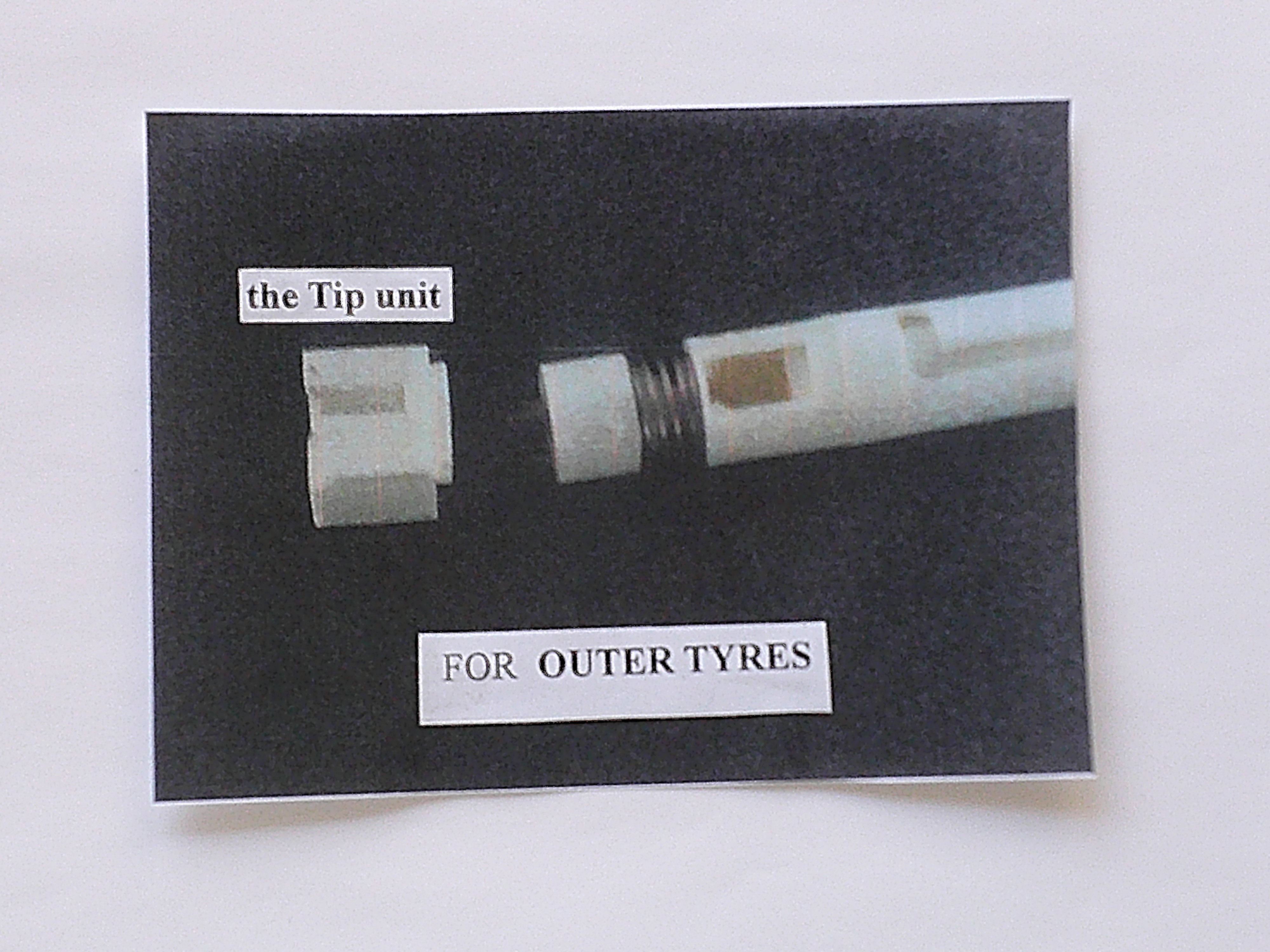
(G)Handle unit:
(1) Has a function to measure the exact position of MG in the main body
(2) display the air pressure by a predetermined method.
(3) The air pressure display by Ultra-bright LEDs is 5 up to (a)-(e).
(a):Over-pressure
(b):Proper air pressure
(c):Air pressure replenishment within a week
(d):Insufficient air pressure
(e):Abnormal air pressure shortage: An emergency such as a puncture is occurring.
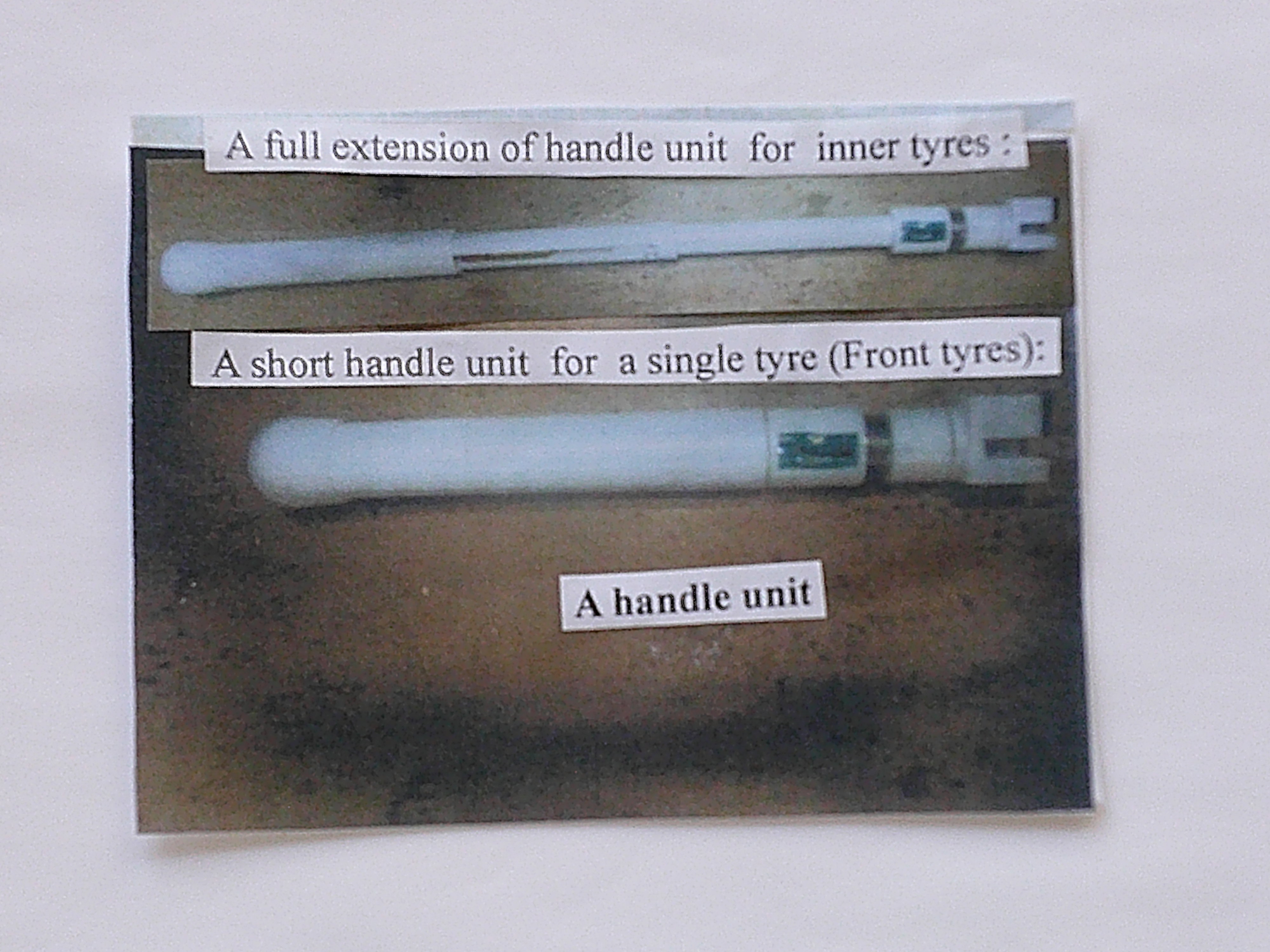
(4) Since truck tyres are numerous, we have to deal with the electricity consump-
tion of ultrabright LEDs. If the need arises for charging, the longer the charging time,
the less valuable it is as a product. We will complete a product that takes all of these
into consideration. In this regard, too, we have come up with an innovative method.
(5) As long as the handle unit is used, the handle unit has two built-in AAA batter-
ies, and has enough power to respond to use as a power source for the display.
(6) The biggest problem is when the Tip unit is detached to accommodate the out-
side tyres. To address this problem, we adopted one of the largest high-performance
capacitor components made in Japan that fits into the space of the Tip unit. As a re-
sult, when the power of the Tip unit drops, the Tip unit is fitted to the tip of the
Handle unit and it is charged instantly, so you can remove the Tip unit and continue
working. There is no need to worry about taking a long time to wait for charging.
H)The docking status:
the main body and the tip of the handle unit:
In the case of (1) and (2) of the three conditions for the
use of Tyre Checker:
In case of Front tyres, and the inside of double tyres:
This applies to single tyre (front wheel) and double tyre inside tyres: i.e.
Photo No.1, and Photo No.3 & 4.
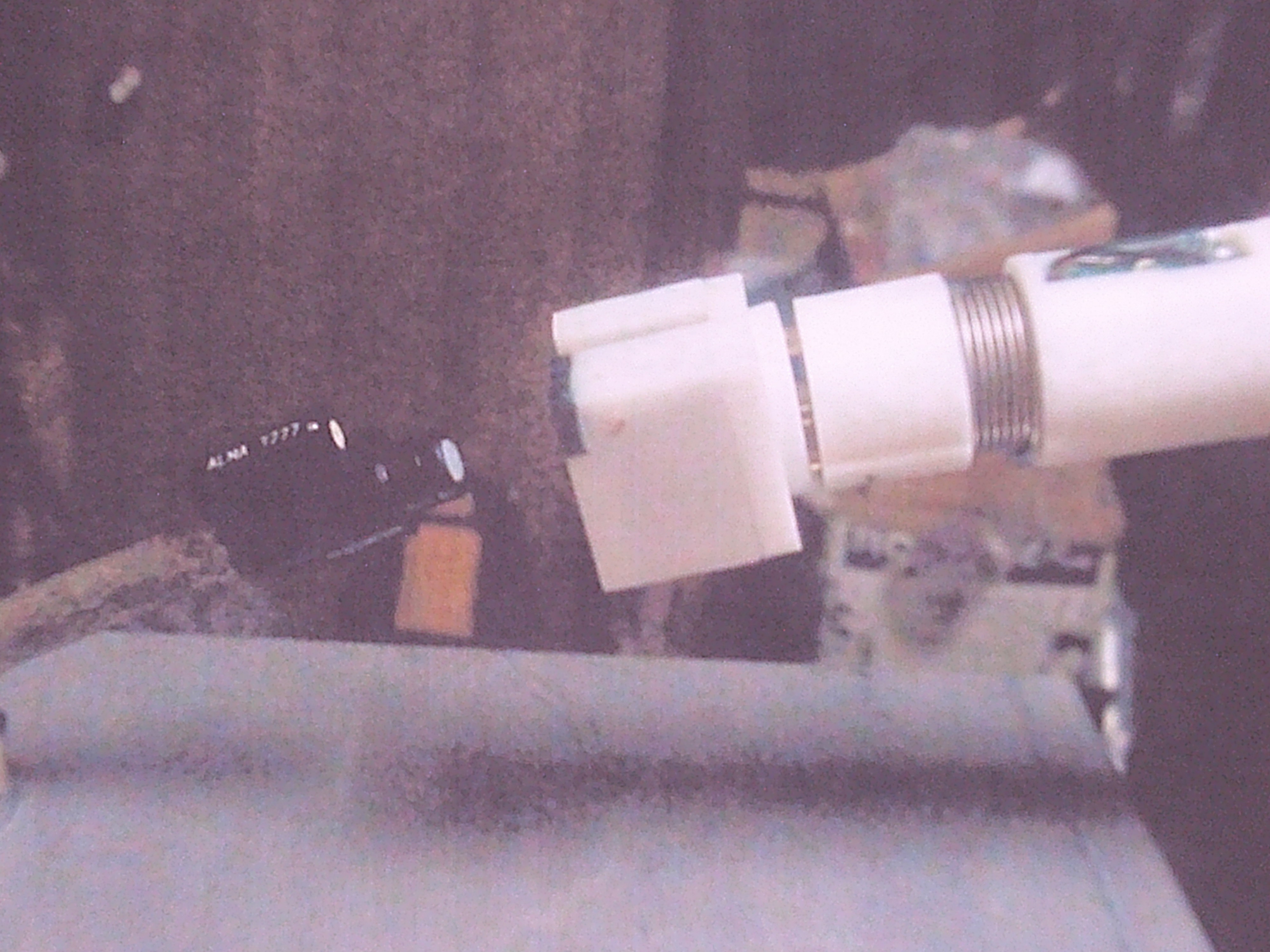
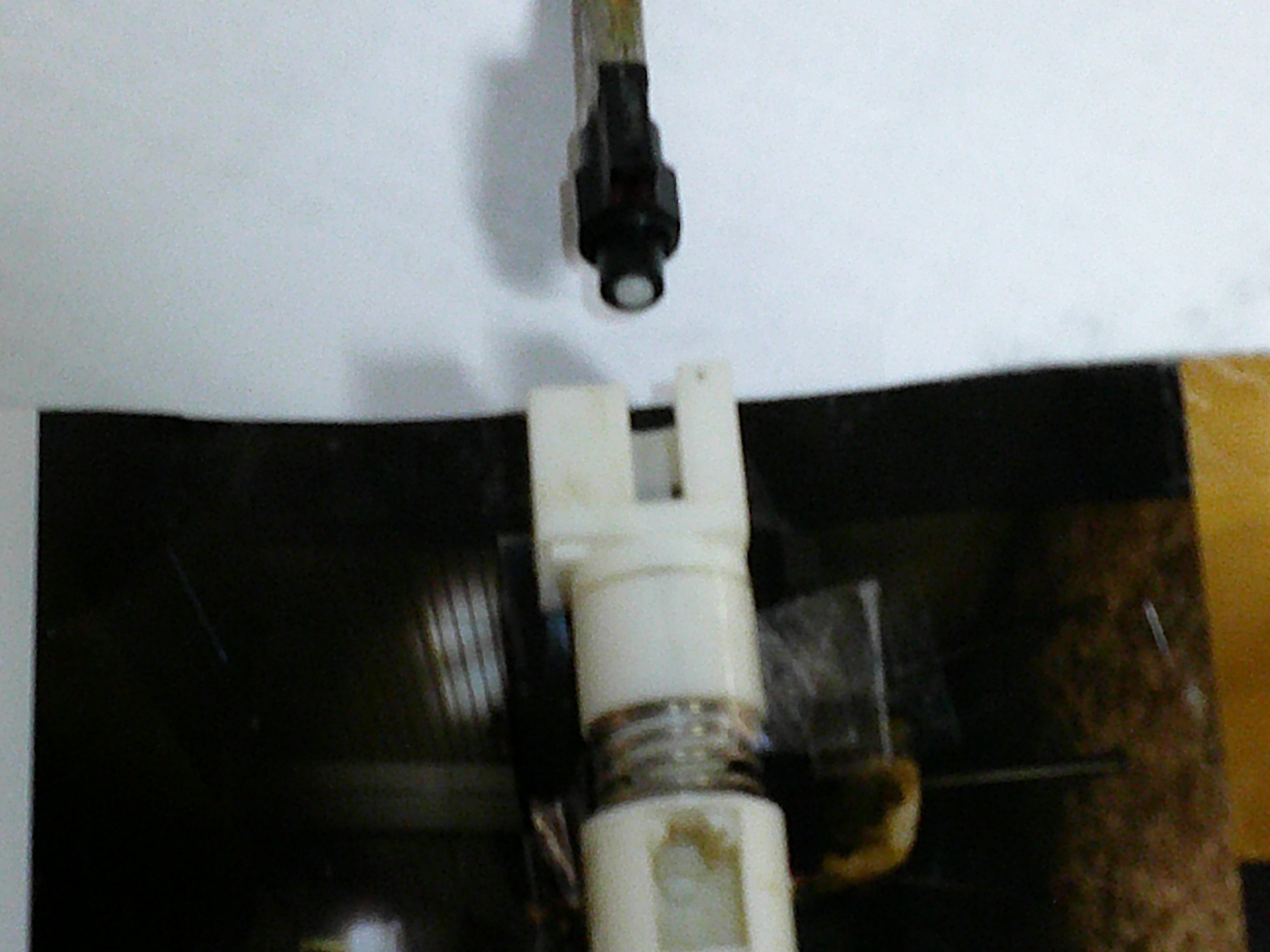
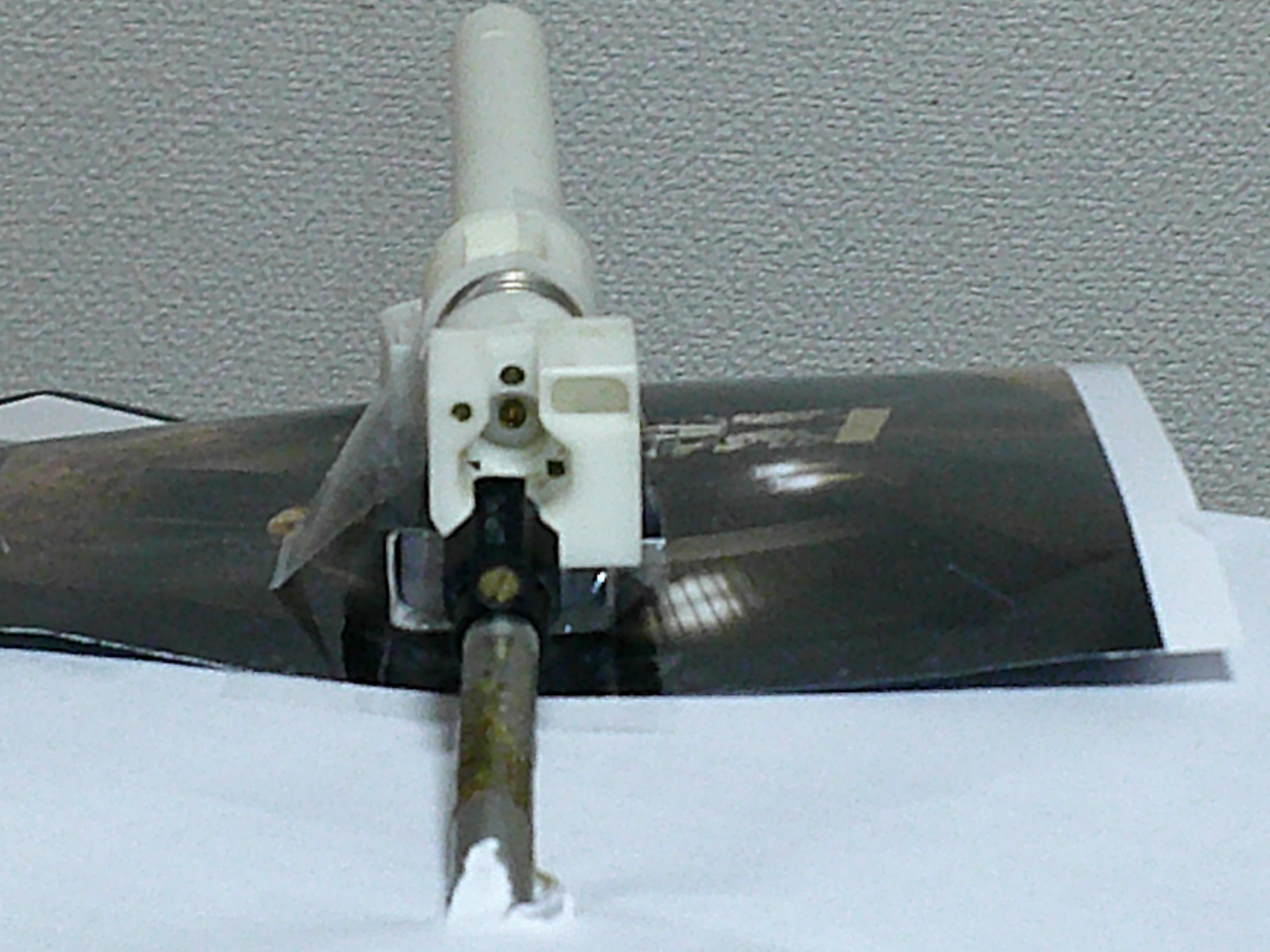
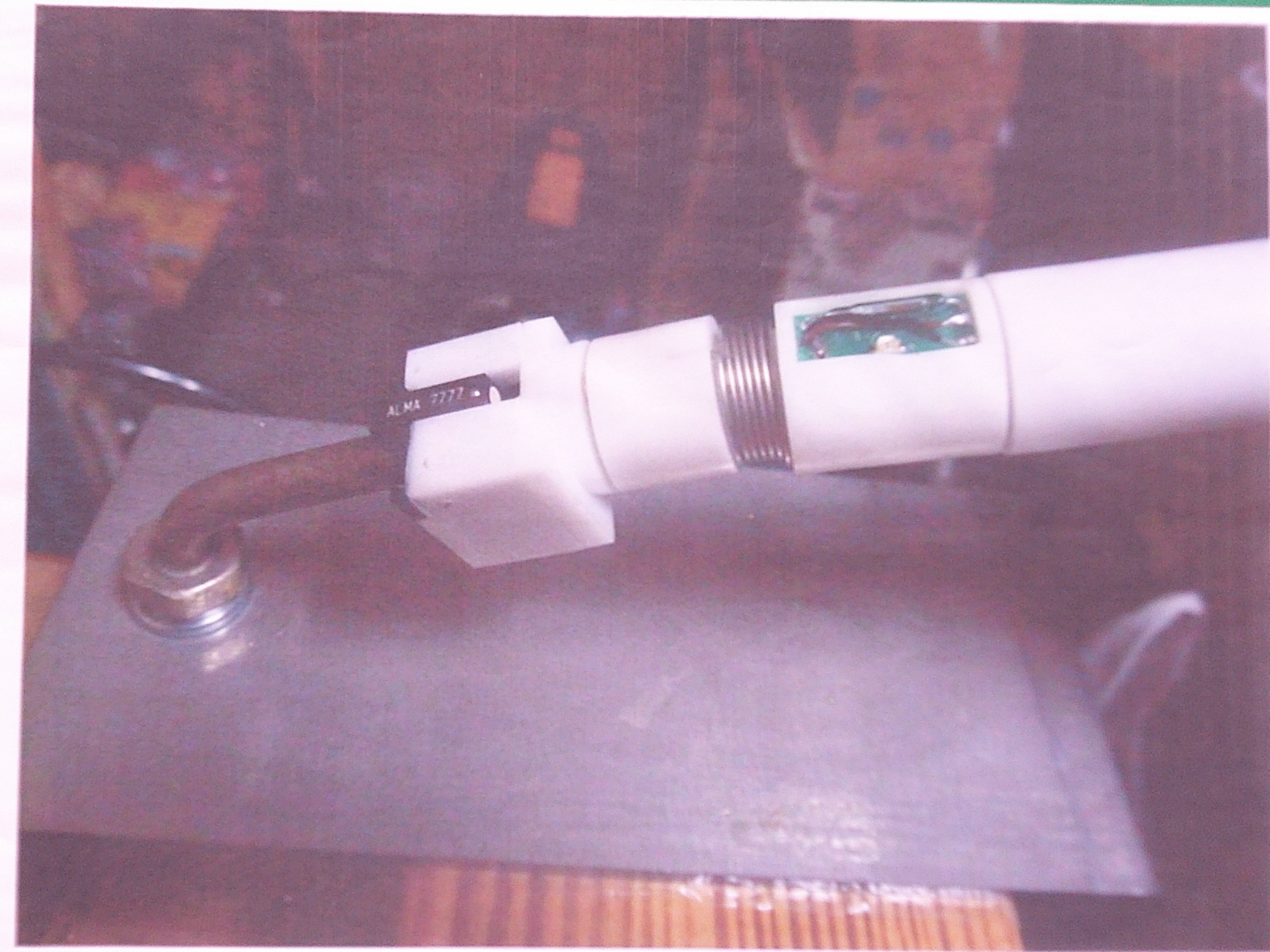
2) Next is Photo No. 2, which is the biggest challenge:
Front side or outside of the double wheel or tyres.
In order to be able to measure in the limited wheel hole in Photo No. 2. It is necessary to make
sure that the tip of the handle, which is the measurement section, comes off. You can under-
stand it from the following pictures.
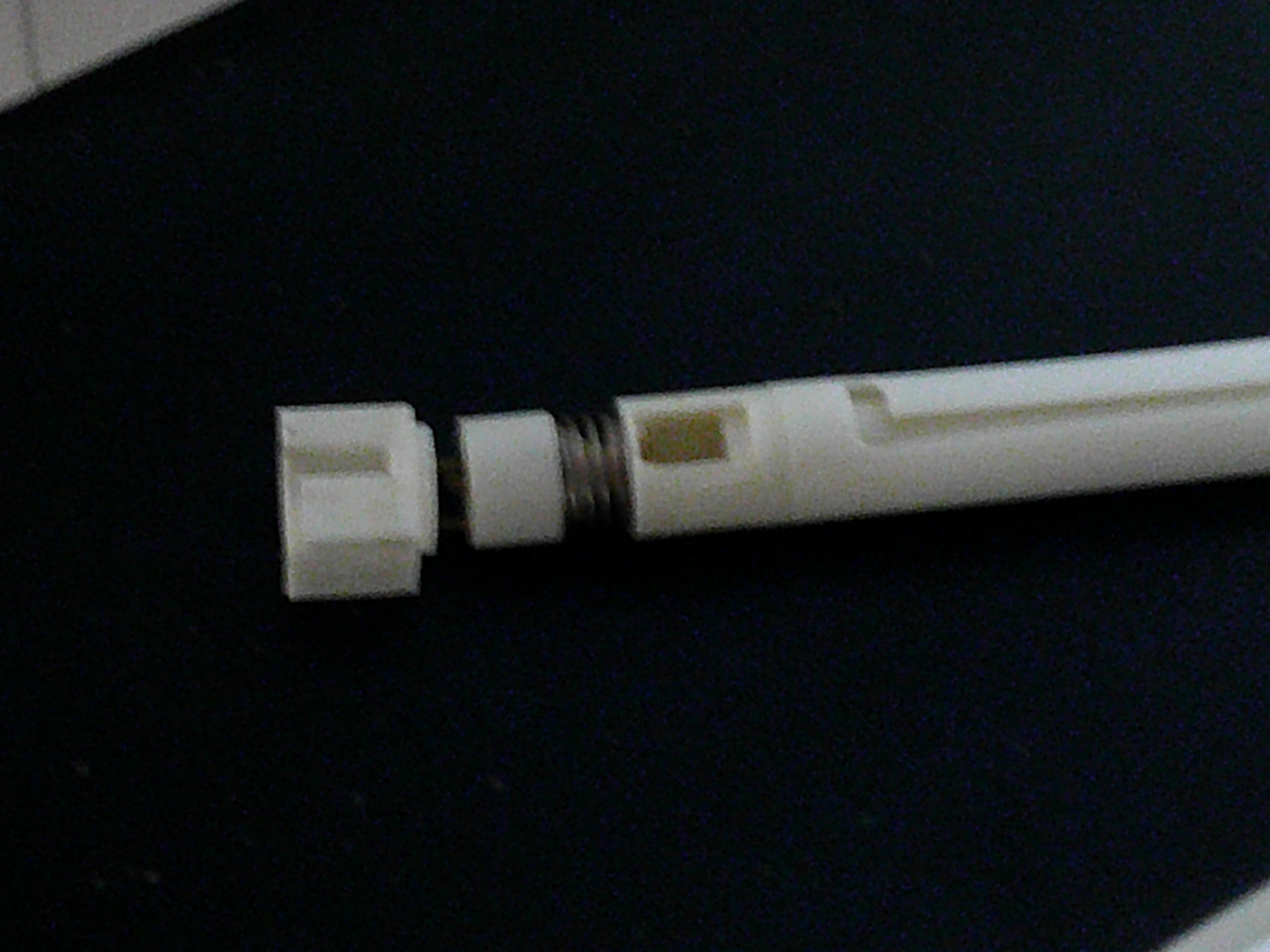
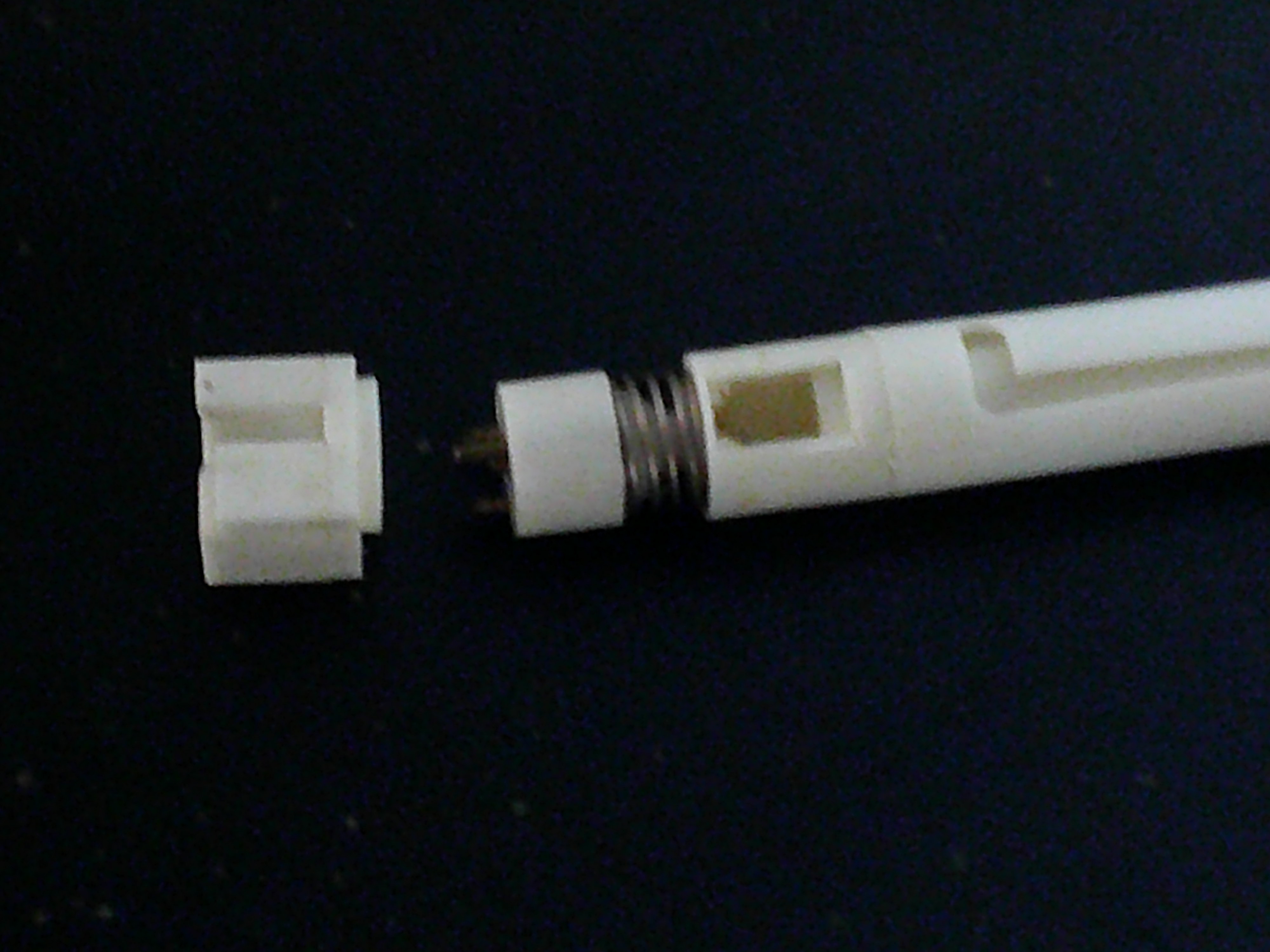
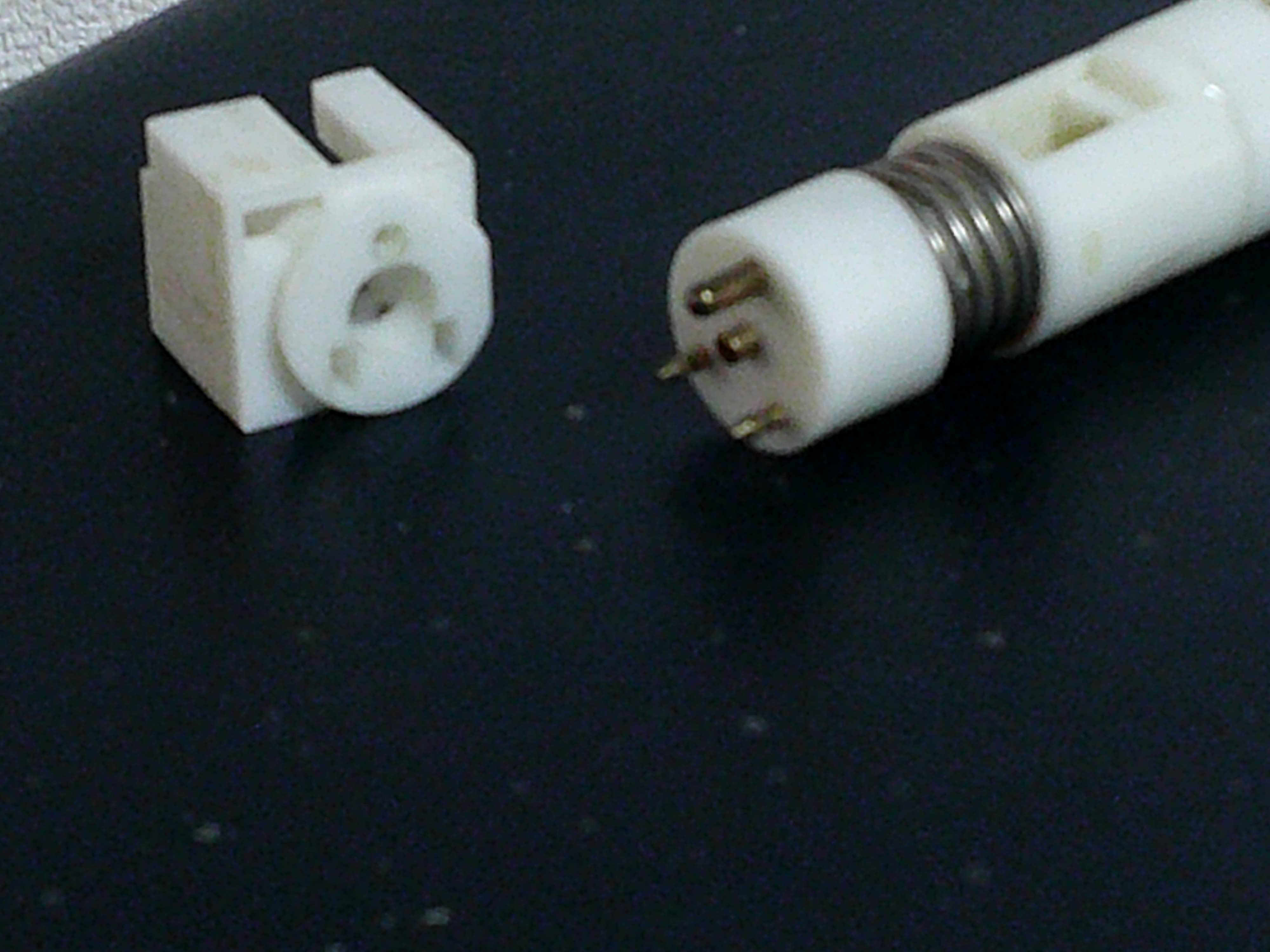
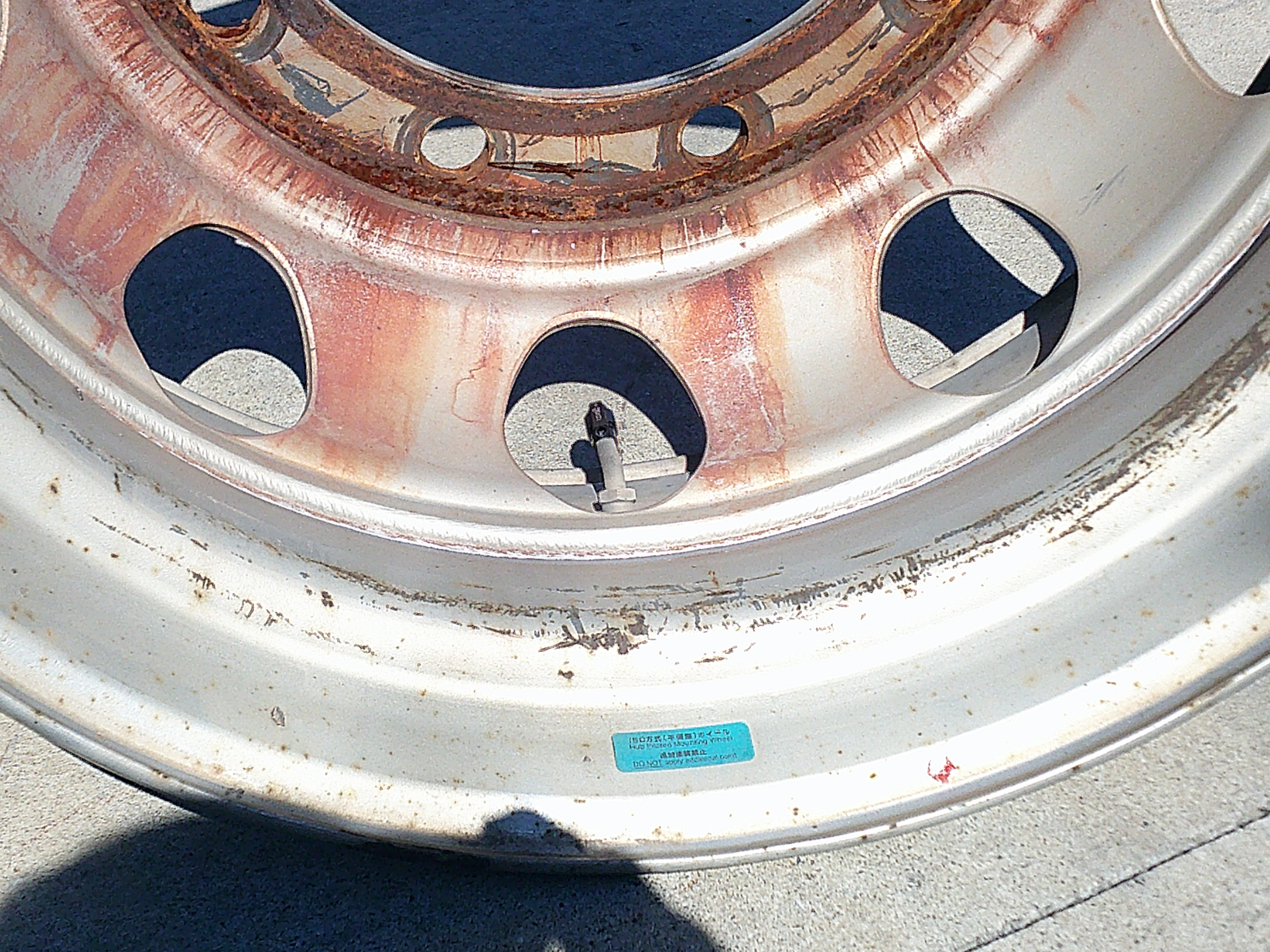
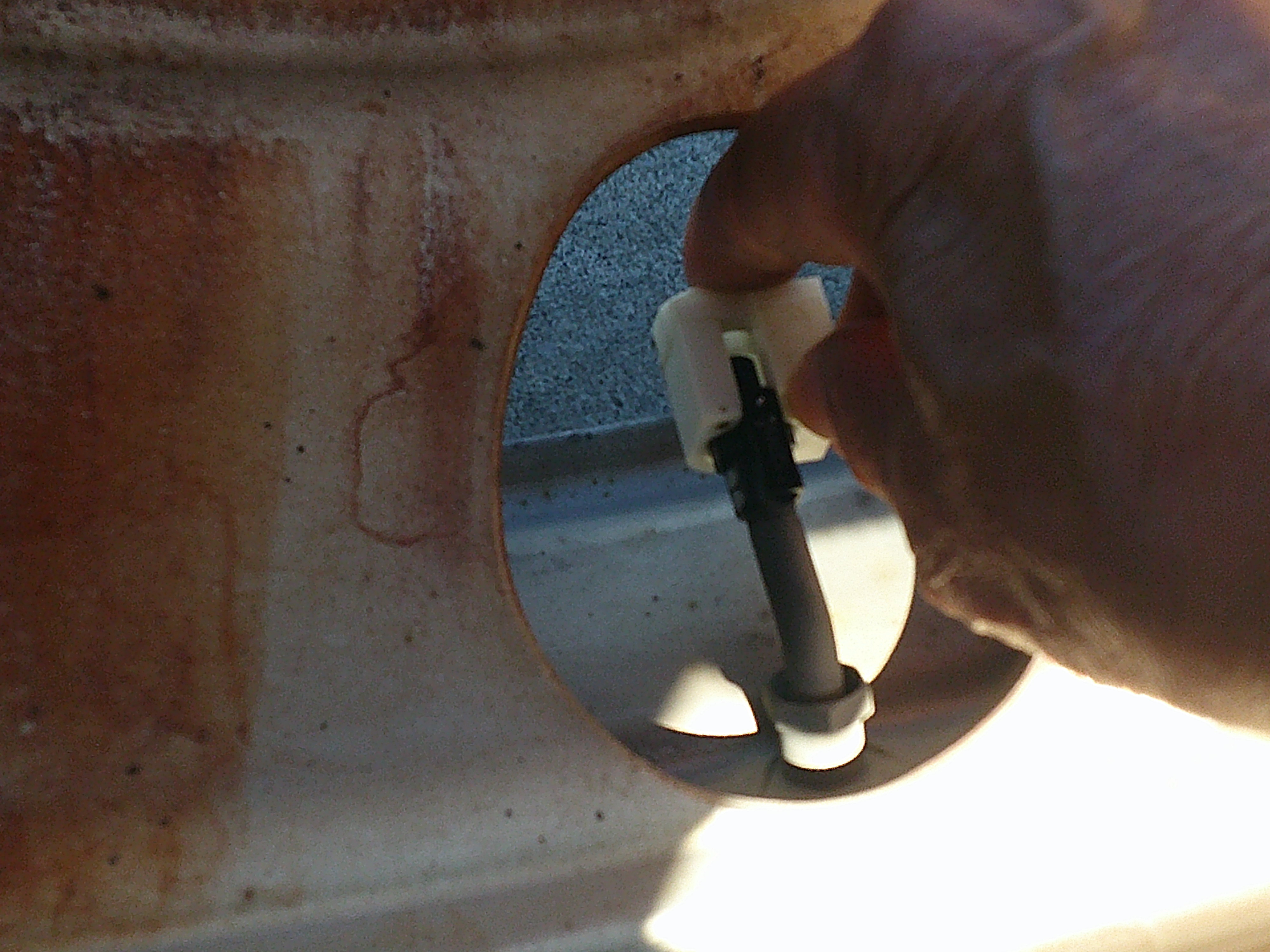
I) The following photos are a general view of the assem-
bled parts used in the new tyre checker for the truck tyres.
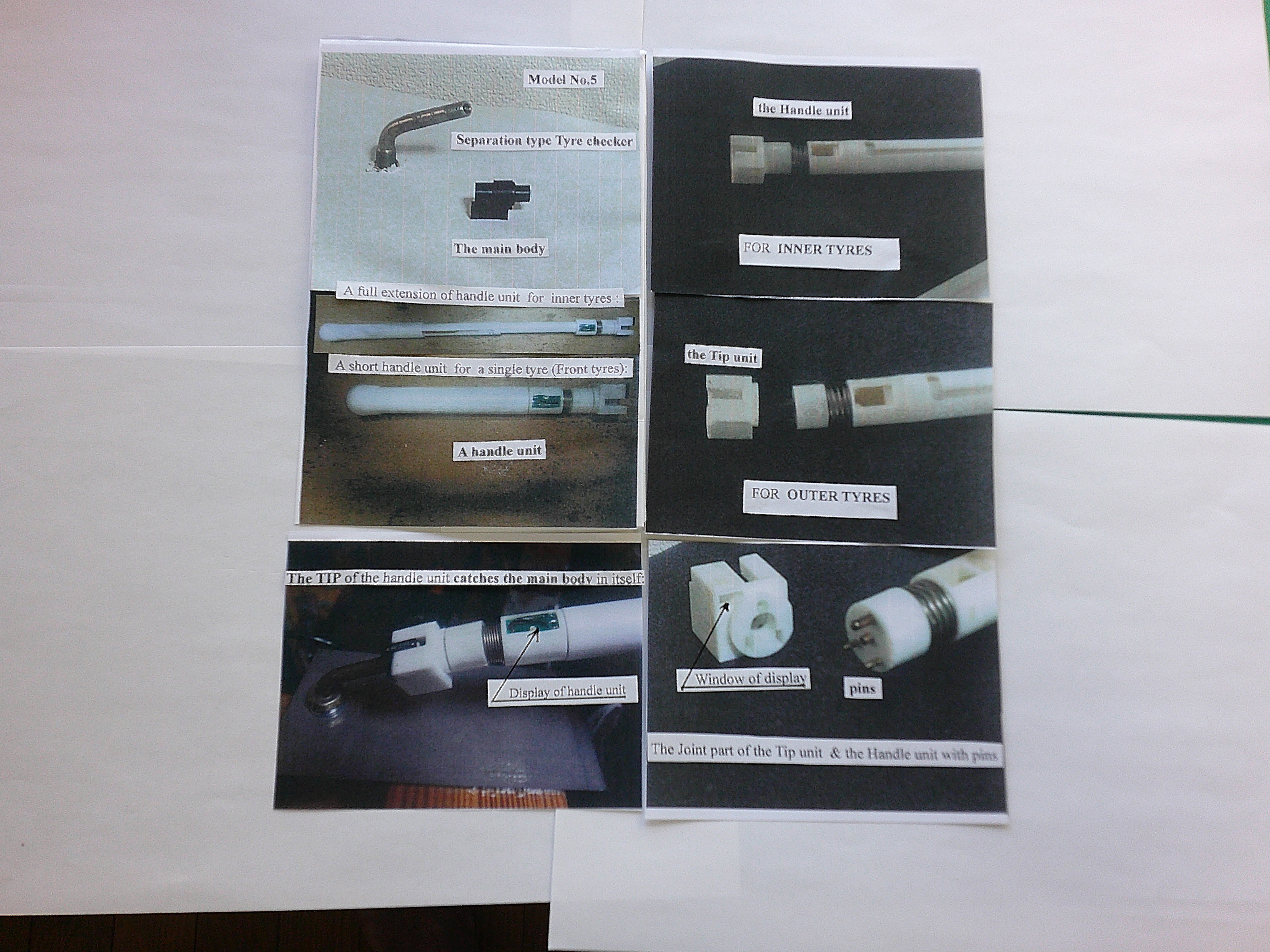
J)Let's see how to check the tyre pessure:
using a tyre checker.
The main body of the tyre checker is assumed to be attached to
the air valve.
(1) Single front tyre:
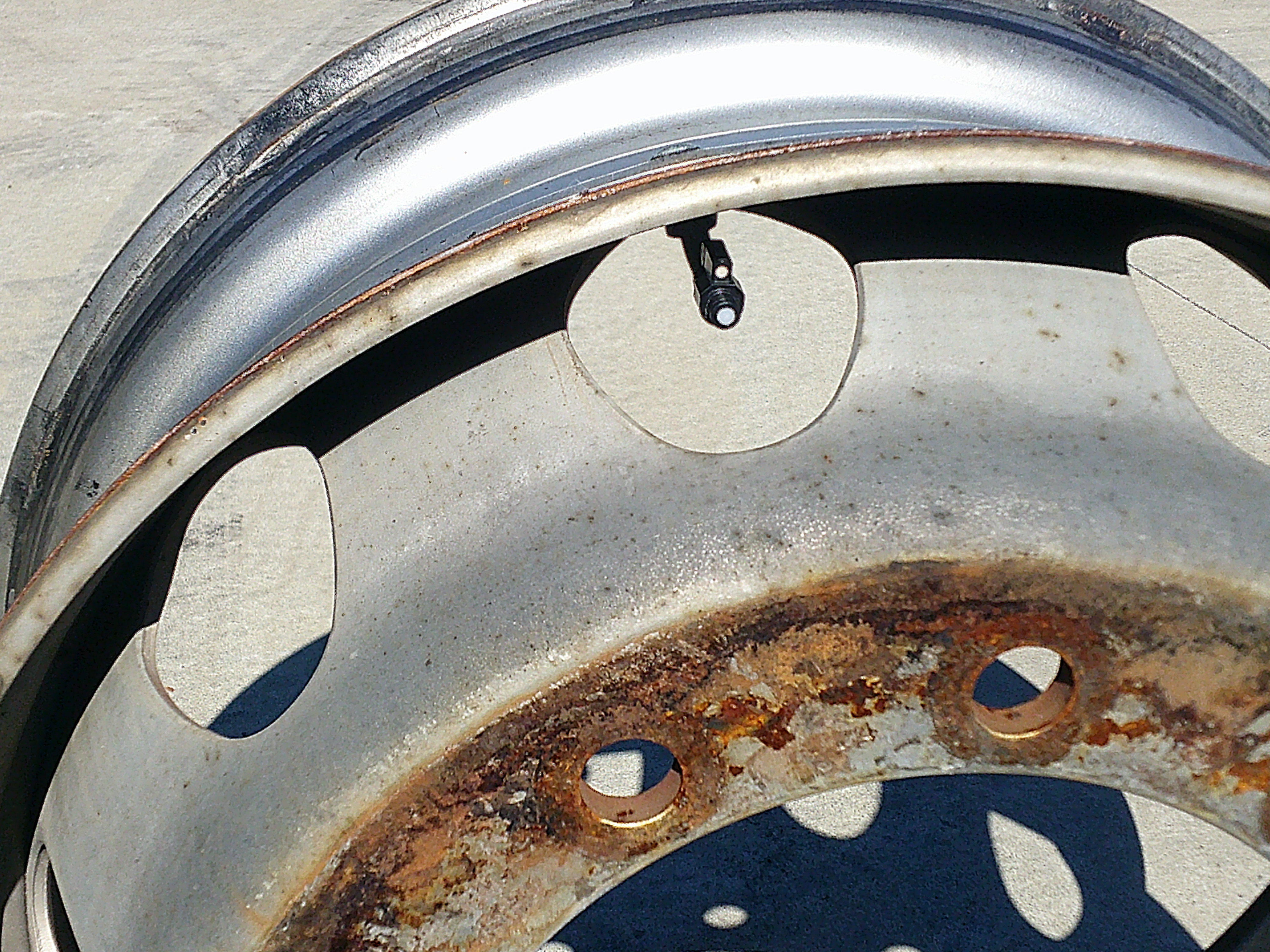
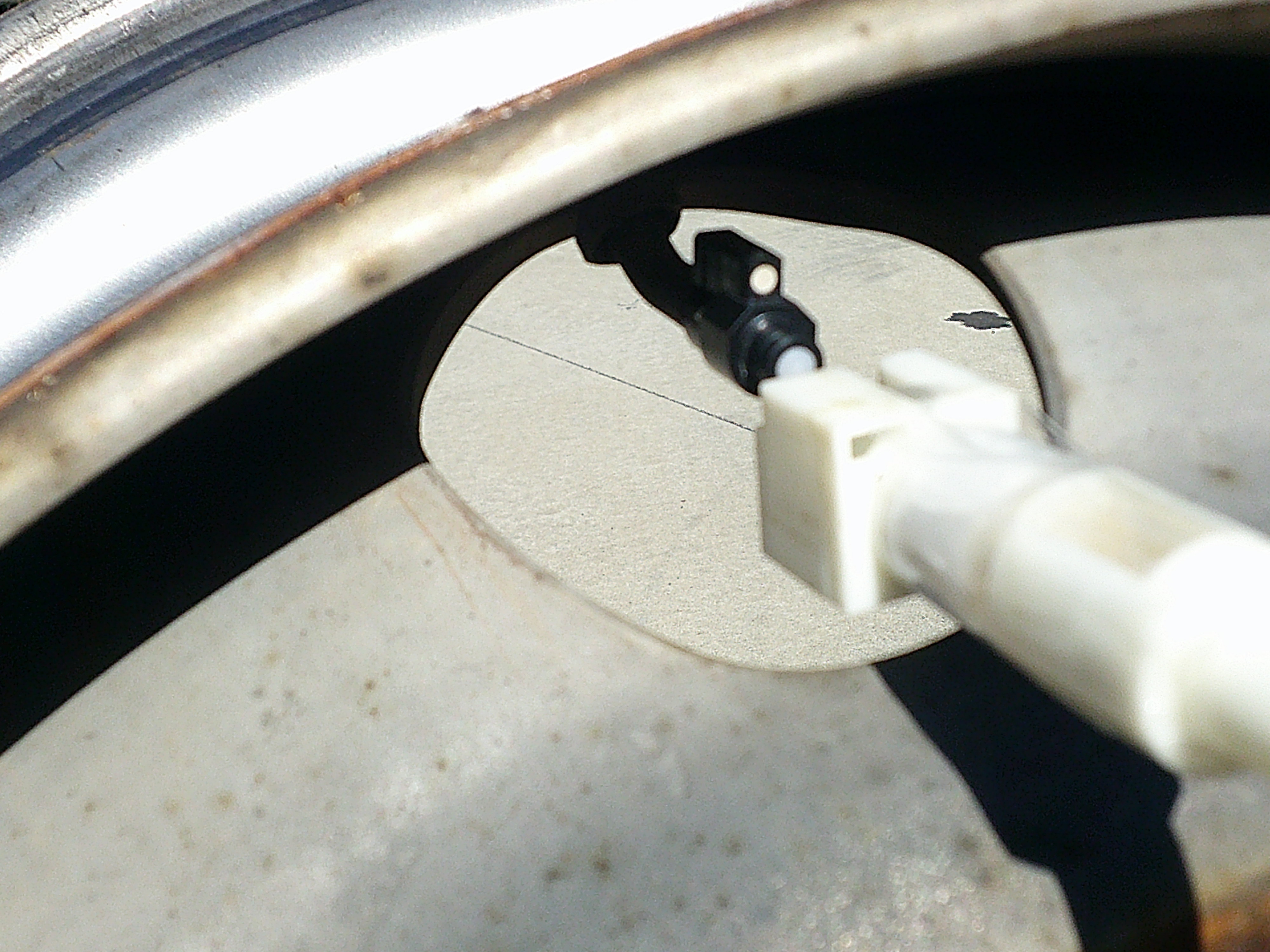

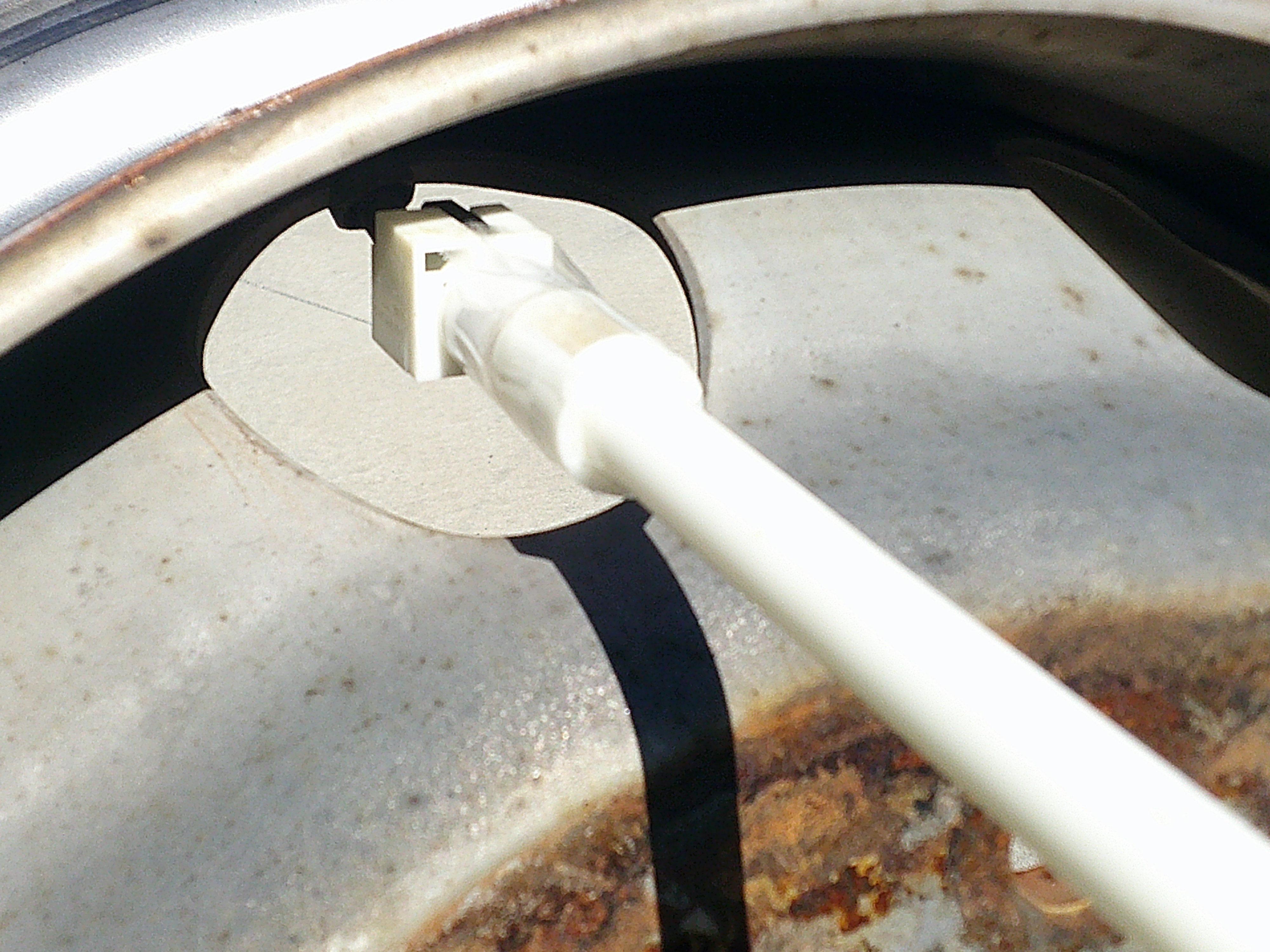
When docking the tip to the main body with the handle, just press a little hard and
the ultra-bright LED display will automatically appear.
(2) Double tyre inside:
The method is exactly the same as in the case of Single tyre. However, since it is a
double tyre, the length of the handle handle is only longer by one wheel. The handle is
used in the state of extension.
The next photo is of The Main Body mounted on the Air Valve on
the inside of the Double Tyres rear wheel. One wheel, it is in the
back, but the main body is clearly visible. For this purpose, a
white round mark is attached to the black body.
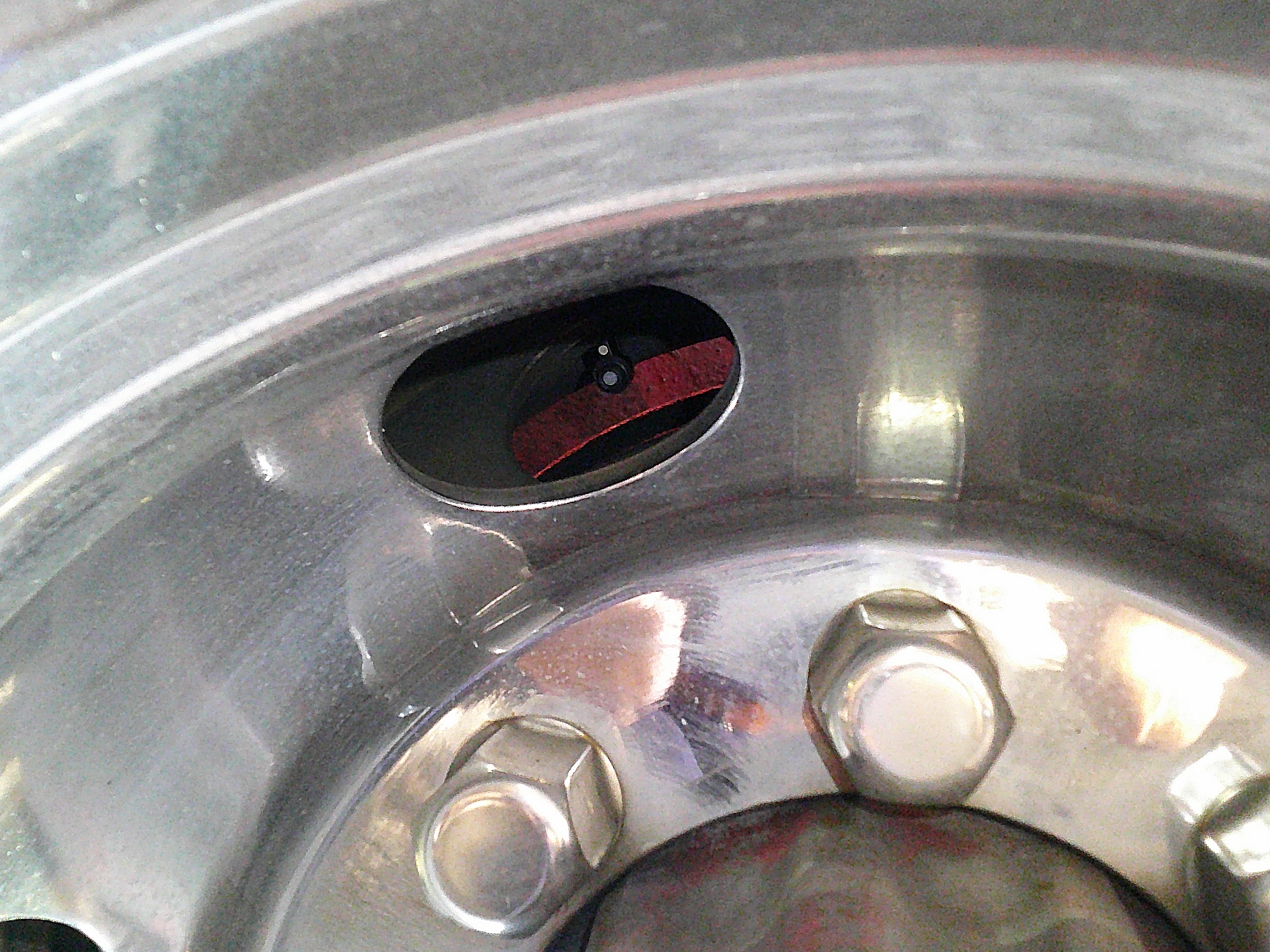
In order to dock with this main body, insert the handle unit in the extension state into
the large hole where the air valve is. What you can see in the photo is the tip of the
handle unit. Photo is taken with the handle unit removed. This is because if I hold the
Extension handle unit, I can't take a picture of the scene where the handle unit gets in
the way and docks with the main body.
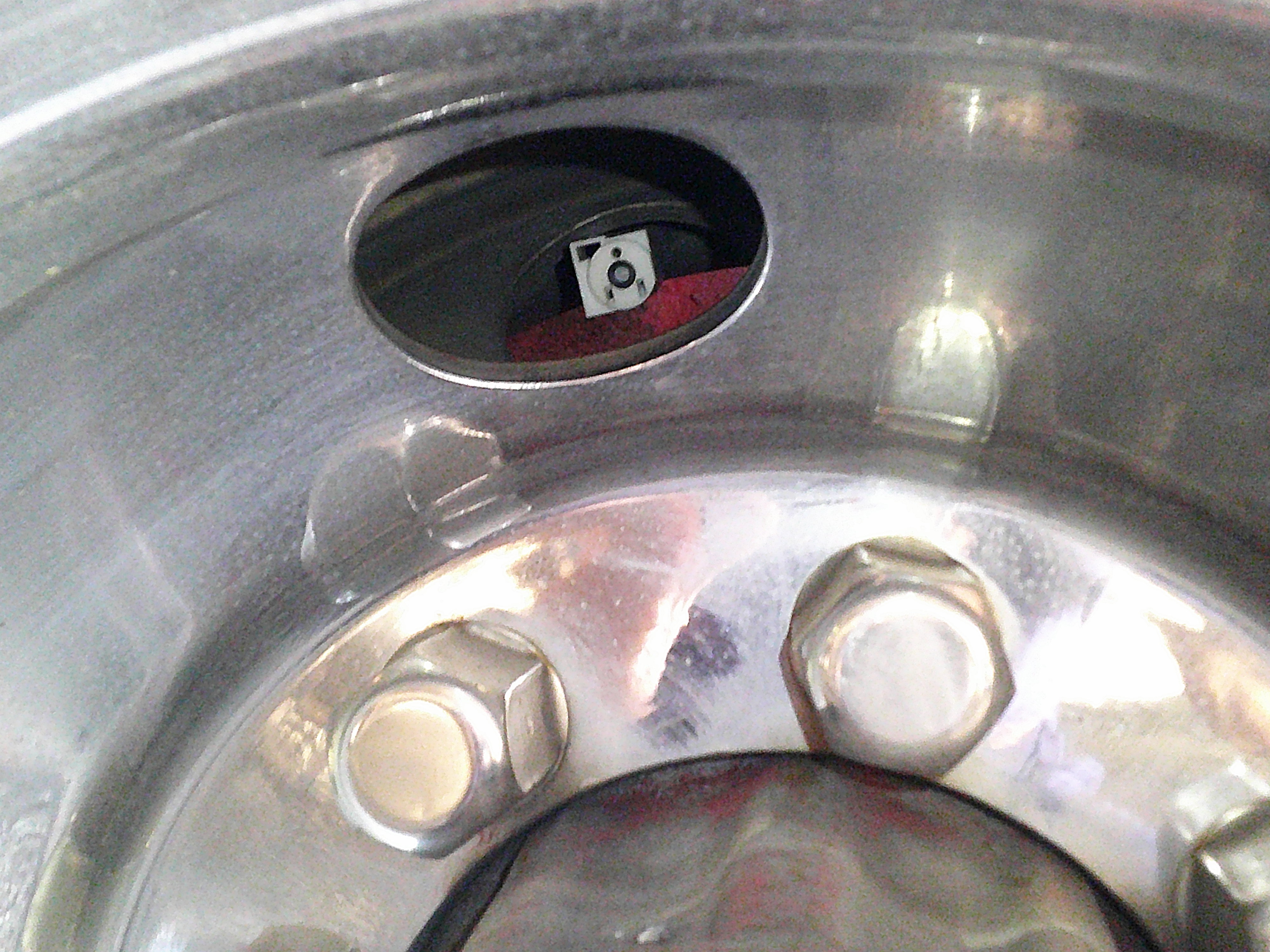
(3) Double tyre outside:
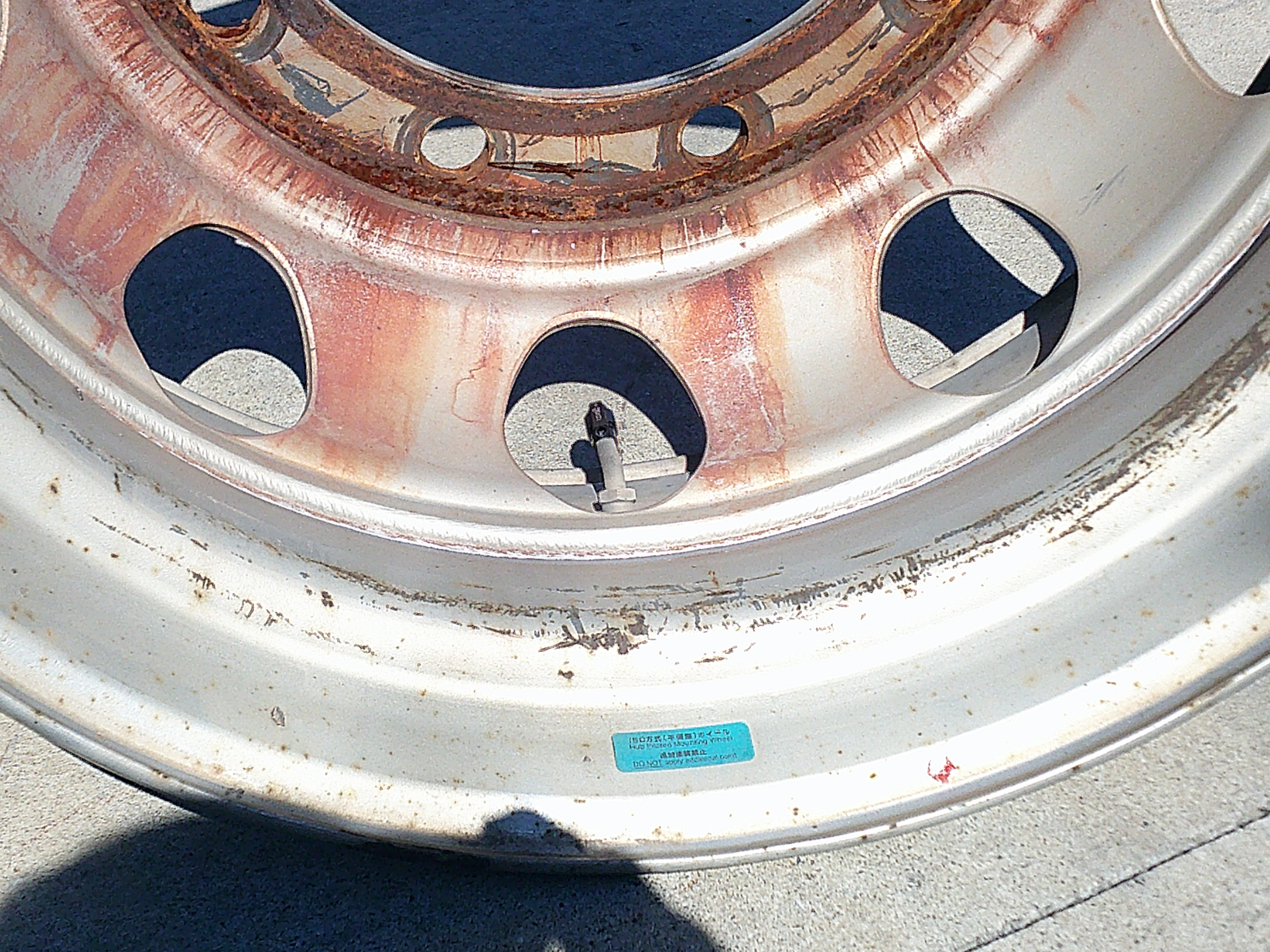
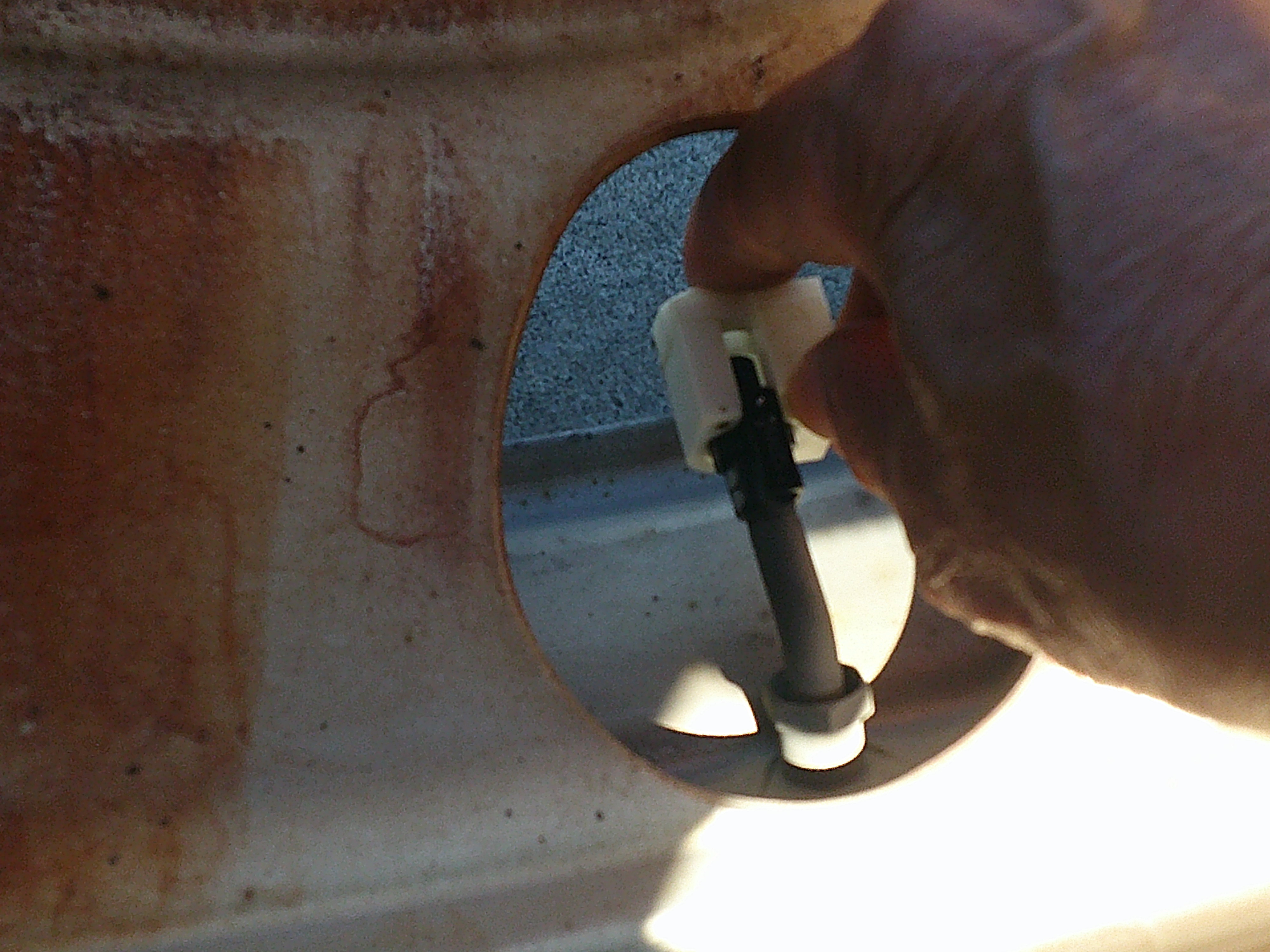

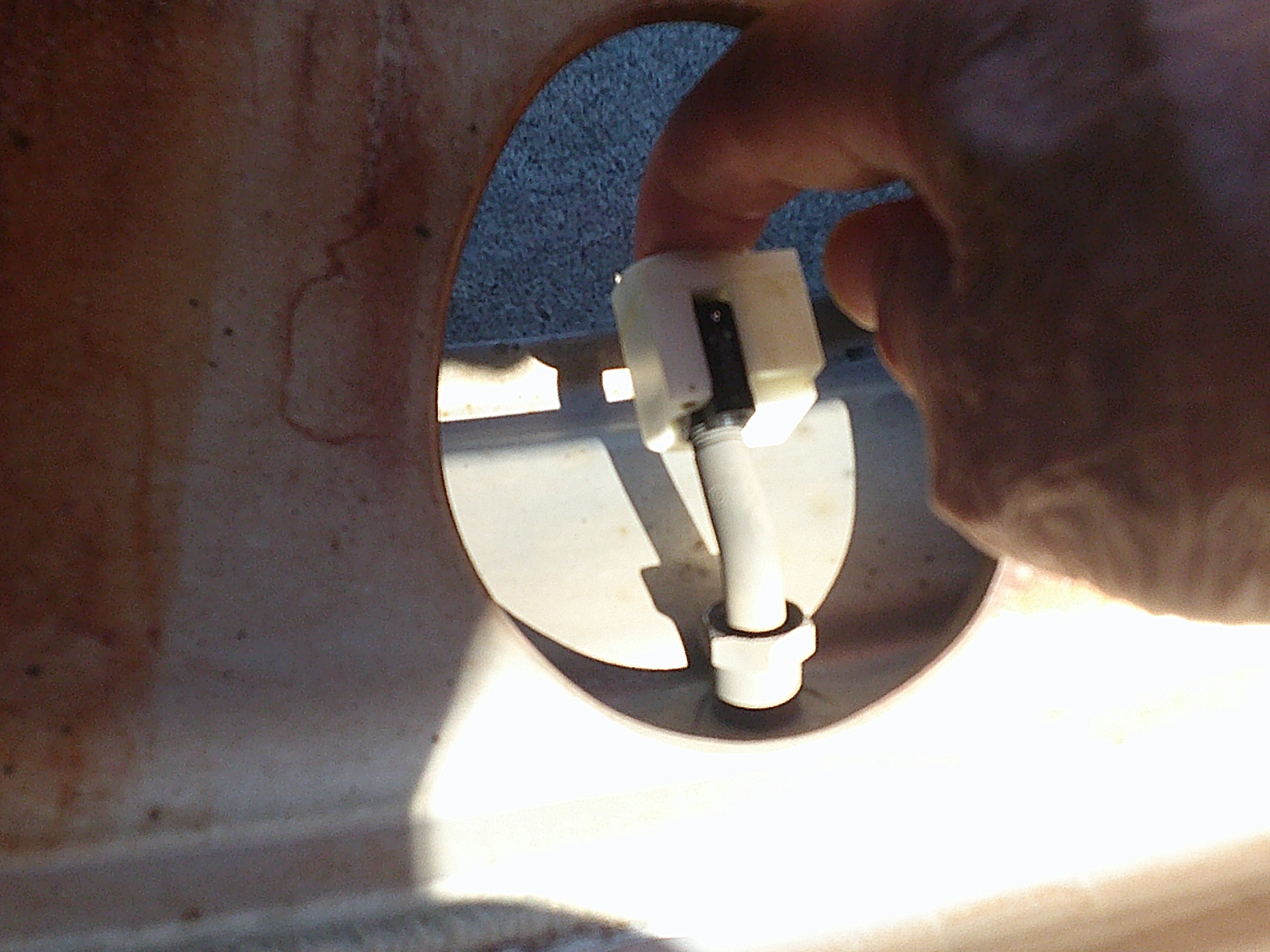
The reason why the ultra-bright LED display is automatically displayed the single tyre or
double tyre inside is that when the handle is pressed, from the air valve air enters the
cylinder of the main body, and the cylinder is pressured to detect its position. However,
in the case of Double tyre outside, instead of Handle, we need to press it with our fin-
gertip. This is for safety reasons. Our tyre checker is designed so that it does not
touch the core of the Air Valve. In the unlikely event that the tyre checker is damaged
due to force majeure, this is even to maintain the tyre pressure normally.
(4) Conducting winter tests:
With the prototype tyre checker:
With the completion of the prototype, I decided to test it while actually driving it on a truck and
evaluate the product. What time of year is the most suitable for the test? Of course, this is the
toughest time. That's the harshest environment for a product, meaning the cold of the winter.
If it passes, there is no problem at all at other times. Therefore, I set the test date to February
5th-11th, 2011. We asked Saito Transport Co., Ltd., which was previously introduced by the head
office of Tokyo Dunlop Tire, to cooperate with the test in Kitami City, Hokkaido. I booked a business
hotel. Needless to say, the plane ticket procedure has been completed, and tomorrow is the day
before I will finally leave Tokyo for Kitami, Hokkaido. I should have gone to bed earlier without
doing anything extra, but I tried to manipulate the lights on the tyre checker many times. This is
not a finished product, but a prototype. While I was touching it, my fingers swung where I
shouldn't have touched, and a malfunction occurred. The LED light suddenly went out. I looked
at the clock and it was past 10 p.m. I can't do anything about it. I had no choice but to call a friend
of mine who is also an expert in weak electricity and a designer of communication equipment. He
runs his own company. When he heard my story, said: "Anything can be done with electricity.
So there's nothing to worry about. However, when it comes to mechanics, it is not an easy
task. That's the only thing we need to make sure about" As expected, the designer. His judge-
ment is accurate. I was comforted by his words, and I was able to go to the test, to Hokkai-
do, where the bitter cold awaits.
(1) Test Report:
As for the electrical aspects, due to my mistake, I was unable to do the test, so I will describe the
mechanical aspect and my impressions:
(a)Strength: As designed by Takanori, the main body did its job well, withstanding the high
pressure of truck tyres.
(b)Insertion Tip Unit into Main Body: Both the front and rear wheels docked well.
(c)Inflating from the main body into the tyres: It is an absolutely necessary function for
replenishing air, but it played the role of that function.
With the exception of electricity, all other functions worked well. Mechanically, I'm very satisfied.
In particular, My heart was pounding when I saw the air in the tyres from the tyre checker,
the main body. Then, involuntarily, I almost shouted to Mr. Walenga that I had finally suc-
ceeded. I think that no one can imagine our mechanism. And, I concludes the test report with
satisfaction.
12) Tyre Checker Development History:
We have developed a total of five types of tyre checkers, for each model, there are various
memories. We can't commercialize it right now, but we hope to have the opportunity to do so in
the near future. A lot of time has passed, and the world has changed so much that you may won-
der if there is really a demand.
Absolutely. Even now, I don't think there is a company that has enough technology and ideas to
surpass ours. And most of all, we know that even Dunlop tires will be available to the world soon.
The amount of air consumption to measure tyre pressure is large, and it is not at the level
of 1cc like our product. And, best of all, tyre gauges have never been improved since they were
invented. It's just that the way it is measured has changed. Nothing has changed in the underlying
problem. It is unfortunate that we were not able to commercialize the product, but if we can find
the funds, we intend to commercialize it with our own funds.
Finally, I will reintroduce the models from No. 1 to No. 5 so far, and end the Tyre Checker
page. As for the Model No.5, in order to make the shape compact, it is the first product to
be used as a separate type instead of an integrated type. The main body was designed by
Takanori, but, lack of funds, the measuring device part was designed by myself who has not any technology or design experience. This is to use the best knowledge I have gained from
Mt. Guy J. Walenga to see in any way the potential of a tyre checker that can inflate tyres
directly. Therefore, please forgive me for the fact that the design and function of the measure-
ment part is the work of a complete amateur. In fact, when we commercialize it, we ask ex-
perts to do it, so I am confident that it will be an even better product. This time, I would be very
happy if you could only look at the functional aspects. And I would like you to pay attention to
the fact that we have actually completed a tyre checker that can easily check the air pres-
sure of truck tyres by inflating directly from the tyre checker, even though it is a prototype.
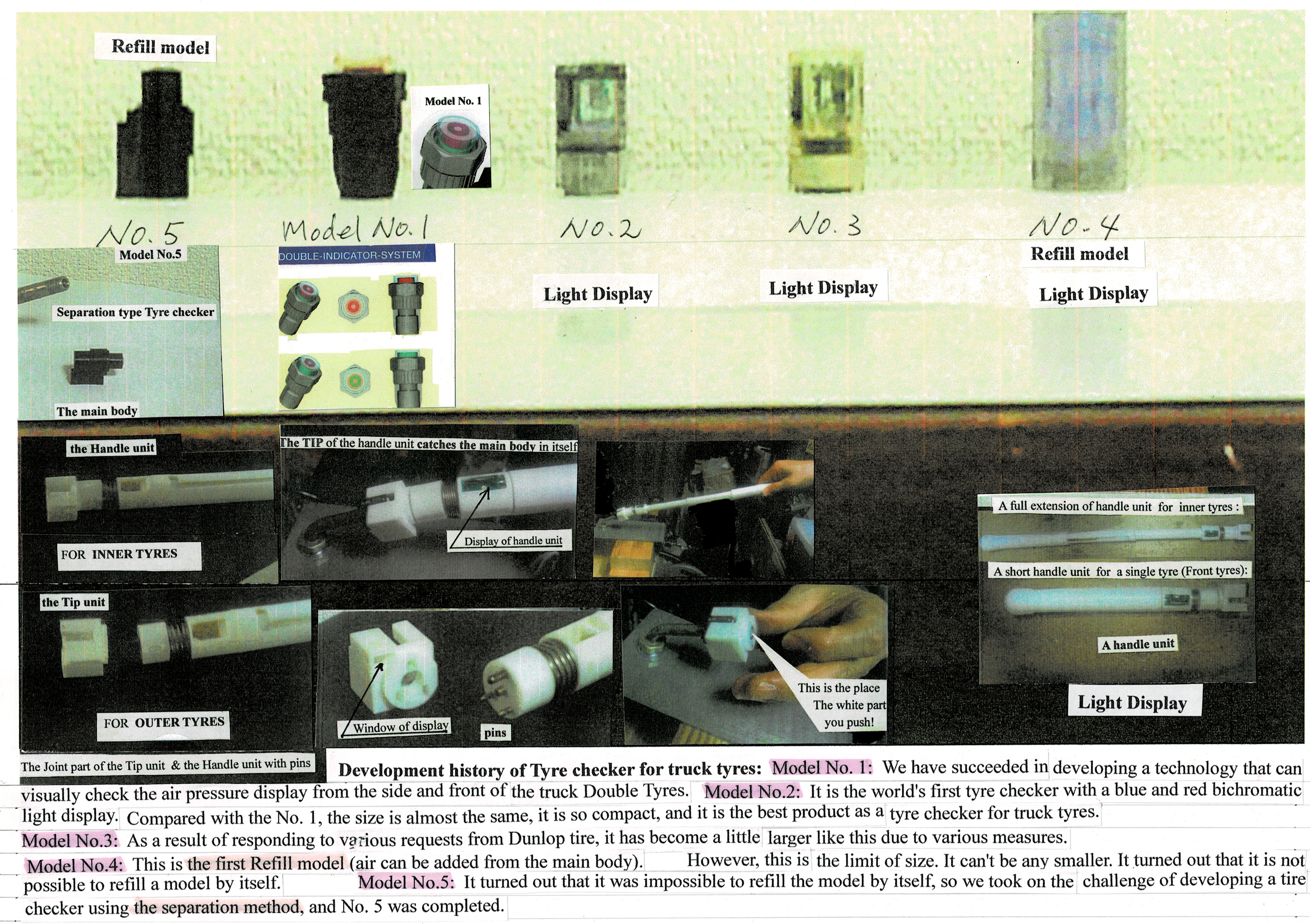
Chapter 4:
This earthquake woke me up to complete SELLA TSP:.
The earthquake that occurred on March 11, 2011 was a huge one with a magnitude of 9.0,
the largest earthquake ever recorded in Japan. This huge earthquake caused a huge tsuna-
mi that engulfed the lives of many people. No one knows what tomorrow will bring. And I
realized that even my life was not guaranteed. Therefore, I decided to concentrate every-
thing on the completion of SELLA TSP, which is the biggest last challenge left for me. I did
not think about development funding any more. I thought only about research, and at
worst, I was prepared to do research in extreme poverty. Otherwise, I would have done
nothing in my life. This incident was like a heavenly outrage at my unmanly attitude, which
was trying to justify my inability to work on the development of SELLA TSP by using the
lack of funding as an excuse. Didn't Benjamin Franklin say that heaven helps those who
help themselves? First of all, if I don't work hard for that purpose, who will help me? Even
heaven won't help me.
1)Make the SELLA the only priority in life :
(1) I rented a cheap apartment and set up the development conditions as much as possible so that
I could live without going into debt further.
(2) Second, the special Aramid fiber costs as much as USD80/kg. Also, the special chemicals I need
cost USD50/kg. In addition, various other chemicals are required for the experiment, but there is
no money to purchase them. Therefore, I talked to Teijin Co., Ltd., a listed company, and other
companies about our purpose and asked for their cooperation in providing free samples. Consider-
ing that we are a company that has applied for many patents, they were willing to cooperate with us, expecting our development capabilities.
(3) With this, the environment for development is ready. I kept the experimental equipment to a
minimum, and I will rent centrifuges and viscometers at an industrial test centre for a fee. Because
high-performance equipment is required to obtain the final data, but I couldn't afford to buy them.
2) My attempt on No separation product:
How can we make a product in which the fiber and the chemical aqueous solution do not
separate?:
(1) The most common answer is that the specific gravity of the fiber and the specific gravity of
the chemical aqueous solution should be the same. This idea is theoretically correct. However
even if research is conducted according to this concept, it is impossible to realize the product. Why
is it that among the many U.S. puncture inhibitor manufacturers, only US Tire-tech has succeeded
in producing it? That says it all. And from my experience, I think it is. Of course, this is not the first
attempt. I've been experimenting for several years in total. Without such knowledge of the past, it
is impossible to move forward. At first, as the title suggests, I planned to solve the problem of non-
separating products, and then proceed with our research to solve the next problem of wheel rust.
However, in 2012, I changed my policy and decided to study the problem of wheel rust at the
same time. Why? Unlike the mechanism, it was difficult to proceed in order, and I knew that I
could not proceed at all unless I experimented with it, and I felt a sense of crisis that I could not
read the time unless I proceeded at the same time.
3) Solving the Wheel Rust Problem:
Which is more difficult, the development of no separation product, or the solution of the wheel
rust problem? The answer, of course, is wheel rust. Why? No separation product has already been
developed by US Tire-tech. However, to the wheel rust problem, Dupont, the world's largest
chemical company, was unable to do anything about, even though they determined to sell its
products to the global market. Therefore, there is no technology to solve the problem of wheel
rust worldwide. As for wheel rust, first, I asked the secretary general of the rust inhibitor industry
to introduce me the best engineer in Japan. I thought that perhaps they could solve it. Because
they have a lot of knowledge as experts in rust inhibitors, I had a faint hope that if I explained the
situation in detail, they might be able to find a solution. He then introduced me to Mr. Kazuhiko
Arimatsu as the best rust inhibitor technician in Japan. I went to see him as far away as
Yokkaichi City in Mie Prefecture. He was a Technical Adviser at Chubu Chelest Co., Ltd. Our discus-
sion included Mr. Morooka, who is the Section Manager of New product development section, was
also present. I explained the terms of use in as much detail as possible to make it easier for them
to develop, and I told them what the biggest problem was. The talks went well. They didn't reject
me for being particularly difficult. I had a little bit of anticipation for them. At a later date, they re-
ported the results of their study. The answer was that they couldn't do it. Hearing their results,
of course, I was shocked to see my modest hopes dashed. But this is where my work begins.
First of all, why can't they make the rust inhibitor I want? I must clearly understand the reason
for this. This is because I have no knowledge of rust inhibitors. And I know from many years of
experience that the shortest way is to ask an expert who knows more about rust inhibitors
than anyone else why it is not possible to do it, rather than reading a specialized book on rust
inhibitors. This allows me to spend less time on unnecessary things, and more time on problems.
For this reason, I went to see Mr. Arimatsu again. And I clearly understood that the current
anti-rust technology could not solve the problem of wheel rust. The current mechanism of
the rust inhibitor is based on the condition that the metal that requires rust prevention is always
in contact with an aqueous solution containing the rust inhibitor. Therefore, the SELLA TSP
is not in constant contact with the wheel, the prerequisites are different. During driving, cen-
trifugal force causes the SELLA TSP to cover the tread part with a thin layer. When stopped,
gravity causes the SELLA to accumulate at the bottom of the tyre. The chance for SELLA to
come into contact with the wheel is when the vehicle starts to move from a standstill or
from running to a standstill, when the centrifugal force is small. There is no rust inhibitor tech-
nology in the world that satisfies the conditions. The full extent of the problem has become clear.
Now I can walk straight towards my goal without making a mistake in solving the problem. It was
worth it to meet the best rust inhibitor technician in Japan. For this alone, I have to thank
Heaven. From now on, development begins by thinking about how to solve this problem. What-
ever it takes, I have to find a way to do it.
4) Finding a solution to wheel rust problem:
At last, in my head, the idea came into being organized as a theory. And I was convinced that
I could do this. However, I am a novice when it comes to rust inhibitors. Again I visited Mr. Ari-
matsu, one of the best rust inhibitor technicians in Japan. The purpose of my visit is to hear his
opinion as an expert. In the eyes of experts, doing something that is not possible is a waste of
time and money. Also, in my theory, if there is a mistake, it is to see where it is wrong. I told him
the purpose of my visit and explained my theory. And I asked for his views on my theory. To my
surprise, his views affirmed and complimented my ideas. he assured me that it would work
. My heart was filled with joy. The best rust inhibitor experts in Japan evaluated and complimented
my theory. And he assured me that I would succeed. All I have to do is solve the problem
through experimentation. I sincerely thanked him for his cooperation. Immediately, based on
theory, I started experimenting with a new method that would not only prevent wheel rust, but
also solve the problem of wheels that were already rusty. Why did I focus my research not
only on rust prevention, but also on already rusted wheels? I have already investigated
what kind of specifications should be used as a rust inhibitor for SELLA TSP. And the results of the
survey show that it cannot be commercialized with a mere rust inhibitor. This is because summer
tyres are replaced with winter tyres. Winter tyres were replaced with summer tyres. The tyre
replacement period coincides with the same time for all vehicles, and the tyre shops have to
deal with it on an overcrowded schedule, there is no time to carefully remove the rust from
the wheels. Therefore, even if the wheel is already somewhat rusted, if the damage of rust
can not be prevented, it will have no product value. Rust(red rust) erodes metals.
Therefore, this is a serious safety issue. This is because it's directly linked to a major accident
. So, how do I solve it? My method is to stop the erosion of the metal by changing the red rust
that is already eroding the wheel with rust to black rust. Black rust does not erode metals.
And it is a rust inhibitor that prevents further erosion of the metal. All of these functions are
performed automatically inside the sealed tyre. For your information, red rust is ferric oxide.
And black rust is 4 iron oxide. When an oxide film is formed on the surface of iron, the oc-
currence of red rust can be suppressed. Triiron tetraoxide does not occur naturally, so it must
be artificially produced. Of course, SELLA TSP's rust inhibitor cannot restore the rust state to its
original state. However, even if the wheel is somewhat rusty, it will change the red rust to
black rust to stop erosion and maintain the strength of the wheel, contributing to safe driv-
ing. All of the developments I have undertaken so far have been the first of their kind in the world.
Therefore, there is no successful attempt on the first try. This time is no different. Even if the theo-
ry is completed, once the rust inhibitor enters into the tyre, nothing can be done from the
outside. The hardest thing for me was figuring out how to make this function work automatically
from the moment it was manufactured. But it is to make it work, regardless of time. I am truly de-
lighted to have been able to develop this product for the first time in the world. Testing continued
ending in 2015. And the development was completed successfully.
5) The final battle against no separation product:
As many people say, the idea that the specific gravity of a fiber should be the same as that of an
aqueous chemical solution was not possible was concluded many years ago. This is because I have
made countless mistakes. And empirically, I knew that this idea was not realistic. So what are the
possible methods? I've already found a way to do that. When it comes to wheel rust, the basic
theory is introduced. However, I will follow US Tire-Tech's lead and keep the No separation product
a trade secret. Since 1996, we have been investigating the cause of the extension of Tyre life, and
of course, we have been researching the manufacturing method of the No separation product.
Difficult problems cannot be solved in a short period of time. It would be a different story if we had
a theory of the manufacturing method, but since there is no theory, the only way is to collect
data through repeated trial and error. When it comes to wheel rust, the basic theory is intro-
duced. However, we can't do any theory without basic knowledge or data. If you think it's
natural, you're right. Because science is just doing the obvious. In other words, contrary to the
principles of eternity, we can never achieve our goals. And I had a choice to make. I identified a
substance that US Tire-Tech was using. However, I found a much better substance in Japan
products. But, the price is more than five times higher. And I decided to use Japan products.
This is to demand high quality from SELLA TSP.
6) Special Notice:
I'm pleased to share with you the good news. It was patented by SELLA TSP.
SELLA TSP has been officially granted a patent as "Tyre Life Extender".
As someone who has been working on this issue for many years, I am very
happy to announce that.
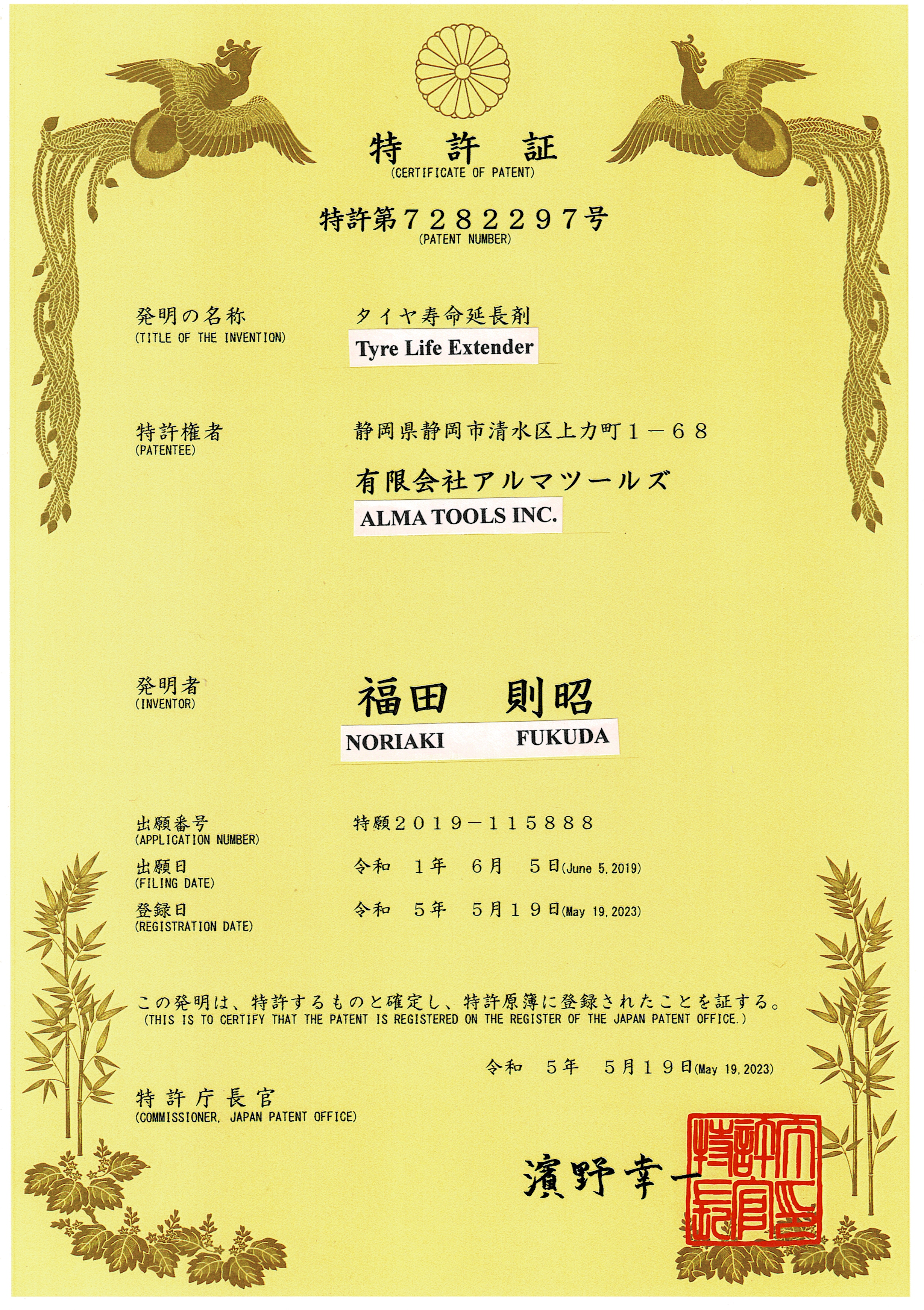
PAT No.7282297 May 19, 2023 Tyre Life Extender
|
|